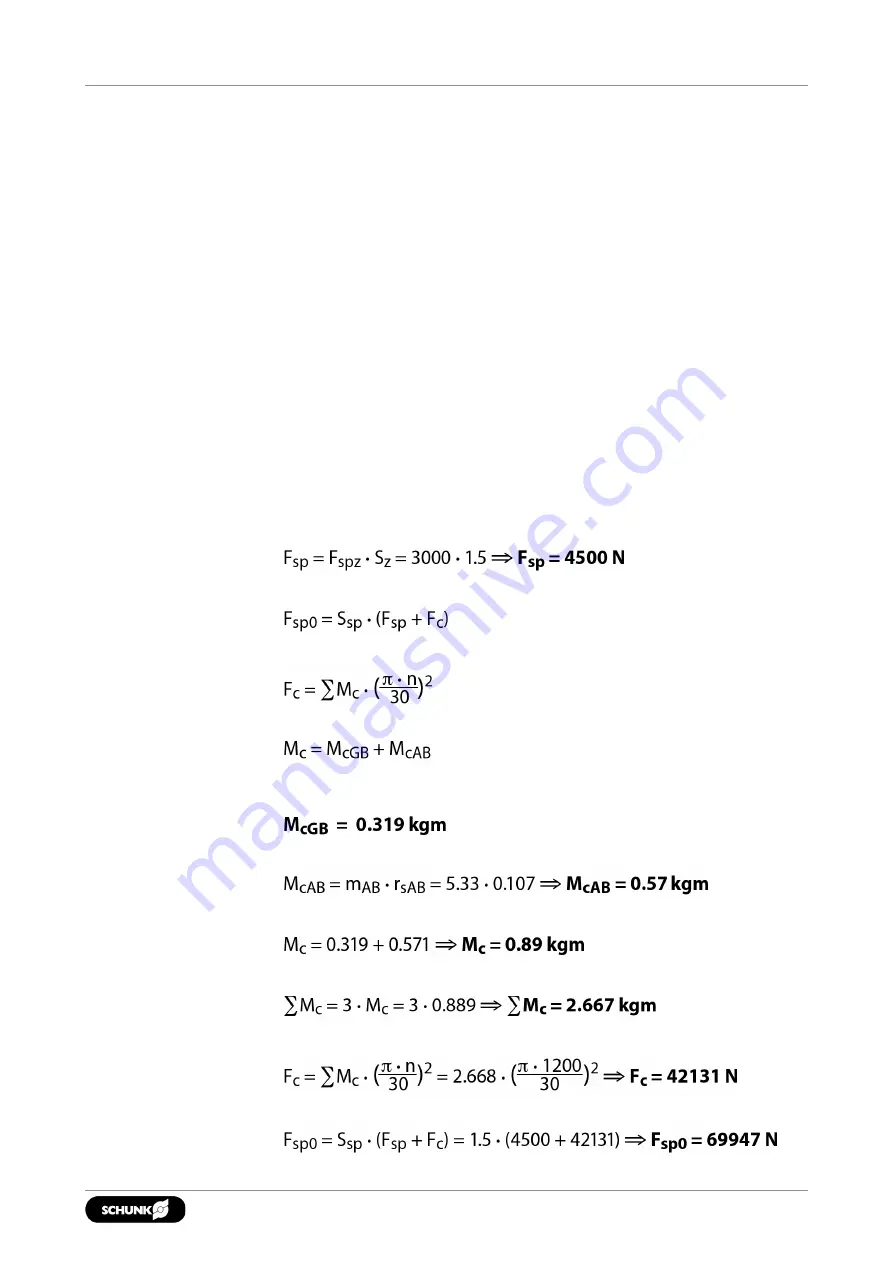
Technical data
3.3.2 Calculation example: Required initial clamping force Fsp0 for a
given rpm n
The following data is known for the machining job:
• Gripping from the outside in (application-specific)
• Machining force F
spz
= 3000 N (application-specific)
• max. speed of rotation n
max
= 3200
rpm
("Chuck data" table)
• RPM n = 1200
rpm
(application-specific)
• Mass of one (!) top jaw m
AB
= 5.33 kg (application-
specific)
• Center of gravity radius of top jaw r
sAB
= 0.107 m (application-
specific)
• Safety factor S
z
= 1.5 (according to VDI 3106)
• Safety factor S
sp
= 1.5 (according to VDI 3106)
Note:
Masses of the jaw mounting screws and T-nuts are not taken
into account.
First the required effective clamping force F
sp
is calculated using
the machining force stated:
Initial clamping force during shutdown:
Calculation of total centrifugal force:
For two-part chuck jaws, the following applies:
Centrifugal torque of base jaw and top jaw specified in "Chuck
data" table:
For the centrifugal torque of the top jaw, the following applies:
Centrifugal torque for one jaw:
The chuck has 3 jaws, the total centrifugal torque is:
The total centrifugal force can now be calculated:
Initial clamping force during shutdown that was sought:
23
06.00 | ROTA THW3 | Power Chuck | en | 1440828
Summary of Contents for ROTA THW3
Page 1: ...Translation of Original Operating Manual Power Chuck ROTA THW3 Assembly and Operating Manual ...
Page 46: ...Drawing 46 06 00 ROTA THW3 Power Chuck en 1440828 9 Drawing Full chuck Accessories ...
Page 47: ...Drawing Thrust jaw 47 06 00 ROTA THW3 Power Chuck en 1440828 ...
Page 48: ...Drawing 48 06 00 ROTA THW3 Power Chuck en 1440828 Mount ...
Page 49: ...Drawing Thread lock with Klemm tight 49 06 00 ROTA THW3 Power Chuck en 1440828 ...
Page 54: ......
Page 55: ......