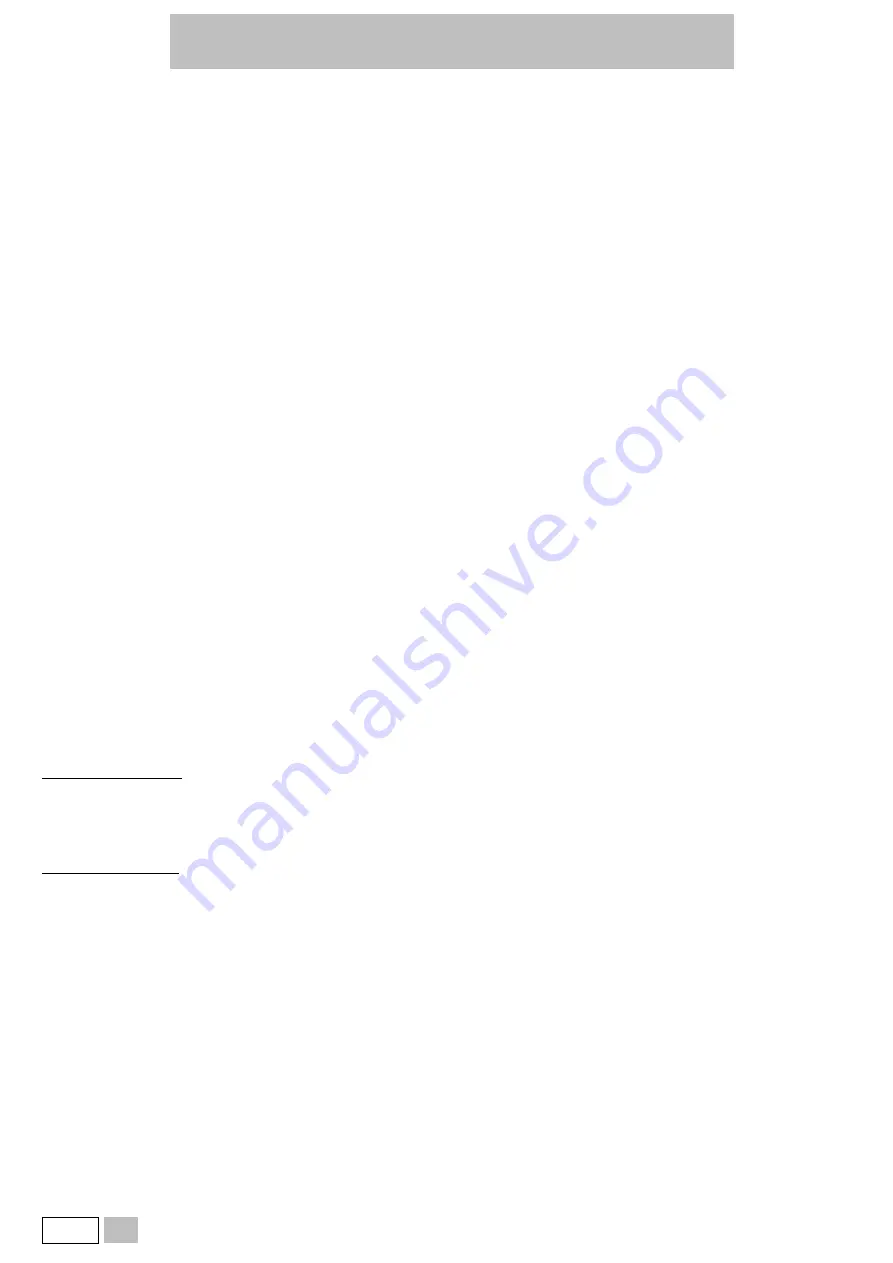
Bravo G4 17 / Bravo G4 22 / Bravo G4 28
6
EN
1.7. RESIDUAL RISKS
FOR THE USER
•
Contamination due to improper handling of the load;
•
Burn by contact with hot surfaces or fluids.
FOR THE PATIENT
•
Contamination due to unsterilised material caused by wrong cleaning treatment before sterilisation;
•
Contamination due to implementation of incorrect reprocessing procedures;
•
Contamination due to material unsuitable for sterilisation or not compliant with instructions for use;
•
Contamination due to unsterilised material caused by wrong final assessment of sterilisation process;
•
Contamination due to missing or wrong scheduled maintenance;
•
Contamination due to missing periodic validation.
1.8. INFORMATION ON MITIGATION OF RESIDUAL RISKS
FOR THE USER
Contamination due to improper handling of the load.
See chapter PREPARING THE MATERIAL.
Burn by contact with hot surfaces or fluids.
•
To extract the sterile material, once the sterilisation process has been completed with saturated steam at 121° or 134°, proceed as follows:
•
Always wear PPE suitable for the handling of hot material and gloves of appropriate material and thickness;
•
Clean your gloved hands with a germicide detergent;
•
Always use the special tray extractor, supplied as standard, to extract the trays from the sterilisation chamber;
•
Avoid any contact of trays and material with contaminated and/or non-heat-resistant surfaces;
•
Handle the sterile material making sure not to damage any packages, bags and containers serving as a barrier.
FOR THE PATIENT
Contamination due to unsterilised material caused by wrong cleaning treatment before sterilisation.
See chapter TREATING THE MATERIAL BEFORE STERILISATION.
Contamination due to implementation of incorrect reprocessing procedures.
Make sure to use sterile material.
Contamination due to material unsuitable to sterilisation or not compliant with instructions for use.
•
Check that the contaminated material is compatible with the selected sterilisation process;
•
Immediately separate the materials to be sterilised from those that must not be subjected to such process or are not able to withstand it.
Contamination due to unsterilised material caused by wrong final assessment of sterilisation process.
The sterilisation process electronic control system monitors the various phases, at the same time checking that the various parameters are respected; if
any type of anomaly is encountered during the cycle, the program is immediately interrupted, generating an alarm identified by a code, with a relative
message explaining the nature of the problem.
Furthermore, the sterilisation process can be checked by means of:
CHEMICAL INDICATORS
That monitor the sterilisation process by providing information, together with the control of physical and biological parameters, on the conditions occurred
in the sterilisation chamber during the process.
The final toning of the process indicator does not certify that the product is sterile but only that the device has been subjected to a sterilisation process. If
the toning does not occur, the operator in charge of releasing the sterile material, that must not be used, must put all actions to avoid the use of the treated
material.
PHYSICAL INDICATORS
They include the reading of machine data and the execution of specific tests indicated during the validation phase for that specific cycle/load/autoclave.
This control system can include:
•
Direct reading of the synoptic system (thermometer, pressure gauge, recorder, etc.);
•
Reading of prints/labels/files on which the data detected by the synoptic system are stored (parameters);
•
Execution of specific tests (Vacuum test, Bowie&Dick test, Helix test) according to local guidelines.
The operator in charge of the process certifies the validity of the load at the end of every cycle by means of the parametric release.
Contamination due to missing or wrong scheduled maintenance.
The steriliser, based on a preset programming, displays a warning message relating to the scheduled maintenance necessary to ensure the good operation
of the device.
Contamination due to missing periodic validation.
See chapter PERIODIC STERILISER VALIDATION.