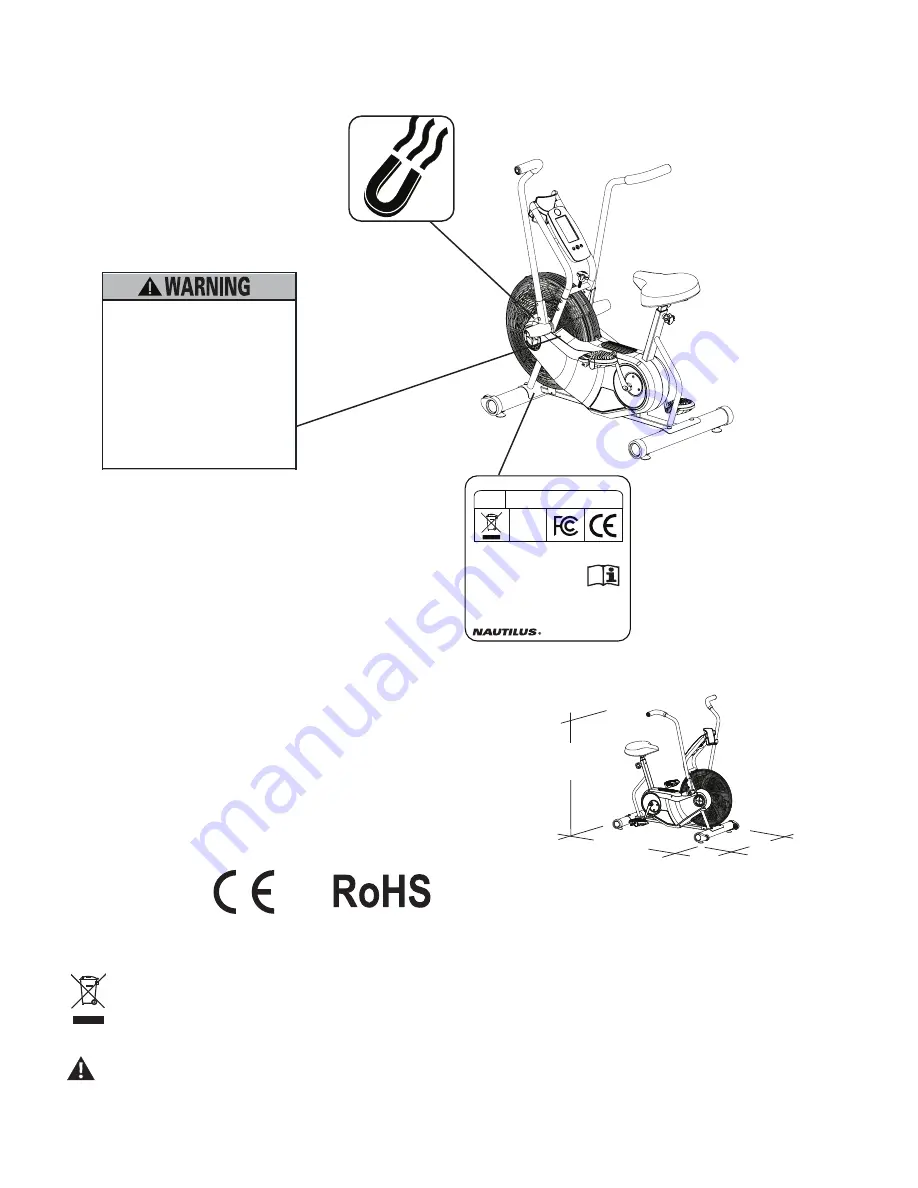
3
SAFETY WARNING LABELS AND SERIAL NUMBER
Reading the Serial Number
The instructions below show how to decode the information
contained on the serial number.
