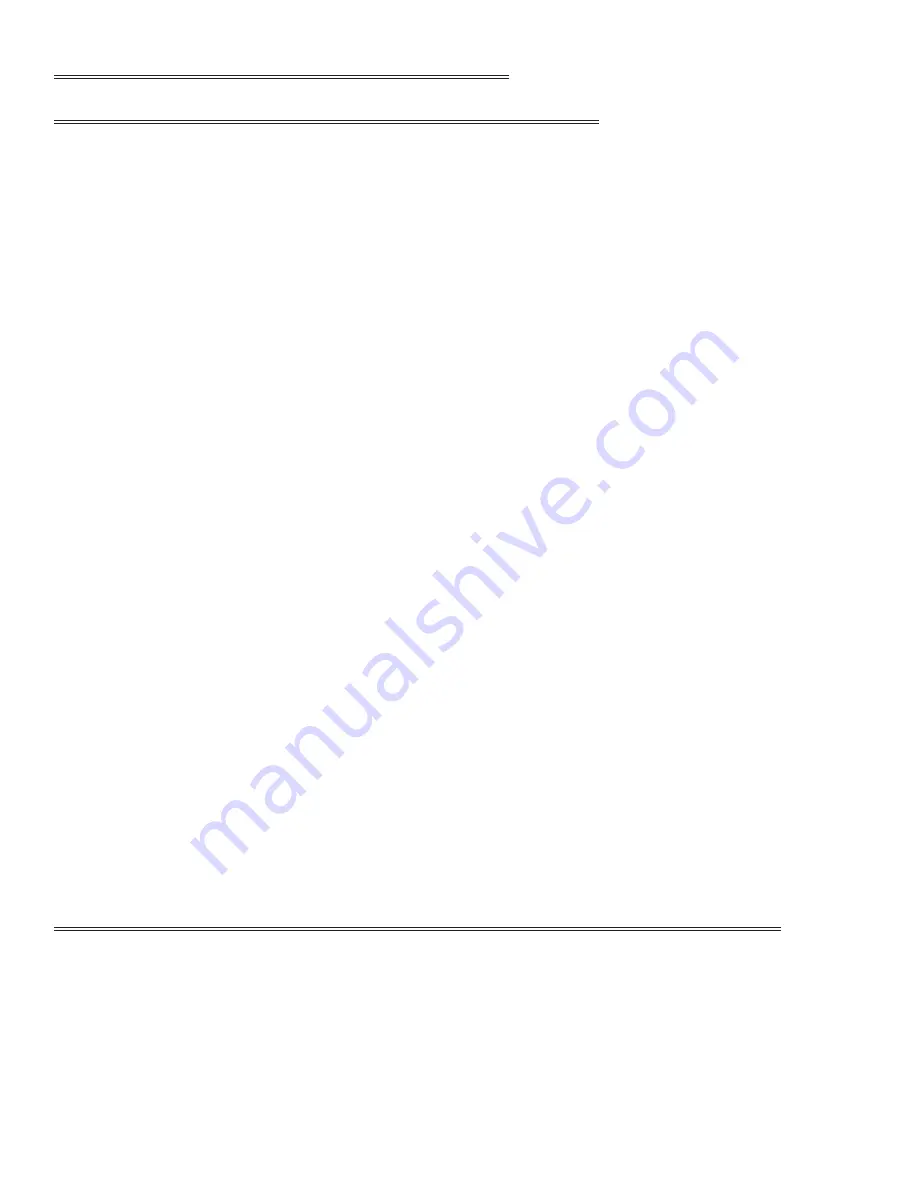
Page 46
10.0 TROUBLE SHOOTING GUIDE
10.1 ELECTRICAL TROUBLE SHOOTING
1.
THE MOTOR WILL NOT RUN.
A.
The main disconnect switch in the base cabinet must be on and the emergency stop switch must be
pulled out.
B.
The motor switch must be in the ON position to start the saw motor.
C.
The MANUAL/AUTO switch must be in the MANUAL position to start the machine.
D.
Also, check the supply voltage to the saw to make sure that it is the same as the motor voltage. If
the supply voltage is correct and the switch energizes and the motor still will not run, contact your
dealer or the factory.
E.
The saw hood must be closed to start the motor.
2.
THE SAW MOTOR RUNS BUT DOES NOT HAVE ADEQUATE POWER.
