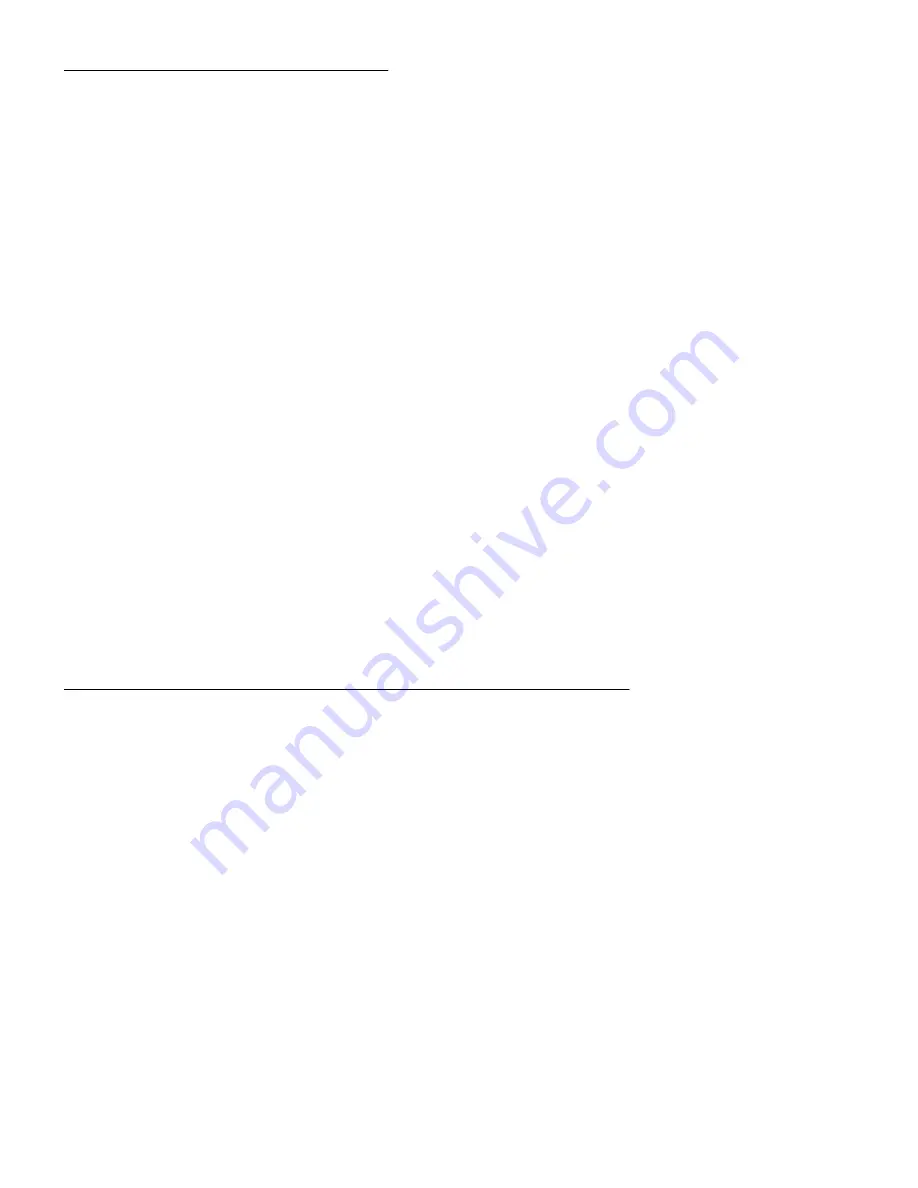
Page 110
12.4 VISE REGULATOR
ITEM
PART #
DESCRIPTION
A
078190
Regulator
A1
077538
Gauge
B
677934
Wall Mount
C
077864
M-5 x 12 SHCS
D
077742
1/4 Male Swivel x 169PL
E
077744
1/4 x 5/16 NPT Fitting
F
060501
5/16 Black Hose
047250
Complete Regulator Assembly
12.4A POWER DOWN FEED REGULATOR
A
078190
Regulator
B
677934
Mount
C
077864
M-5 x 12 SHCS
D
077746
1/4 x 90 Swivel
E
077746
1/4 x 90 Swivel
F
073758
Air Line
G
Summary of Contents for CPO-315-RFA-NF
Page 10: ...Page 9 FIGURE 1 A D E B C G I L F K ...
Page 12: ...Page 11 FIGURE 2 ...
Page 37: ...Page 36 6 4 POWER DOWN FEED REFER TO FIGURE 26 BELOW FIGURE 26 ...
Page 40: ...F G A B C FIGURE 27 NOTE HOOD AND BLADE GUARD ARE NOT SHOWN FOR CLARITY Page 39 ...
Page 47: ...Page 46 8 4 SPINDLE BEARING REPLACEMENT REFER TO FIGURE 31 BELOW FIGURE 31 ...
Page 49: ...Page 48 8 5 SPINDLE REPLACEMENT MAIN VISE SEE FIGURE 32 BELOW FIGURE 32 ...
Page 57: ...Page 56 WWW SCOTCHMAN COM BEST IN THE BUSINESS WARRANTY S C O T C H M A N ...
Page 66: ...Page 65 FIGURE 38 ...
Page 68: ...Page 67 FIGURE 39 ...
Page 70: ...Page 69 FIGURE 40 ...
Page 72: ...Page 71 FIGURE 41 ...
Page 76: ...Page 75 FIGURE 43 ...
Page 78: ...Page 77 FIGURE 44 ...
Page 82: ...Page 81 FIGURE 46 ...
Page 84: ...Page 83 FIGURE 47 ...
Page 86: ...Page 85 FIGURE 48 ...
Page 88: ...Page 87 FIGURE 49 ...
Page 90: ...Page 89 FIGURE 50 ...
Page 92: ...Page 91 FIGURE 51 ...
Page 94: ...Page 93 FIGURE 52 ...
Page 98: ...Page 97 THIS PAGE LEFT BLANK INTENTIONALLY ...
Page 100: ...Page 99 FIGURE 54 ...
Page 102: ...Page 101 FIGURE 55 ...
Page 104: ...Page 103 FIGURE 56 ...
Page 106: ...Page 105 FIGURE 57 ...
Page 110: ...Page 109 FIGURE 59 ...
Page 112: ...Page 111 FIGURE 60 ...
Page 114: ...Page 113 FIGURE 61 ...