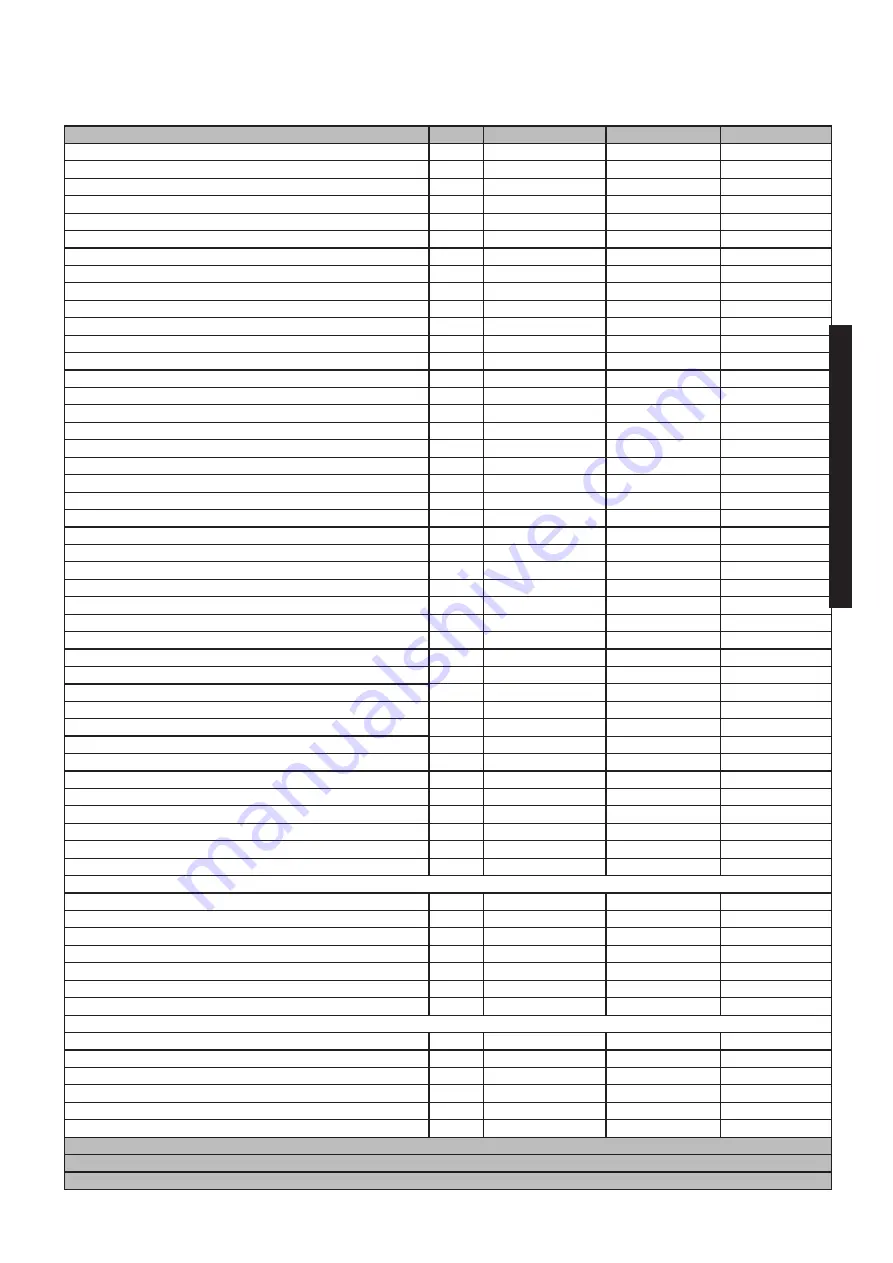
13
13
Technical Features
BWA R 50 c
BWA R 70
Appliance category
II
2H3P
II
2H3P
Modulation Ratio
1:5
1:7
Nominal Heat Input on P.C.I. Qn
kW
48,5
67,5
Minimum Heat Input on P.C.I. Qmin
kW
9,6
9,6
Nominal Output (Tr 60 / Tm 80 °C) Pn
kW
47,2
65,5
Minimum Output (Tr 60 / Tm 80 °C) Pn min
kW
9,1
9,1
Nominal Output (Tr 30 / Tm 50 °C) Pcond
kW
49,3
68,5
Minimum Output (Tr 30 / Tm 50 °C) Pcond min
kW
10,3
10,3
Efficiency at max. output (Tr 60 / Tm 80°C)
%
97,29
97,29
Efficiency at min. output (Tr 60 / Tm 80°C)
%
94,9
94,9
Efficiency at max. output (Tr 30 / Tm 50°C))
%
101,62
101,51
Efficiency at min. output (Tr 30 / Tm 50°C)
%
104,3
104,3
Rendimento al 30% del carico (Tr 30°C)
%
107,33
107,33
Number of stars (according to 92/42 EEC)
Combustion efficiency with nominal load
%
97,80
97,41
Combustion efficiency with minimum load
%
98,42
98,42
Heat loss at casing with burner in operation (Qmin)
%
3,61
3,61
Heat loss at casing with burner in operation (Qn)
%
0,51
0,12
Stand-by losses (with ∆t 30°C)
%
0,2
0,2
Flue gas temperature tf-ta (min)(**)
°C
33
33
Flue gas temperature tf-ta (max)(**)
°C
43,6
51,3
Flue gas mass flow rate (min)
kg/h
15,9
15,9
Flue gas mass flow rate (max)
kg/h
80,0
111,4
Excess λ air
%
26,84
20,57
(***) CO
2
(min/max)
%
9,0- 9,2
9,5 - 9,5
Flue losses with burner in operation (min)
%
1,58
1,58
Flue losses with burner in operation (max)
%
2,20
2,59
Flue losses with burner off (depression “0”)
%
0,2
0,2
Portata d’acqua alla potenza nominale (∆T 15°C)
l/h
2837
3927
Portata d’acqua alla potenza nominale (∆T 20°C)
l/h
2120
2946
