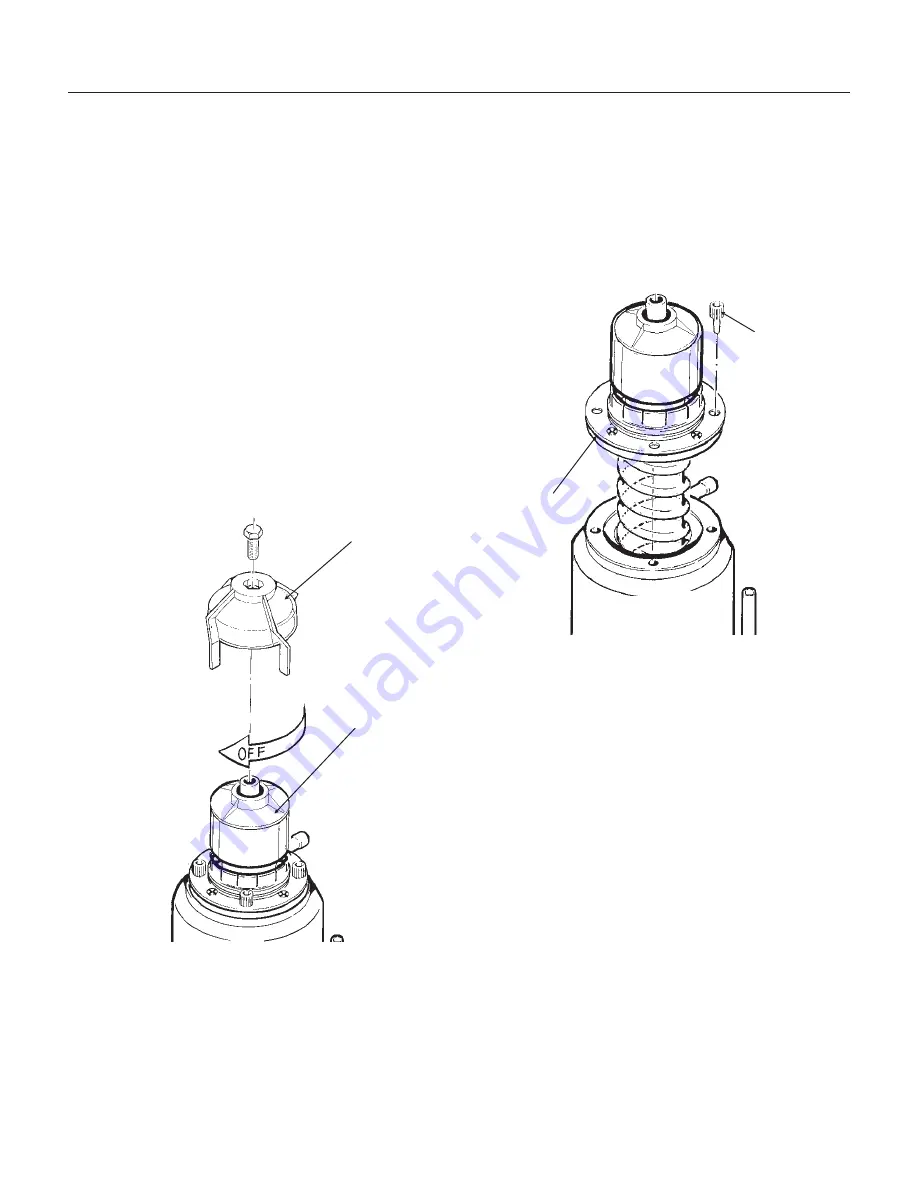
AUGER MAINTENANCE
In some areas the water supply to the Ice Machine
will have a great deal of minerals in it, and that will
result in an evaporator and auger becoming
coated with these minerals, requiring a more
frequent removal than twice per year. If in doubt
about the condition of the evaporator and auger,
the auger can be removed so the parts can be
inspected.
Note: Water filters can filter out suspended solids,
but not dissolved solids. “Soft” water may not be
the complete answer. Check with a water
treatment specialist regarding water treatment
For more information on removal and
replacement of these parts, see REMOVAL AND
REPLACEMENT.
Shut off water and electrical supply.
1. To remove the auger, remove the front and top
panels.
2. Push back bail clamp holding ice chute cover to
ice chute, and remove cover.
3. Unscrew and remove ice sweep.
4. Remove ice chute from evaporator.
5. Remove 4 allen screws holding breaker to
evaporator.
6. Pull up to remove auger.
After the auger has been removed, allow the auger
to dry; if the auger is not bright and shiny, it must
be cleaned.
Clean the auger and evaporator as required.
DO NOT HONE THE EVAPORATOR.
7. Replace the water seal.
8. Reverse to reassemble.
NME1854R & FME2404R
January 2000
Page 24
BREAKER &
BEARING &
AUGER
ASSEMBLY
ALLEN
SCREWS
ICE
SWEEP
BREAKER
COVER