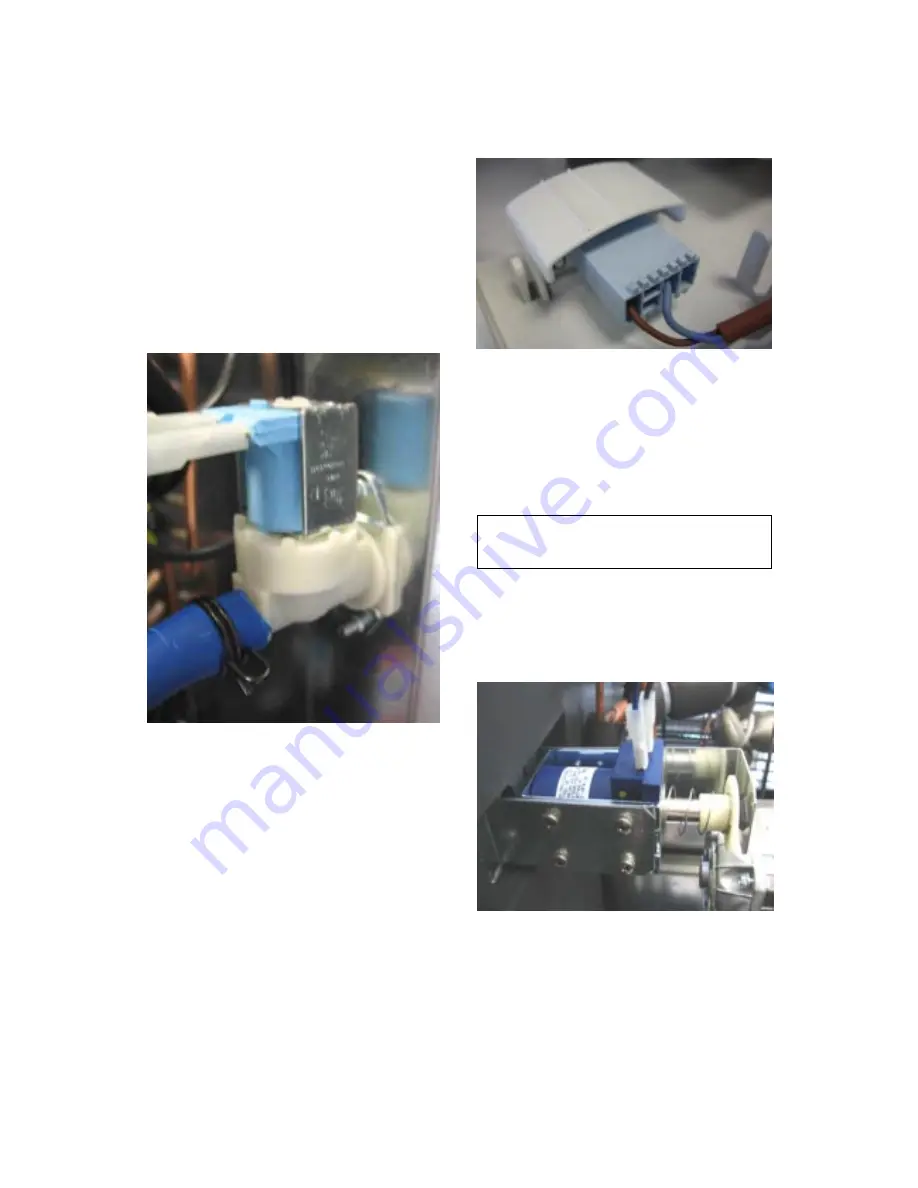
Page 29
Page 29
14. Water inlet solenoid valve - 3/4" male
fitting
The Water Inlet Solenoid valve is energised by
the P.C. Board during the beginning of the freezing
cycle till the water reaches the maximum level
into the sump (controlled by the Water Level
Sensor).
After 3 minutes, from the start up of the freezing
cycle, the Water Inlet Valve is energised again for
a short period to re-fill the sump with water till
again to the max. level so to minimise any
possibility of slush ice formation
A flow control, fitted into its outlet port, reduces
the pressure of the water flow.
15. Water level sensor
The Water Level Sensor, located on the front of
the water sump, works in conjunction with the
P.C. Board in order to control the water level at
beginning of the freezing cycle by receiving a low
power current passing through the water.
When the current reaches the PC Board, the
water inlet solenoid valve is de-energised.
In case the PC Board doesn’t receive any signal
(current) from the Water Level Sensor within the
first 3 minutes of the freezing cycle, the PC Board
trips OFF the operation of the machine with the
switching ON of the Water Error LEDs.
16. Start up delay PC Board (only for MV 1006)
Located in the back side of the unit it delays the
start up of the entire machine by 90' so to avoid
that compressor can start up w/out be pre-heated.
17. Start up delay PC Board by-pass switch
(only for MV 1006)
Located in the back side of the machine allows to
by-pass the delay time controlled by the delay
PC Board.
WARNING. It is IMPERATIVE to by-pass
the delay time only when sure of proper
warm up of compressor.
18. Harvest Assist Solenoid (Not used on
MV 306)
Operated by the controller in parallel with the hot
gas valve. Cycles on and off at the beginning of
a restart. Energized throughout the harvest cycle.
Line voltage coil.