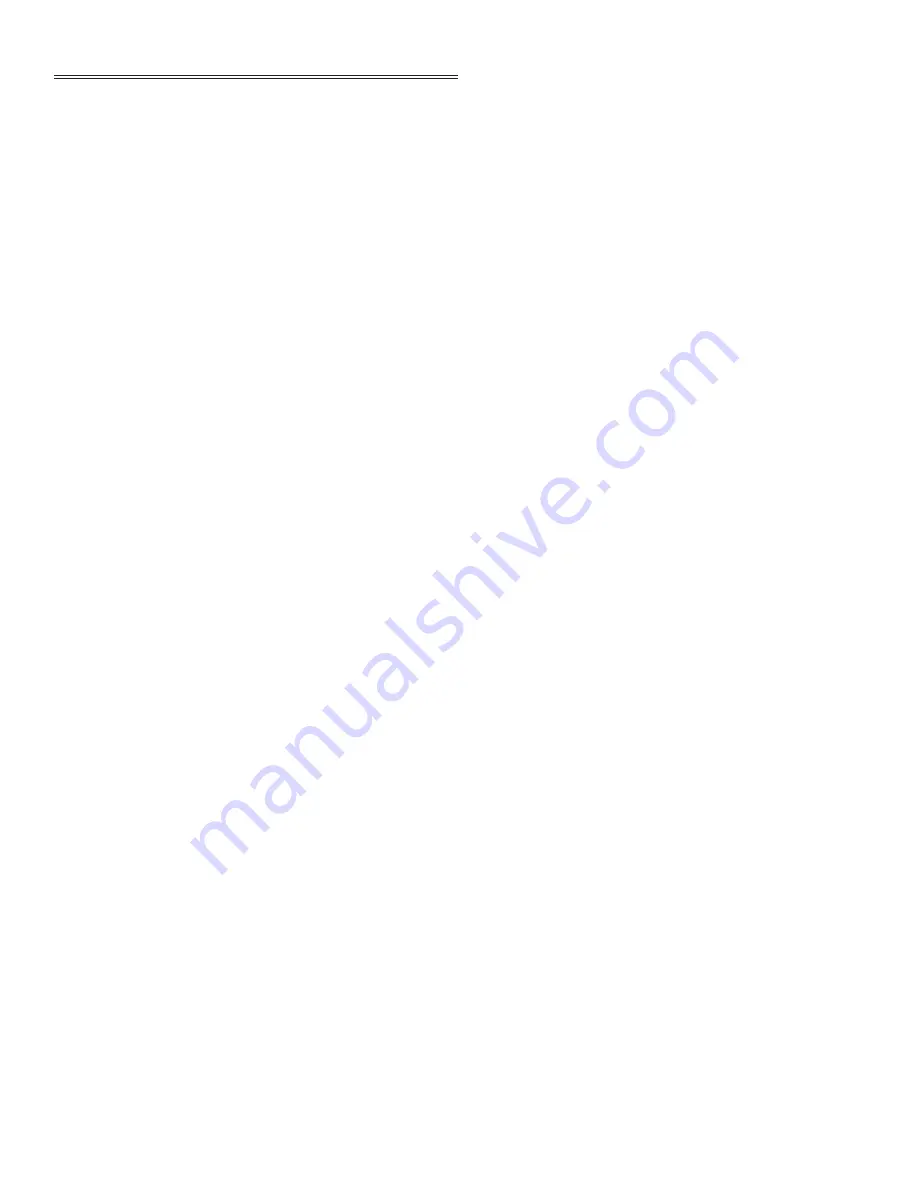
Page 8
4.2 MACHINE INSTALLATION
SEE FIGURE 2 ON THE FOLLOWING PAGE.
This machine is shipped on a pallet and can be moved to the installation location by means of a fork lift.
CAUTION: THIS MACHINE IS TOP HEAVY AND MUST BE MOVED WITH CARE, ON
HARD FLAT SURFACES ONLY.
USE THE FOLLOWING STEPS TO INSTALL THE MACHINE:
1.