A.
Make sure that the supply voltage and phase correspond to the saw motor’s voltage and phase.
B.
Disconnect the machine from the power source and check for any loose or disconnected wires.
C.
The supply lines to the machine must be of adequate size to handle the load.
FOR RECOMMENDED SIZES AND LENGTHS, SEE SECTION 4.3.
D.
The worm gears in the head may be damaged. With the power to the machine disconnected,
check the blade spindle for any free travel. If free play is present, drain the oil from the head and
remove the motor. Check both worm gears for wear and replace, if necessary. We recommend
replacing the worm gears as a set, if either shows wear.
FOR REPLACEMENT INSTRUCTIONS, SEE SECTION 8.4.
3.
THE MACHINE WILL NOT RUN IN THE AUTOMATIC MODE.
A.
The counter must have a pre-set quantity displayed. If the counter reads zero, the machine will
not run in the automatic mode.
B.
There must be material in the shuttle vise and the vise must be adjusted to the material.
C.
If the machine has reached the end of a bar, you need to reset the machine before starting the
automatic operation again. REFER TO SECTION 7.0.
10.2 BREAKAGE OR EXCESSIVE DULLING OF BLADES
1.
Select the proper blade and spindle speed for the material being cut.
FOR RECOMMENDATIONS, REFER TO SECTION 6.1.
2.
Always break in the blade before you start normal cutting.
3.
Do not apply excessive down pressure on the workpiece. Excessive down pressure will cause the
teeth to remove too large of a chip, resulting in premature dulling or breakage.
4.
Use a good quality, synthetic coolant and maintain the proper ratio of coolant to water, as
recommended in SECTION 4.4.
Summary of Contents for CPO-315-HFA-5HP
Page 8: ...Page 7 FIGURE 1...
Page 10: ...Page 9 FIGURE 2...
Page 18: ...Page 17 THIS PAGE LEFT BLANK INTENTIONALLY...
Page 19: ...Page 18 6 2 BLADE INSTALLATION SEE FIGURE 4 BELOW FIGURE 4...
Page 23: ...Page 22 6 4 MATERIAL MAIN VISE SEE FIGURE 6 BELOW FIGURE 6...
Page 25: ...Page 24 FIGURE 7...
Page 27: ...Page 26 6 6 POWER DOWN FEED REFER TO FIGURE 8 BELOW FIGURE 8...
Page 30: ...Page 29 FIGURE 9...
Page 31: ...Page 30 6 9 COUNTER SET UP REFER TO FIGURE 10 BELOW FIGURE 10...
Page 37: ...Page 36 8 4 GEAR REPLACEMENT SAW HEAD REFER TO FIGURE 13 BELOW FIGURE 13...
Page 39: ...Page 38 8 5 SPINDLE REPLACEMENT MAIN VISE SEE FIGURE 14 BELOW FIGURE 14...
Page 41: ...Page 40 8 7 SHUTTLE VISE MAINTENANCE SEE FIGURE 15 BELOW FIGURE 15...
Page 46: ...Page 45 FIGURE 17...
Page 58: ......
Page 62: ...Page 61 FIGURE 24...
Page 64: ...Page 63 FIGURE 25...
Page 66: ...Page 65 FIGURE 26...
Page 68: ...Page 67 FIGURE 27...
Page 70: ...Page 69 FIGURE 28...
Page 72: ...Page 71 FIGURE 29...
Page 74: ...Page 73 FIGURE 30...
Page 76: ...Page 75 045345 Scotchman Inds PART NO FIGURE 31 A B D E F G C H I...
Page 77: ......
Page 78: ...Page 77 FIGURE 31B...
Page 80: ...Page 79 FIGURE 32...
Page 82: ...Page 81 FIGURE 33...
Page 83: ......
Page 84: ...Page 83 FIGURE 34...
Page 86: ...Page 85 FIGURE 35...
Page 88: ...Page 87 FIGURE 36...
Page 90: ...Page 89 FIGURE 36...
Page 92: ...Page 91 FIGURE 38...
Page 94: ...Page 93 045345 Scotchman Inds PART NO 14 0 WIRING DIAGRAMS...
Page 95: ...045345 Scotchman Inds PART NO 1 3 Page 94...
Page 97: ...Cont Prev Page Cont Prev Page 045345 Scotchman Inds PART NO 3 3 Page 96...