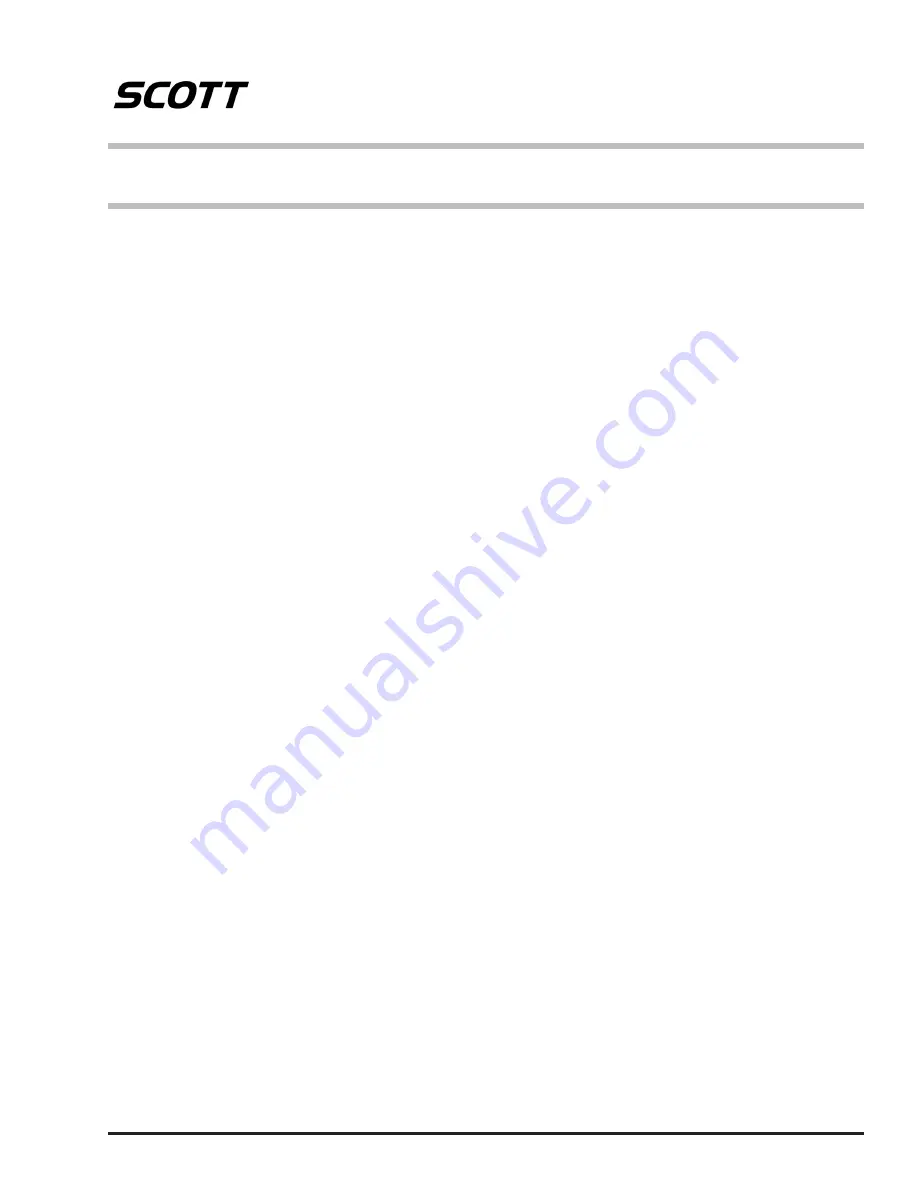
1
Stationary Air Compressor System Operating Instructions
Contents
Stationary Air Compressor Systems
Operating Instructions
SCOTT P/N 595134-01 REV C 1/12
IMPORTANT SAFETY INSTRUCTIONS
.................2
Safety Notations ..........................................3
Safety Labels ...............................................3
Limited Warranty
....................................................4
1 - Introduction .......................................................5
HUSH Air Compressor .................................7
Simple Air Compressor ................................7
2 - Features .............................................................7
General Description .....................................7
Routine Maintenance ...................................7
Simple Air System Components ..................8
HUSH Air System Components ...................9
Principle of Operation ................................10
Breathing Air Quality ..................................10
Simplified System Diagram
.......................11
3 - Starting and Operating the Stationary Air Com-
pressor System ..............................................15
Introduction
................................................15
Working with Compressed Air
...................15
Pre-Operation Checks ...............................16
Removing the Cabinet Enclosure .......16
Pre-Operation Check Procedures
.......20
Operation of the Compressor System .......20
Compressor Rotation .................................20
X4 Control Panel .......................................20
Operating the Compressor .......................22
Operating the Compressor ........................23
Operating the Compressor Continued...
....24
Compressor Stage Gauge Readings
.........24
Information Button .....................................25
Operating the Compressor ........................25
Service Notifications
..................................25
Operating the Compressor Continued...
....26
System Tolerances and Overrides
.............26
Use of the Purge ........................................26
Overrides
...................................................27
System Shutdown
......................................27
Charging the Storage System ...................28
Storage Cylinder Inspection
................28
Charging Storage Cylinders
................28
Cascade Volume Operation
................28
4 - Operator Maintenance Checks.......................29
Operator Maintenance Checks ..................29
Service Schedules
.....................................29
Condensate Container
...............................30
Electrical Fuses .........................................30
Simple Air Inlet Filter Cap ...................30
Inlet Filter ...................................................31
Purification System Moisture Indicator
......31
Compressor Drive Belt ..............................31
5 - Additional Features .........................................33
Auxiliary Air Outlets (Standard)
.................33
Regulated Pressure Outlet (Optional)
.......34
High Pressure Outlet and Gauge
........34
Low Pressure Outlet and Gauge
.........35
6 - System Administrator Responsibilities ........37
Modify System Settings
.............................37
Perform System Service ............................38
Calibrate the CO Monitor ...........................39
7 - Index .................................................................41
Maintenance Record ............................................43
© 2012 SCOTT Safety. SCOTT, the SCOTT SAFETY Logo, Scott Health and Safety, HUSH Air, Simple Air, X4, and
Smart Fill are registered and/or unregistered marks of Scott Technologies, Inc. or its affiliates.
Summary of Contents for HUSH
Page 2: ......
Page 21: ...3 Starting and Operating Stationary Air Compressor System Operating Instructions 19 NOTES ...
Page 34: ...Stationary Air Compressor System Operating Instructions 4 Operator Maintenance 32 NOTES ...
Page 38: ...Stationary Air Compressor System Operating Instructions 5 Additional Features 36 NOTES ...
Page 45: ...43 Maintenance Record ...
Page 46: ...44 NOTES ...
Page 47: ......