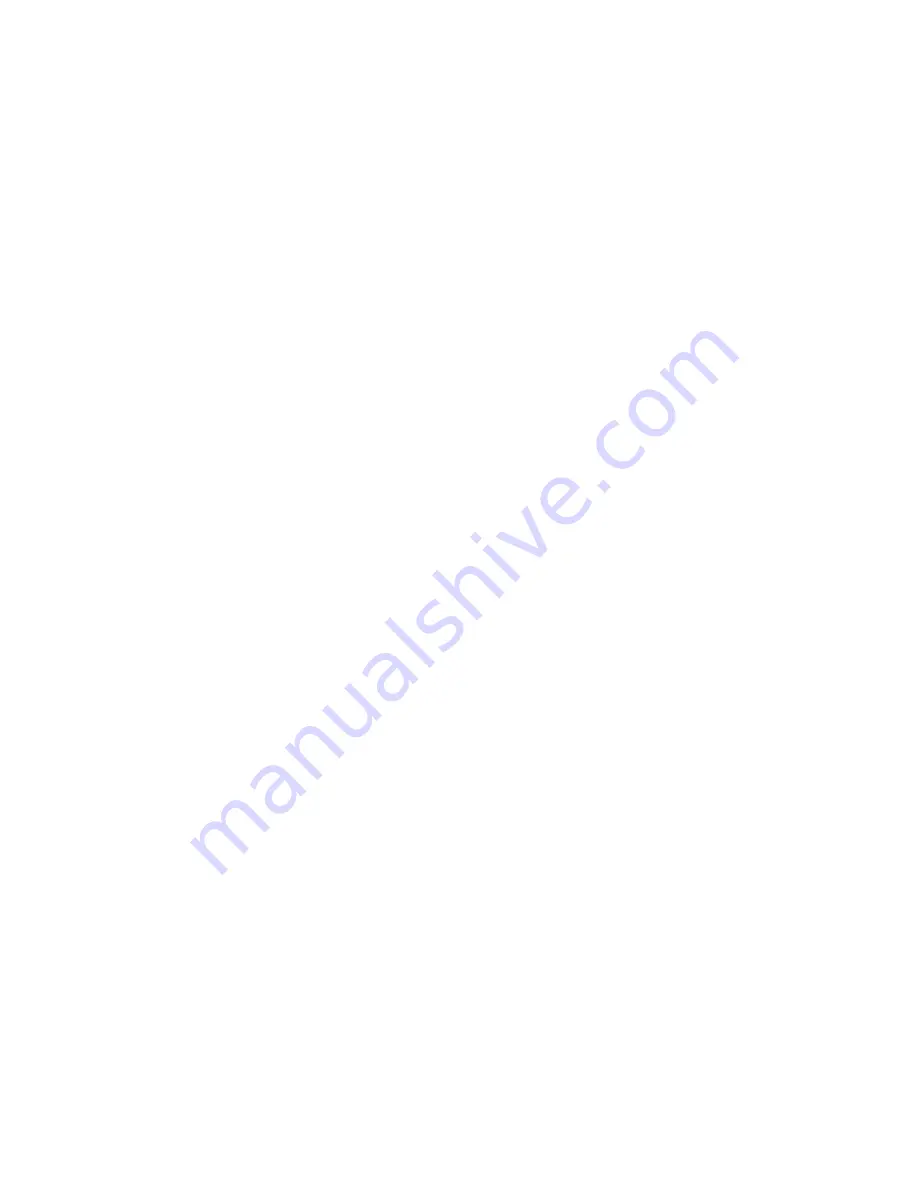
1
STATCLAVE G4 Service Manual
Diagram of key systems and components ........................................................................................................ 5
Front and back of the unit................................................................................................................................. 7
Top of the unit – inside reservoirs .................................................................................................................... 8
Specifications .................................................................................................................................................... 9
Safety devices .................................................................................................................................................... 9
Water supply ................................................................................................................................................... 10
Safety information .......................................................................................................................................... 10
Safe operation ................................................................................................................................................. 11
Safe servicing................................................................................................................................................... 11
Tools and hardware ........................................................................................................................................ 12
Shipping instructions ....................................................................................................................................... 13
Unboxing, connecting and lifting the unit into position ................................................................................. 15
Checking package contents ............................................................................................................................. 17
Positioning a unit ............................................................................................................................................ 18
Unit dimensions and operating environment ................................................................................................. 18
Electrical connections and power ................................................................................................................... 19
Connecting the exhaust tubes ........................................................................................................................ 19
Direct to drain connection (recommended) ............................................................................................... 20
Connecting to a waste bottle ...................................................................................................................... 21
Summary of Contents for STATCLAVE G4
Page 5: ...5 Diagram of key systems and components...
Page 6: ...6...
Page 17: ...17 Checking package contents...
Page 18: ...18 Positioning a unit Unit dimensions and operating environment...
Page 20: ...20 Direct to drain connection recommended...
Page 21: ...21 Connecting to a waste bottle...
Page 22: ...22 Connecting to the Internet Connecting to a wired network Connecting to a wireless network...
Page 23: ...23...
Page 25: ...25 Connecting an auxiliary pump...
Page 28: ...28...
Page 30: ...30 Starting and stopping a cycle...
Page 50: ...50 Registering for online access...
Page 51: ...51 First start up...
Page 52: ...52...
Page 58: ...58 Draining the unit for cleaning and shipping...
Page 61: ...61 Replacing the bacteriological filter Replacing the door seal...
Page 75: ...75...
Page 107: ...107 APPENDIX A STATCLAVE G4 plumbing diagram...
Page 108: ...108 APPENDIX B STATCLAVE G4 electrical schematic...