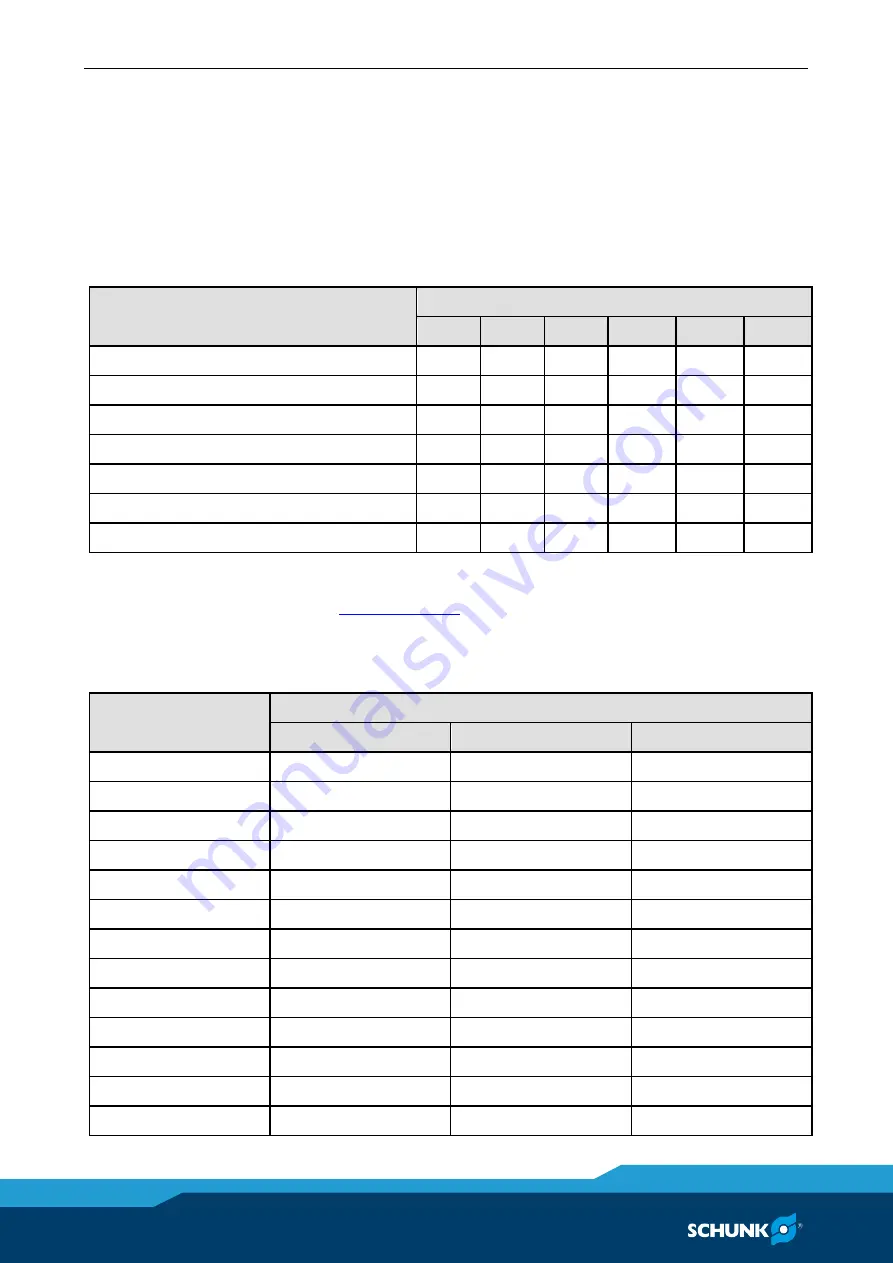
Technical data
14
02.00|KSPplus-BWM KSP-LHplus-BWM |en
Technical data
Installation position
variable
Operating temperature
5 °C – 60 °C
Noise emission [dB(A)]
≤ 70
Pressure medium
Compressed air, compressed air quality according to
ISO 8573-1:7 4 4
Designation
KSP plus-BWM KSP-LH plus-BWM
100
160
250
LH 100 LH 160 LH 250
Stroke per jaw [mm]
2
3
5
6
8
15
Clamping force* at max. pressure [kN] 18
45
55
8
20
20
max. pressure**
9
9
9
9
9
9
Repeatability [mm]***
0.01
0.02
0.03
0.01
0.02
0.03
Repeat accuracy [mm]
0.02
0.02
0.02
0.02
0.02
0.02
max. jaw height [mm]
35
55
70
35
55
70
Weight [kg]
4
11.6
34.5
4
11.7
34.6
*
Clamping force is the arithmetic sum of the individual forces occuring at the jaw,
** When using an ABP-A base plate, the maximum pressure must be limited to
7 bar
.
*** After 100 consecutive strokes to end positions.
Dimension
KSP plus-BWM KSP-LH plus-BWM
100
160
250
A
90
146
230
B
64
106
154
Ø C
6H7 x 12
8H7 x 14
10H7 x 20
D
80
125
200
E
29.5
50
75
F
32
40
64
G
34.5
59.7
92.6
H
55
82
139.6
I
64
104
170
J
70
83
98
K
42
45
52
L
10
15
20
M
59
100
150
5