Serial Number
AAAAAAA
Nautilus part number (SKU)
BBB
Vendor Code
PPPPPP
Purchase Order Number
LL
Purchase Order Line Number
CCCCCC
Unique Identifier
Machine Weight:
115 lbs. (52.2 kg)
Power Requirements:
2 AA Batteries
Operating Voltage:
1.0 - 3.3VDC
Maximum User Weight:
300 lbs. (136 kg)
Regulatory Approvals:
This product conforms to the applicable EN ISO 20957 International Standards for Stationary Training Equipment, Class S
DO NOT dispose of this product as refuse. This product is to be recycled. For information on the proper method of
disposal, contact a Nautilus Customer Service Representative. Contact information is available in the Contacts
section in this manual.
This product, its packaging, and components contain chemicals known to the State of California to cause
cancer, birth defects, or reproductive harm. This Notice is provided in accordance with California’s Proposi-
tion 65. If you would like additional information, please refer to our website at www.nautilus.com/prop65.
50.9”
(129.2 cm)
25.7”
(65.2 cm)
49.7”
(126.3 cm)
REVISIONS
ECO
REVISION
REV DESCRIPTION
APPROVED
DATE
TITLE.
PART NO.
REV.
SHEET 1 OF 1
SCALE: 1:1
DO NOT SCALE DRAWING
1. ALL ITEMS MUST BE RoHS COMPLIANT
2. ALL DIMENSIONS APPLY BEFORE PLATING OR COATING.
3. REMOVE ALL BURRS, BREAK SHARP EDGES 0.5 MM MAX.
4. ALL MACHINES SURFACES Ra 3.2 uM.
5. ALL APPLICABLE NAUTILUS STANDARDS AND
SPECIFICATIONS APPLY.
6. ALL DIMENSIONS ARE IN MILLIMETERS
7. ALL DUAL DIMENSIONS ARE IN INCH
UNLESS OTHERWISE SPECIFIED:
METRIC
THIRD ANGLE
PROJECTION
INTERPRET DIMENSIONS AND TOLERANCES
PER ASME Y14.5M - 1994
2.5
1.5
0.75
0.25
1°
X.
X.X
X.XX
X.XXX
ANGULAR
C
SIZE
TOLERANCES.
DRAWN
DESIGNED
DATE
METRIC_C_REV G
NAUTILUS, INC.
16400 SE NAUTILUS DRIVE, VANCOUVER, WA 98683
LIFECYCLE
12-20-2011
APPROVALS
- -
- -
- -
WARRANTY ITEM:
LSEVIER
12/20/2011
LSEVIER
B
004-6970
SN LABEL - AD6
MATERIAL.
COLOR.
DIE LINE
BLACK
Labels must be created from an agency approved tamper proof labeling system
such as "UL Recognized component marking and labeling system (example: UL PGGU2) or equivalent.
Label and adhesive must be rated for surface it is applied to (painted metal or ABS plastic),
Label and adhesive must be rated for 60 degrees C minimum. Labels must meet UL 1647 Permanence of Marking Test.
NOTE:
0000 - SEQUENCIAL SUPPLIER TRACKING NUMBER
REFERANCE 003-9706 FOR ADDITIONAL PLACEMENT GUIDELINES
SERIAL NO. FORMAT
AAAAAAA - SKU (NOT TO EXCEED 12 DIGITS)
BBB - NLS VENDOR CODE (3 DIGITS)
PPPPP - PURCHASE ORDER NUMBER (NOT TO EXCEED 8 DIGITS)
LL- PURCHASE LINE NUMBER (2 DIGITS)
CCCCCC - UNIQUE IDENTIFIER (5 DIGITS)
MANUFACTURE DATE:
MM/YY - MONTH AND YEAR THE UNIT WAS PRODUCED.
LSEVIER
DRAFTER
40mm
40mm
This document is the property of Nautilus, Inc. It may not be reproduced in whole or part, provided to third parties, or used for any purposes other than the performance of work for Nautilus, Inc. without written authorization. © Nautilus, Inc. This document is provided in confidence and your acceptance of this document is your agreement to maintain the document in confidence.
A
RELEASE
13410
LSEVIER
12/20/2011
B
ADDED ADDITIONAL INFORMATION FOR COMPLIANCE
?????
