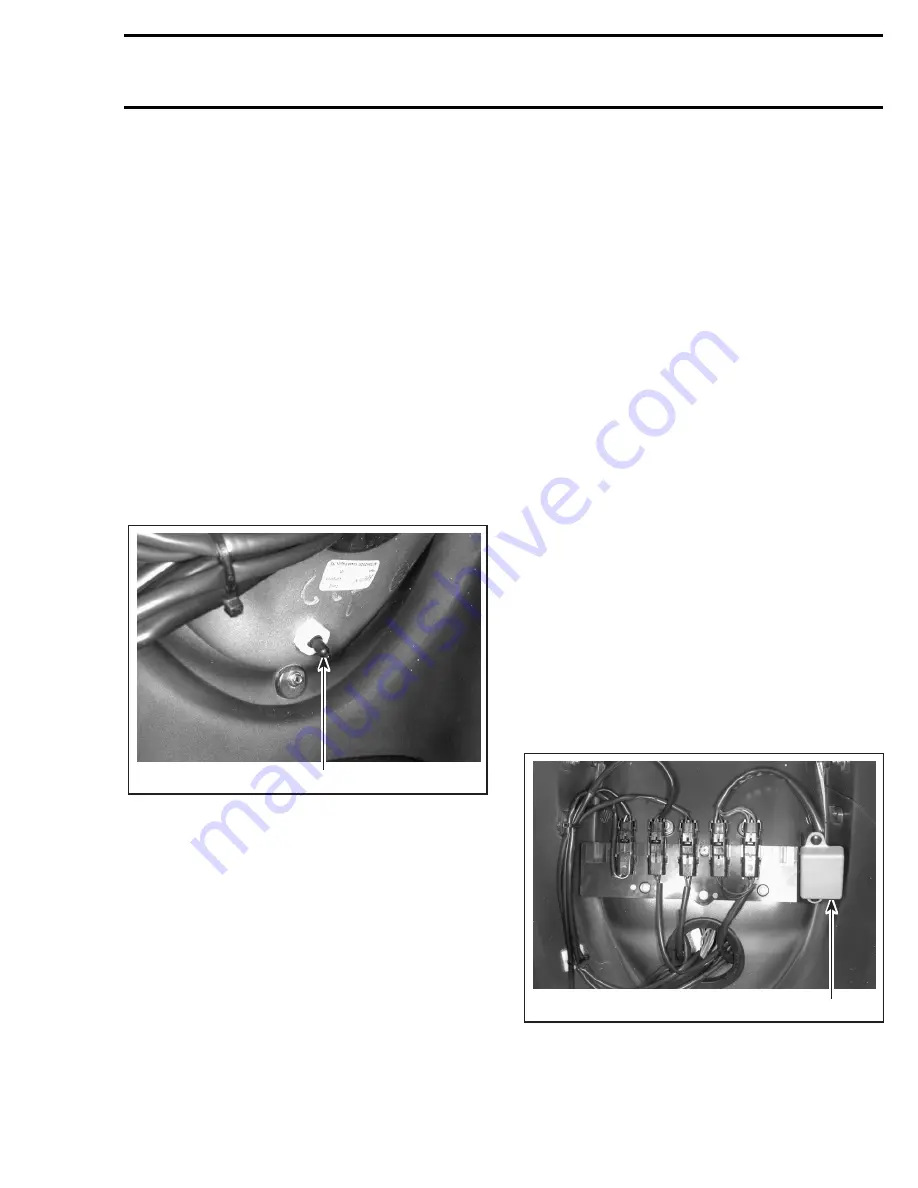
Section 01
ELECTRICAL SYSTEM
Sub-Section 01
(INSTRUMENTS AND ACCESSORIES)
01-01-1
INSTRUMENTS AND ACCESSORIES
1
GENERAL
It is possible to activate the Info Center gauge
when the engine is not running.
Make sure the safety lanyard is removed, then de-
press the start / stop button.
The gauge will be activated during 33 seconds;
the time the delay timer of the MPEM will stay on.
INSPECTION
Exterior Temperature Sensor
The temperature sensor is located in the storage
cover.
Remove the back panel of the storage cover to
access the temperature sensor.
1. Temperature sensor
To check if the temperature sensor is operational,
activate the Info Center gauge and select the ex-
terior temperature mode.
Use a heat gun to warm up the sensor. The tem-
perature should raise rapidly on the gauge.
If not, replace the temperature sensor.
Lake Temperature Sensor
The lake temperature sensor is integrated with
the speed sensor located on the ride plate.
To check if the lake temperature sensor is opera-
tional, activate the Info Center gauge and select
the lake temperature mode.
With a garden hose, spray the speed sensor with
water. The lake temperature on the Info Center
gauge should adjust to the water temperature.
If not, replace the speed sensor.
Speed Sensor
To check if the speed sensor is operational, dis-
connect the speed sensor connector housing
from inside bilge.
Using an appropriate terminal remover, remove
the PURPLE / YELLOW and BLACK / ORANGE
wires from the tab housing.
Reconnect the PURPLE / YELLOW and BLACK /
ORANGE wires in the receptacle housing.
Connect the positive probe of a voltmeter to
speed sensor PURPLE / YELLOW wire and the
negative probe to speed sensor BLACK / OR-
ANGE wire.
Depress the start / stop button to activate the de-
lay timer.
Spin the paddle wheel. There should be a voltage
fluctuation.
Compass
The compass is located in the storage cover.
Remove the back panel of the storage cover to
access the compass.
1. Compass
Remove the compass from the support.
Activate the Info Center gauge.
F07H01A
1
F07H02A
1