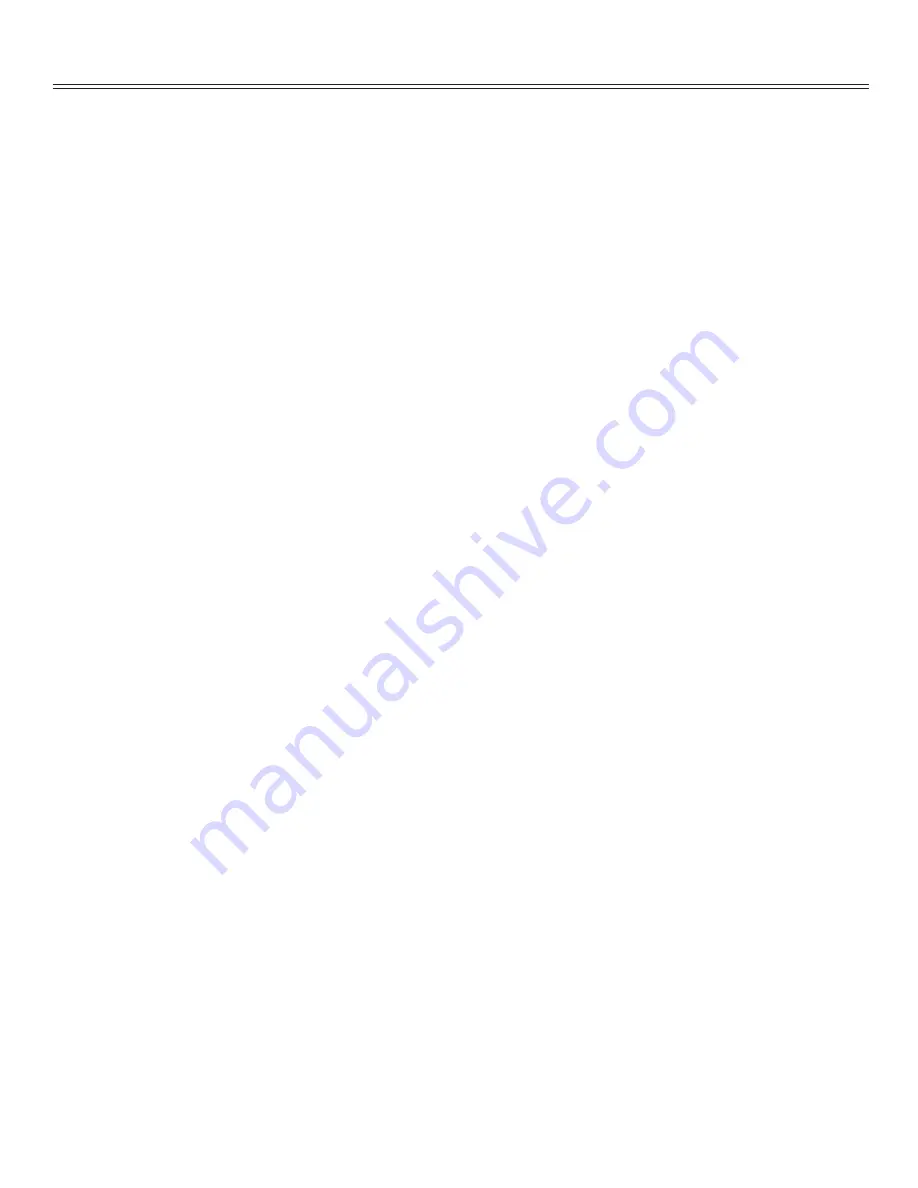
7.2D INSTALLING BLADES (POWER DOWN FEED)
SEE FIGURE 17 ON THE FOLLOWING PAGE.
Ö
CAUTION: USE ONLY HIGH SPEED STEEL BLADES DESIGNED FOR THIS MACHINE. DO
NOT MODIFY ANY BLADE TO FIT THIS MACHINE. DO NOT USE BLADES DESIGNED FOR
THIS MACHINE ON ANY OTHER EQUIPMENT.
The CPO-350 saw is designed to use a maximum 14 inch (350mm) diameter blade. The arbor size is
40mm with four 12mm pins spaced at 64mm.
Ü
BEFORE INSTALLING THE BLADE, make sure that the power to the machine is disconnected.
USE THE FOLLOWING STEPS TO INSTALL A BLADE:
(An 8mm hex key wrench (A), shipped with each machine, is required to change blades.)
