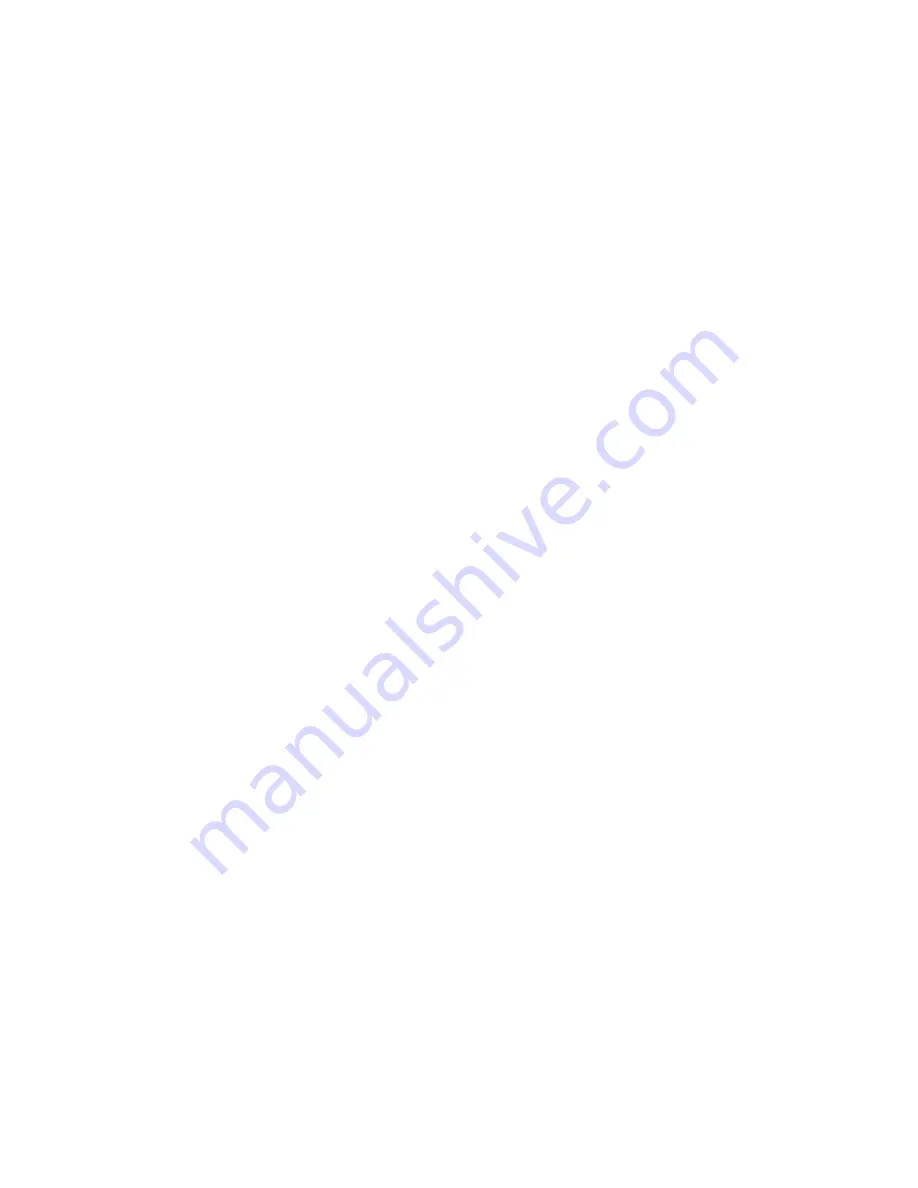
THE FOLLOWING ARE SET-UP AND MAINTENANCE INSTRUCTIONS FOR THE POWER VISE
OPTION (RETROFIT OR FACTORY INSTALLED):
1. Before connecting the air supply to the saw, make sure that the filter/lubricating device (A) is full of
oil.
2. Slide the shuttle valve (F) on the filter/lubricator device to the closed position.
3. Connect the air supply to the shuttle valve. Make sure that the vise is clear and that the head is in the
UP position.
4. Slide the shuttle valve in to open the valve. Whenever the shuttle valve is closed, it bleeds the air
pressure out of the system automatically.
5. Adjust the air pressure regulator (G). 90 PSI (6.2 BAR) is the minimum operating pressure. 105 PSI
(7.2 BAR) is the maximum.
6. Before powering the saw, pull the head down several times, to make sure that the four way valve (H)
and the lubricating device (A) are adjusted properly and that the air pressure setting remains con-
stant.
