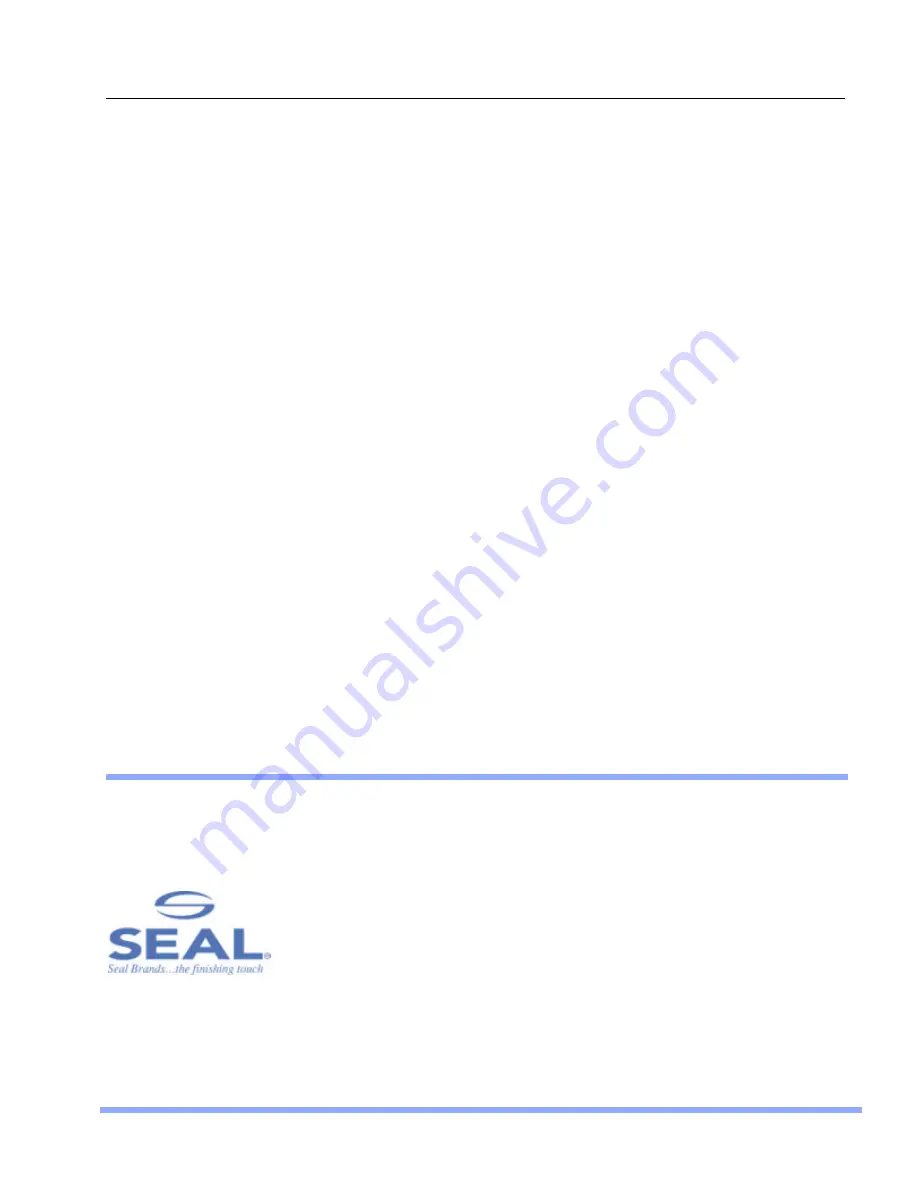
Section 4. After Sales Support
23
SEAL
Brands Technical Service
SEAL
Brands Technical Service – Europe and
(For technical assistance & service)
Asia Pacific
(For technical assistance & service)
Tel: 1-800-486-6502
For UK: Tel: +44 1268 722 400
Fax: 1-800-966-4554
Fax: +44 1268 729 442 or +44 870 125 5798
For NL: Tel: +31 572 345 500
Fax: +31 572 345 501
SEAL
Brands Customer Service
SEAL
Brands Customer Service - Europe
(For information and placing orders)
(For information and placing orders)
Tel: 1-800-257-7325
Tel: +31 572 345 500
Fax: 1-800-966-4554
Fax: +31 572 345 501
Note:
SEAL Graphics recommends that your main power be installed by a licensed electrician in accordance with electrical codes in your area.
Specifications subject to change without notice.
Seal Graphics
Seal Graphics
Seal Graphics
Seal Graphics
Seal Graphics
Americas Corporation
Canada
U.K. Ltd
Europe BV
Pacific Limited
7091 Troy Hill Drive
1601 Matheson Blvd. E
Unit 1, 1 Watkins Close
Kanaaldijk O.Z.3
Unit A, 13
th
Floor, Block 1
Elkridge, MD 21075
Unit #4
Burnt Mills Industrial Estate
P.O. Box 29,
Leader Industrial Centre
Tel: 410-379-5400
Mississauga, Ontario
Basildon, Essex SS13 1BJ
8100 AA Raalte
Tsuen Wan,
Fax: 410-579-8960
Canada, L4W 1H9
United Kingdom
The Netherlands
New Territories, Hong Kong
Tel: 905-212-9232
Tel: +44 1268 722 400
Tel: +31 572 345 500
Tel: +852 2407 3738
Fax: 905-212-9313
Fax: +44 1268 729 442
Fax: +31 572 345 501
Fax: -852 2408 0973
www.sealbrands.com
© 2002 SEAL Graphics
SEAL
and Image
are registered trademarks of SEAL Graphics
Part #OM3000-E Rev. 3
(11/02)