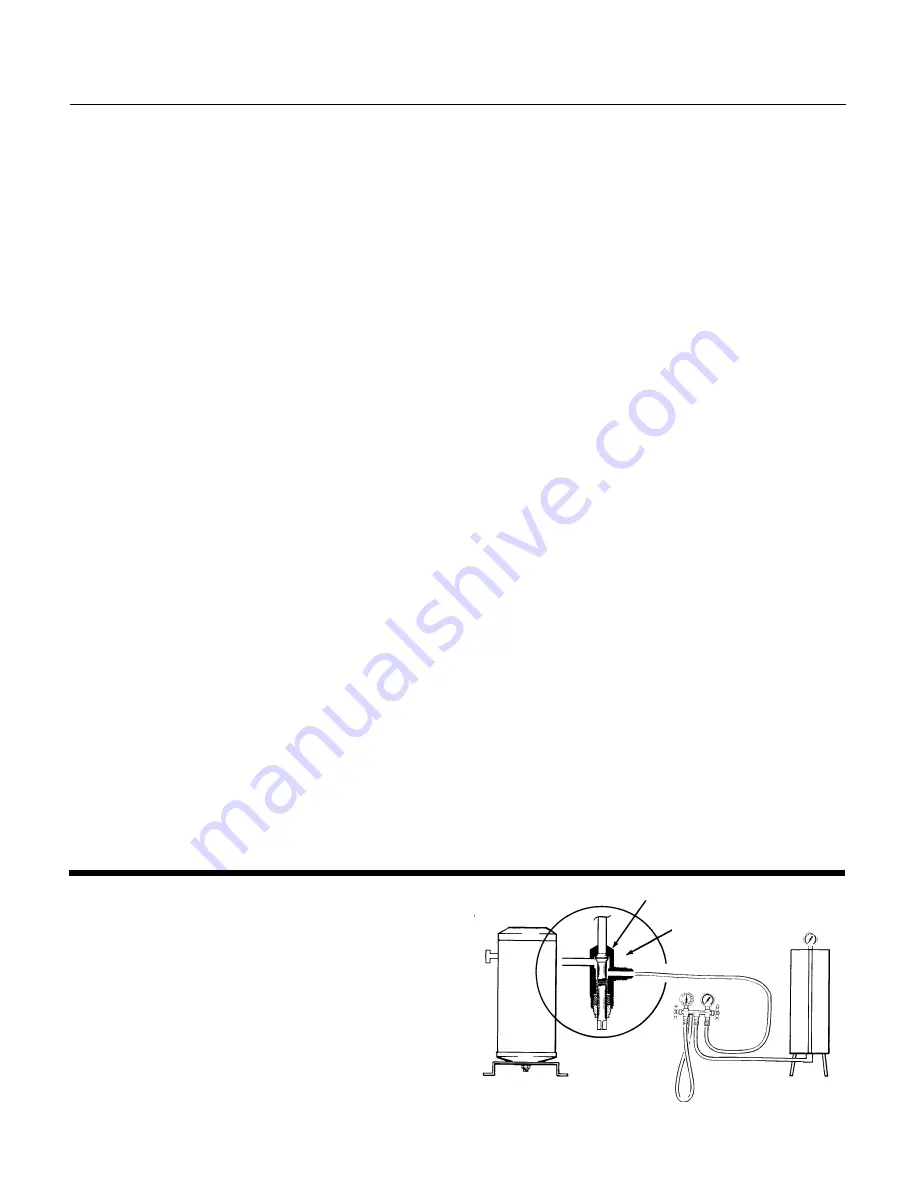
Thermostatic Expansion Valve
1. Before replacing this valve, be certain that the
valve is the cause of the problem, and cannot be
adjusted.
2. Remove the top, service and front panels.
3. Discharge and recover the refrigerant.
4. Locate the TXV bulb (on the suction line),
remove the clamps and bulb from the tube.
5. With the refrigeration system open, unsweat the
TXV from the tubing.
6. Place the new TXV in position.
7. Wrap the new TXV body with wet rags. Do not
get any moisture in the valve.
8. Carefully braze the valve to the tubing. Examine
the joints, if they look good proceed to the next
step, if not, re-do them.
9. Install a new dryer, and braze it in place also.
10. Reattach the TXV bulb to the suction line in the
same place as the old one.
11. Evacuate the system to 200 microns.
12. Weigh or measure the nameplate charge into
the receiver.
13. If the machine has been off on the breaker
there may be refrigerant trapped in the oil of the
compressor, so do not restart until the compressor
has been warmed by the crankcase heater for 12
hours. If the compressor was warm throughout the
replacement process, the ice machine may be
restarted without waiting to re-warm the
compressor.
Hot Gas or Liquid Line Valve.
1. Before replacing this valve, be certain that the
valve is the cause of the problem.
2. Remove the top, service and front panels.
3. Discharge and recover the refrigerant.
4. Unplug the coil of the valve.
5. With the refrigeration system open, unsweat the
valve from the tubing.
6. Place the new valve in position.
7. Wrap the new valve body with wet rags. Do not
get any moisture in the valve.
8. Carefully braze the valve to the tubing. Examine
the joints, if they look good proceed to the next
step, if not, re-do them.
9. Install a new dryer, and braze it in place also.
10. Plug the power cord back onto the coil.
11. Evacuate the system to 200 microns.
12. Weigh or measure the nameplate charge into
the receiver.
13. If the machine has been off on the breaker
there may be refrigerant trapped in the oil of the
compressor, so do not restart until the compressor
has been warmed by the crankcase heater for 12
hours. If the compressor was warm throughout the
replacement process, the ice machine may be
restarted without waiting to re-warm the
compressor.
FRONT SEATED VALVE
SERVICE PORT
Refrigerant:
NO liquid refrigerant may be put into this system
anywhere except the receiver. DO NOT use the
access valves at the front of the machine for
weighing in the charge: use the “king” or receiver
service valve. All liquid HP62 must be weighed
into the receiver through the “front seated”
receiver outlet service valve.
REMOVAL AND REPLACEMENT
CME500R
March 1994
Page 26