7. The four way valve should activate the vise at the beginning of the downstroke and release it at the
top of the return stroke. The four way valve is adjusted with the set screw (B) in the valve arm, just
above the roller.
8. The lubricating device (A) should release one drop of oil every 5 to 10 cycles. On top of the lubricating
device is a clear plastic dome with a small copper tube inside. The oil should drop out of the copper
tube. The lubricating device is adjusted by turning the knob (C) on the top of the lubricator.
9. To add oil to the lubricating device, disconnect the air supply and remove the plastic bowl. The bowl
is threaded and unscrews from the body. Fill the bowl approximately 3/4 full of oil designed for air
lubricators and screw it back on the lubricator.
TO ADJUST THE VISE TO THE SIZE OF MATERIAL BEING CUT:
1. Release the locking collar (D) on the vise spindle. The vise spindle is left hand threaded and the
locking collar must be turned clockwise to release it.
2. Open the vise, using the positioning handle (E), and place the material in the vise.
3. Crank the vise closed to within approximately 1/8 of an inch (3mm) from the material and re-lock the
locking collar (D). Failure to lock the locking collar may allow the vise to vibrate open while cutting,
causing damage or breakage of the blade. The power vise has approximately 1/4 of an inch (6mm) of
stroke. As with the manual vise, proper clamping is very important and special jaws may be required
for some materials.
FOR EXAMPLES, REFER TO FIGURE 8 ON PAGE 29.
PAGE 31
Summary of Contents for CPO 350
Page 1: ...CPO 350 VARIABLE SPEED COLD SAW PRINTED SEPTEMBER 2014...
Page 7: ...PAGE 7 FIGURE 1...
Page 8: ...4 2 MACHINE MOVING PROCEDURES SEE FIGURE 2 BELOW PAGE 8 FIGURE 2...
Page 11: ...PAGE 11 350 VS POWER DOWN 230 VOLT SEE PAGE 47 FOR POWER DOWN WIRING FIGURE 3 1...
Page 12: ...PAGE 12 350 VS MANUAL PK 230 VOLT FIGURE 3 2...
Page 13: ...PAGE 13 350 VS POWER DOWN 460 VOLT SEE PAGE 47 FOR POWER DOWN WIRING FIGURE 3 3...
Page 14: ...PAGE 14 350 VS MANUAL PK 460 VOLT FIGURE 3 4...
Page 17: ...PAGE 17 FIGURE 4...
Page 19: ...PAGE 19 FIGURE 5...
Page 27: ...PAGE 27 FIGURE 8 FIGURE 9...
Page 29: ...PAGE 29 FIGURE 10...
Page 33: ...PAGE 33 FIGURE 12...
Page 35: ...PAGE 35 FIGURE 13...
Page 37: ...PAGE 37 FIGURE 14...
Page 39: ...PAGE 39 FIGURE 15...
Page 41: ...PAGE 41 FIGURE 16...
Page 43: ...PAGE 43 FIGURE 17...
Page 45: ...7 2F POWER DOWN FEED WIRING DIAGRAM Ser s 6425 Up PAGE 45 FIGURE 19...
Page 46: ...7 2G PNEUMATIC SCHEMATIC POWER DOWN MACHINES PAGE 46 FIGURE 20...
Page 47: ...THIS PAGE LEFT BLANK INTENTIONALLY PAGE 47...
Page 49: ...PAGE 49 FIGURE 21...
Page 51: ...PAGE 51 FIGURE 22...
Page 55: ...PAGE 55 FIGURE 23...
Page 59: ...PAGE 59 FIGURE 25...
Page 61: ...PAGE 61 FIGURE 26...
Page 63: ...PAGE 63 FIGURE 27...
Page 65: ...PAGE 65 FIGURE 28...
Page 67: ...PAGE 67 FIGURE 29...
Page 69: ...PAGE 69 FIGURE 30...
Page 71: ...PAGE 71 FIGURE 31...
Page 73: ...PAGE 73 FIGURE 32...
Page 75: ...PAGE 75 FIGURE 33...
Page 77: ...PAGE 77 FIGURE 33...
Page 79: ...PAGE 79 FIGURE 34...
Page 81: ...PAGE 81 FIGURE 35...
Page 83: ...PAGE 83 FIGURE 36...
Page 85: ...PAGE 85 FIGURE 37...
Page 87: ...PAGE 87 FIGURE 38...
Page 89: ...PAGE 89 FIGURE 39...
Page 91: ...PAGE 91 FIGURE 40...
Page 93: ...PAGE 93 FIGURE 41...