Select a location for the machine that allows adequate room for any length of material you may
want to cut. Leave adequate space behind the machine and on either end for set-up and
maintenance.
2.
Lift the machine off of the shipping pallet, using a fork lift.
3.
Place the machine in its final location and level it, using the leveling pads. For this machine to
function properly, it is very important that it is level. Any supply tracks used with this machine
must also be level and aligned with the vises on the machine.
4.
Install the shuttle cylinder on the machine.
5.
We strongly recommend that the machine and any tracks be anchored to the floor. The shipping
brackets that hold the machine to the pallet can be used to anchor the machine to the floor.
6.
Connect the main air and electrical supply lines to the machine. To connect the air, slide the
shuttle valve (I) down to the closed position and connect the incoming supply line. (DO NOT
TURN THE AIR ON YET.) This machine requires a minimum of 90 PSI and may require up to
130 PSI, depending on your application. The electrical supply lines must be connected by a
qualified electrician. The supply lines connect to the top of the main disconnect switch (J) located
in the lower base cabinet. Before connecting the electrical supply, make sure that your plant phase
and voltage correspond to the phase and voltage of the machine.
CAUTION: DO NOT POWER THE MACHINE UNTIL THE MACHINE INSTALLATION IS
COMPLETE AND YOU HAVE READ ALL OF THE SECTIONS OF THIS MANUAL!
Summary of Contents for CPO-315-HFA-NF
Page 8: ...Page 7 FIGURE 1...
Page 10: ...Page 9 FIGURE 2...
Page 14: ...Page 13 FIGURE 3...
Page 18: ...Page 17 THIS PAGE LEFT BLANK INTENTIONALLY...
Page 22: ...Page 21 THIS PAGE LEFT BLANK INTENTIONALLY...
Page 23: ...Page 22 6 3 MATERIAL MAIN VISE SEE FIGURE 6 BELOW FIGURE 6...
Page 25: ...Page 24 FIGURE 7...
Page 27: ...Page 26 6 6 POWER DOWN FEED REFER TO FIGURE 8 BELOW FIGURE 8...
Page 30: ...Page 29 FIGURE 9...
Page 31: ...Page 30 6 9 COUNTER SET UP REFER TO FIGURE 10 BELOW FIGURE 10...
Page 33: ...Page 32 7 0 MACHINE AUTOMATIC OPERATION SET UP REFER TO FIGURE 11 BELOW FIGURE 11...
Page 37: ...Page 36 8 4 SPINDLE SHAFT REPLACEMENT REFER TO FIGURE 13 BELOW FIGURE 13...
Page 39: ...Page 38 8 5 SPINDLE REPLACEMENT MAIN VISE SEE FIGURE 14 BELOW FIGURE 14...
Page 41: ...Page 40 8 7 SHUTTLE VISE MAINTENANCE SEE FIGURE 15 BELOW FIGURE 15...
Page 44: ...Page 43 FIGURE 16...
Page 50: ...Page 49 FIGURE 18...
Page 56: ......
Page 60: ...Page 59 FIGURE 23...
Page 62: ...Page 61 FIGURE 24...
Page 64: ...Page 63 FIGURE 25...
Page 66: ...Page 65 FIGURE 26...
Page 68: ...Page 67 FIGURE 27...
Page 70: ...Page 69 FIGURE 28...
Page 72: ...Page 71 FIGURE 29...
Page 75: ......
Page 76: ......
Page 78: ...Page 77 FIGURE 31...
Page 80: ...Page 79 FIGURE 32...
Page 82: ...Page 81 FIGURE 33...
Page 84: ...Page 83 FIGURE 34...
Page 86: ...Page 85 FIGURE 35...
Page 88: ...Page 87 FIGURE 36...
Page 90: ...Page 89 FIGURE 37...
Page 92: ...14 0 WIRING DIAGRAMS Page 91 045345 Scotchman Inds PART NO...
Page 93: ...3 5PB 1PL 045345 Scotchman Inds PART NO 1 3 Page 92 Ser s B1392HFANF0314 Up Part of Next Page...