Minimum heating circuit pressure
bar
0,5
0,5
Maximum heating circuit pressure
bar
6
6
Max allowable pressure of the generator
bar
8
8
Water content
l
3,9
3,9
Gas Consumption Natural (20 mbar) gas G 20 a Qn
m
3
/h
5,13
7,14
Gas Consumption Natural gas (20 mbar) G 20 a Qmin
m
3
/h
1,02
1,02
Gas Consumption G25 (supply pressure 25 mbar) Qn
m
3
/h
Gas Consumption G25 (supply pressure 25 mbar) Qmin
m
3
/h
Gas Consumption G31 (supply pressure 37/50 mbar)
Qn
kg/h
3,76
5,24
Gas Consumption G31 (supply pressure 37/50 mbar)
Qmin
kg/h
0,75
0,75
Max. available pressure at the chimney base
Pa
40
40
Condensate production max
kg/h
7,8
10,87
Emissioni
CO at Minimum Heat Input with 0% of O2
mg/kWh
19,7
19,7
NOx at Nominal Heat Input with 0% of O2
mg/kWh
68
68
NOx at Minimum Heat Input with 0% of O2
mg/kWh
37
37
NOx Weighted value according EN 15420)
mg/kWh
33,9
34,68
NOx Class
5
5
Electrical Data
Voltage/Frequency electric power supply
V/Hz
230/50
230/50
Fuse on main supply
A (R)
4
4
Maximum absorbed output
W
172
290
Minimum absorbed output
W
77
145
Standby Consumption
W
16
16
Insulation degree
IP
X4D
X4D
(*) (*) Room Temperature = 20°C
(**) Temperatures detected with the unit in operation
(Tr 60 / Tm 80°C)
(***) See table INJECTORS PRESSURES
2.5 - OPERATING DATA ACCORDING TO UNI 10348 and GENERAL FEATUREs
For the adjustment data: NOZZLES - PRESSURE - DIAGRAMS - FLOW RATES - CONSUMPTION refer to the paragraph ADAP
-
TATION TO OTHER TYPES OF GAS.
Summary of Contents for BWA R50
Page 1: ...INSTALLATION AND SERVICING MANUAL R 50 R 70 BWA R 50 R 70 ...
Page 2: ...2 ...
Page 20: ...20 DOUBLE Ø 80 ...
Page 39: ......