LSEVIER
4/2/2012
18225 NE Riverside Parkway, Portland, Or. 97230
www.nautilus.com
Phone:1-800-NAUTILUS
Model: Schwinn®Airdyne®AD6
Rating: NA
Class: SA, HA,
Maximum User Weight: 300lb (136kg)
Fitness Equipment
Made in: China
004-6970_B
0000
Serial Number
AAAAAABBBPPPPPPLLCCCCCC
MM/YY
Mfg. Date
ISO
20957
REVISIONS
ECO
REVISION
REV DESCRIPTION
APPROVED
DATE
TITLE.
PART NO.
REV.
SHEET 1 OF 1
SCALE: 1:1
DO NOT SCALE DRAWING
1. ALL ITEMS MUST BE RoHS COMPLIANT
2. ALL DIMENSIONS APPLY BEFORE PLATING OR COATING.
3. REMOVE ALL BURRS, BREAK SHARP EDGES 0.5 MM MAX.
4. ALL MACHINES SURFACES Ra 3.2 uM.
5. ALL APPLICABLE NAUTILUS STANDARDS AND
SPECIFICATIONS APPLY.
6. ALL DIMENSIONS ARE IN MILLIMETERS
7. ALL DUAL DIMENSIONS ARE IN INCH
UNLESS OTHERWISE SPECIFIED:
METRIC
THIRD ANGLE
PROJECTION
INTERPRET DIMENSIONS AND TOLERANCES
PER ASME Y14.5M - 1994
2.5
1.5
0.75
0.25
1°
X.
X.X
X.XX
X.XXX
ANGULAR
C
SIZE
This document is the property of Nautilus, Inc. It may not be reproduced in whole or part, provided to third parties, or used for any purposes other than the performance of work for Nautilus, Inc. without written authorization. All rights are reserved, including copyrights.
TOLERANCES.
DRAWN
DESIGNED
DATE
METRIC_C_REV G
NAUTILUS, INC.
16400 SE NAUTILUS DRIVE, VANCOUVER, WA 98683
LIFECYCLE
- -
APPROVALS
- -
- -
- -
WARRANTY ITEM:
L.SEVIER
1/30/2012
L.SEVIER
C
8000072
GWl AD6 HOME USE 300lbs
MATERIAL.
COLOR.
DIE LINE
PMS 152
PMS 109
BLACK
WHITE
Labels must be created from an agency approved tamper proof labeling system
such as "UL Recognized component marking and labeling system (example: UL PGGU2) or equivalent.
Label and adhesive must be rated for surface it is applied to (painted metal or ABS plastic),
Label and adhesive must be rated for 60 degrees C minimum. Labels must meet UL 1647 Permanence of Marking Test.
50mm
100.9mm
NPI 13410
A
RELEASE
1/30/2012
LSEVIER
xxxxxxx
B
ADDED WARNING
5/6/2012
LSEVIER
xxxxxxx
C
REMOVED COMMERCIAL WARNINGS
7/19/2012
LSEVIER
• Gardez les enfants et les animaux de compagnie
éloignés de cette machine en tout temps
•
Déconseillé aux enfants âgés de
moins de 14 ans.
• Lisez et familiarisez-vous avec le Manuel du
propriétaire et avec tous les avertissements
avant d’utiliser cette machine.
• Soyez prudent lorsque vous utilisez cet
équipement pour ne pas vous infliger de graves
blessures.
• Cette machine supporte un poids maximal de
300lbs. (136kg).
• Remplacez toute étiquette d’avertissement
endommagée, illisible ou manquante.
• Cet appareil est à usage domestique.
• Lorsque l’appareil est utilisé à domicile,
verrouillez-le lorsqu'il n'est pas utilisé.
• Keep children away.
•
Not intended for use by anyone under
14 years of age.
• Prior to use, read and understand the
Owner’s Manual.
• Injury or death is possible if Caution is
not used while using this machine.
• The maximum user weight for this
machine is 300 lbs (136 kg).
• Replace any “Caution”, “Warning” or
“Danger” label that is illegible,
damaged, or removed.
• This machine is for home use only.
• Lock the machine when not in operation.
004-8874_C