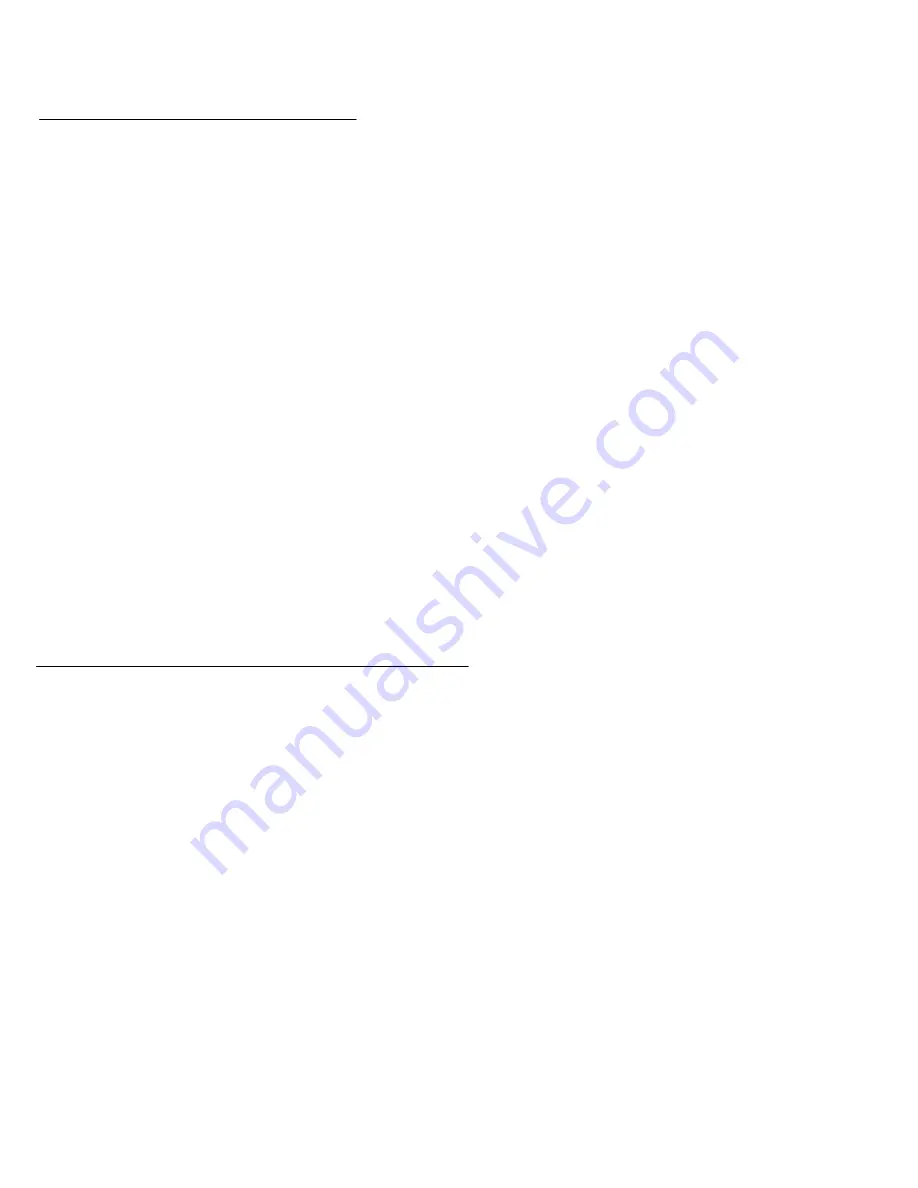
PAGE 6
1.0 INTRODUCTION
2.0 SAFETY PRECAUTIONS
1.
The operators of this machine must be qualified and well trained in the operation of the machine.
The operators must be aware of the capacities of the machine and the proper use of the hold down
device, strippers and guards provided with the machine. This manual is not intended to teach
untrained personnel how to operate machinery.
2.
All of the guards, adjustable restrictors and awareness barriers must be installed on the machine
and kept in good working order. Promptly replace worn or damaged parts with authorized parts.
3.
Never place any part of your body into or under any of the machine’s moving parts, strippers or
hold devices.
4.
Wear the appropriate personal protective equipment. Safety glasses are required at all times,
whether operating, setting up or observing this machine in operation. Since heavy pieces of metal
with sharp edges can be processed on this machine, the operator should also wear steel-toed shoes
and leather gloves.
5.
Strictly comply with all warning labels and decals on the machine. Never remove any of the labels
and replace worn or damaged labels promptly.
6.
Always disconnect and lock out the power when performing maintenance work or setting up any
tooling on the machine. Follow the procedures outlined in the operator’s manual for setting up,
changing or aligning any tooling on this machine.
7.
Never operate this machine with dull or damaged tooling. Replace worn punches, dies and blades
promptly.
PAGE 6
The Scotchman DO-150/240-24M is a versatile, multi-purpose, shearing, punching and forming machine
engineered for trouble-free operation. The design of the machine combines simplicity of operation with
smooth, full stroke control. The ability of the operators to control the machine’s direction of movement
at any point in the stroke (stop, jog or reverse) gives the Scotchman Ironworker a tremendous advantage
over mechanical Ironworkers. There is no chance of the Scotchman being "accidentally tripped".
The hydraulic system operates at a maximum pressure of 3,500 PSI (241 BAR) in the punch and tooling
station and 3,500 PSI (241 BAR) in the shear and notch position and is protected from overload by a
relief valve. The Scotchman DO-150/240-24M is designed as a dual operator Ironworker. On this model,
the punch and tooling stations operate independently of the shear and notcher stations.
This machine is designed for the user that wants the advantage of doubling production by having two
operators using the same machine at the same time. Scotchman also offers many optional tools that are
adaptable to this model. Some of the optional tools available are: a channel shear, pipe notcher, 12 & 24
inch brake attachments, a picket tool and a variety of special tools. If you have a special application,
please contact your dealer or the factory.