1. Release the upper stroke control and allow the head to travel to its full UP position.
2. Raise the movable section of the guard (B) to the OPEN position.
3. Remove the blade bolt (C) through the center hole in the blade guard.
4. Remove the blade flange (D).
5. Install the blade. Make sure that the pin holes line up to the holes in the spindle.
6. Replace the blade flange and start the bolt into the spindle.
7. Before locking the blade in position, the back lash must be taken up. To take up the back lash,
rotate the bottom of the blade toward you until it seats against the drive pins.
Ö
CAUTION: THE BLADES ARE VERY SHARP AND CARE MUST BE TAKEN WHEN
REMOVING THE BACK LASH. DO NOT GRIP THE CUTTING EDGE OF THE BLADE BARE
HANDED. THE BACK LASH MUST BE TAKEN UP EVERY TIME A BLADE IS CHANGED.
8. After taking up the back lash, tighten the blade bolt (C).
9. Return the movable guard to the DOWN position and re-set the upper stroke control.
10. Break in the saw blade. The teeth on new or re-sharpened blades have a sharp edge and should be fed
through the first three or four cuts, very slowly, before starting normal cutting. Besides taking up the
back lash and breaking in the blade, it is very important to keep the blade flange, the spindle and the
blade clean and free from nicks. Failure to do these things will result in broken or damaged blades.
PAGE 42
Summary of Contents for CPO 350
Page 1: ...CPO 350 VARIABLE SPEED COLD SAW PRINTED SEPTEMBER 2014...
Page 7: ...PAGE 7 FIGURE 1...
Page 8: ...4 2 MACHINE MOVING PROCEDURES SEE FIGURE 2 BELOW PAGE 8 FIGURE 2...
Page 11: ...PAGE 11 350 VS POWER DOWN 230 VOLT SEE PAGE 47 FOR POWER DOWN WIRING FIGURE 3 1...
Page 12: ...PAGE 12 350 VS MANUAL PK 230 VOLT FIGURE 3 2...
Page 13: ...PAGE 13 350 VS POWER DOWN 460 VOLT SEE PAGE 47 FOR POWER DOWN WIRING FIGURE 3 3...
Page 14: ...PAGE 14 350 VS MANUAL PK 460 VOLT FIGURE 3 4...
Page 17: ...PAGE 17 FIGURE 4...
Page 19: ...PAGE 19 FIGURE 5...
Page 27: ...PAGE 27 FIGURE 8 FIGURE 9...
Page 29: ...PAGE 29 FIGURE 10...
Page 33: ...PAGE 33 FIGURE 12...
Page 35: ...PAGE 35 FIGURE 13...
Page 37: ...PAGE 37 FIGURE 14...
Page 39: ...PAGE 39 FIGURE 15...
Page 41: ...PAGE 41 FIGURE 16...
Page 43: ...PAGE 43 FIGURE 17...
Page 45: ...7 2F POWER DOWN FEED WIRING DIAGRAM Ser s 6425 Up PAGE 45 FIGURE 19...
Page 46: ...7 2G PNEUMATIC SCHEMATIC POWER DOWN MACHINES PAGE 46 FIGURE 20...
Page 47: ...THIS PAGE LEFT BLANK INTENTIONALLY PAGE 47...
Page 49: ...PAGE 49 FIGURE 21...
Page 51: ...PAGE 51 FIGURE 22...
Page 55: ...PAGE 55 FIGURE 23...
Page 59: ...PAGE 59 FIGURE 25...
Page 61: ...PAGE 61 FIGURE 26...
Page 63: ...PAGE 63 FIGURE 27...
Page 65: ...PAGE 65 FIGURE 28...
Page 67: ...PAGE 67 FIGURE 29...
Page 69: ...PAGE 69 FIGURE 30...
Page 71: ...PAGE 71 FIGURE 31...
Page 73: ...PAGE 73 FIGURE 32...
Page 75: ...PAGE 75 FIGURE 33...
Page 77: ...PAGE 77 FIGURE 33...
Page 79: ...PAGE 79 FIGURE 34...
Page 81: ...PAGE 81 FIGURE 35...
Page 83: ...PAGE 83 FIGURE 36...
Page 85: ...PAGE 85 FIGURE 37...
Page 87: ...PAGE 87 FIGURE 38...
Page 89: ...PAGE 89 FIGURE 39...
Page 91: ...PAGE 91 FIGURE 40...
Page 93: ...PAGE 93 FIGURE 41...