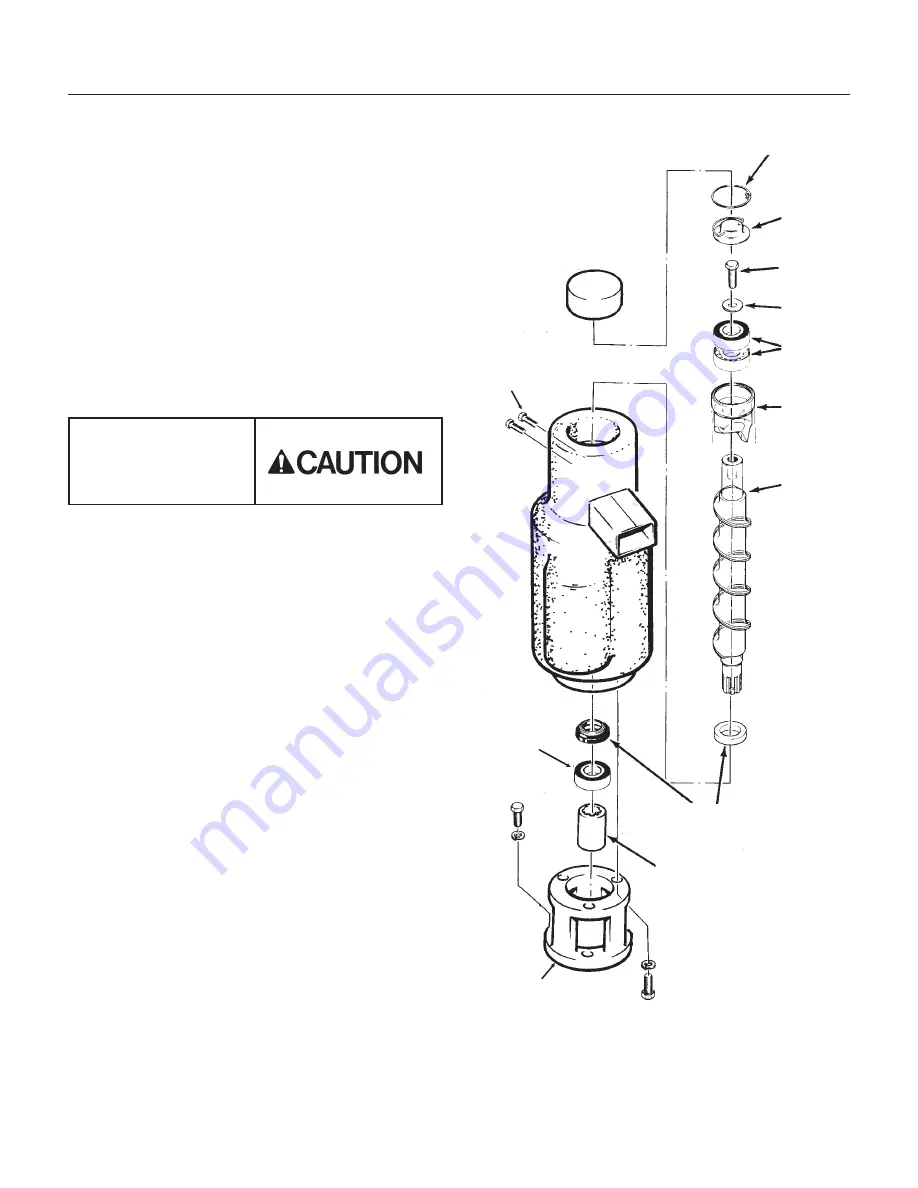
Auger and Bearing Inspection
While in most areas regular in-place cleaning with
Scotsman Ice Machine Cleaner will be adequate to
keep the interior of the evaporator free of
excessive mineral build up, some water conditions
may require more intense methods. In addition, the
auger bearings require physical inspection to
determine that they are not wearing. This physical
inspection is recommended twice per year for the
top bearing and once per year for the auger and
both bearings.
Whenever the auger is removed, replacement of
the water seal is recommended.
If a bearing requires replacement, the other
bearing must also be replaced.
1. Unplug or disconnect electrical power.
2. Shut off the water supply.
3. Remove top panel.
4. Remove right side panel.
5. Drain the evaporator and reservoir.
6. Remove foam cap on top of evaporator.
7. Remove 2 permagum plugs from the side of the
evaporator.
8. Remove 2 screws (screwheads were covered by
the permagum).
9. Pull up on the pull ring to remove the auger. If it
is difficult to pull:
A. Remove the breaker cover by taking the snap
ring out.
B. Unscrew the auger bolt.
C. Use threaded rod or a slide hammer puller and
screw into the auger, slide the weight quickly up
against the stop to remove the auger.
If the auger still will not move, bearing replacement
is mandatory. See Bearing Removal and
Replacement.
FDE474
March 2000
Page 17
Snap Ring
Cap
Cap Screw
Washer
Top Bearing
Set
Breaker
Auger
Water
Seal
Coupling
Adapter Stand
Auger & Bearings
Breaker
Screws
Bottom
Bearing
Rotating parts hazard.
Disconnect Electrical
Power Before
Beginning.