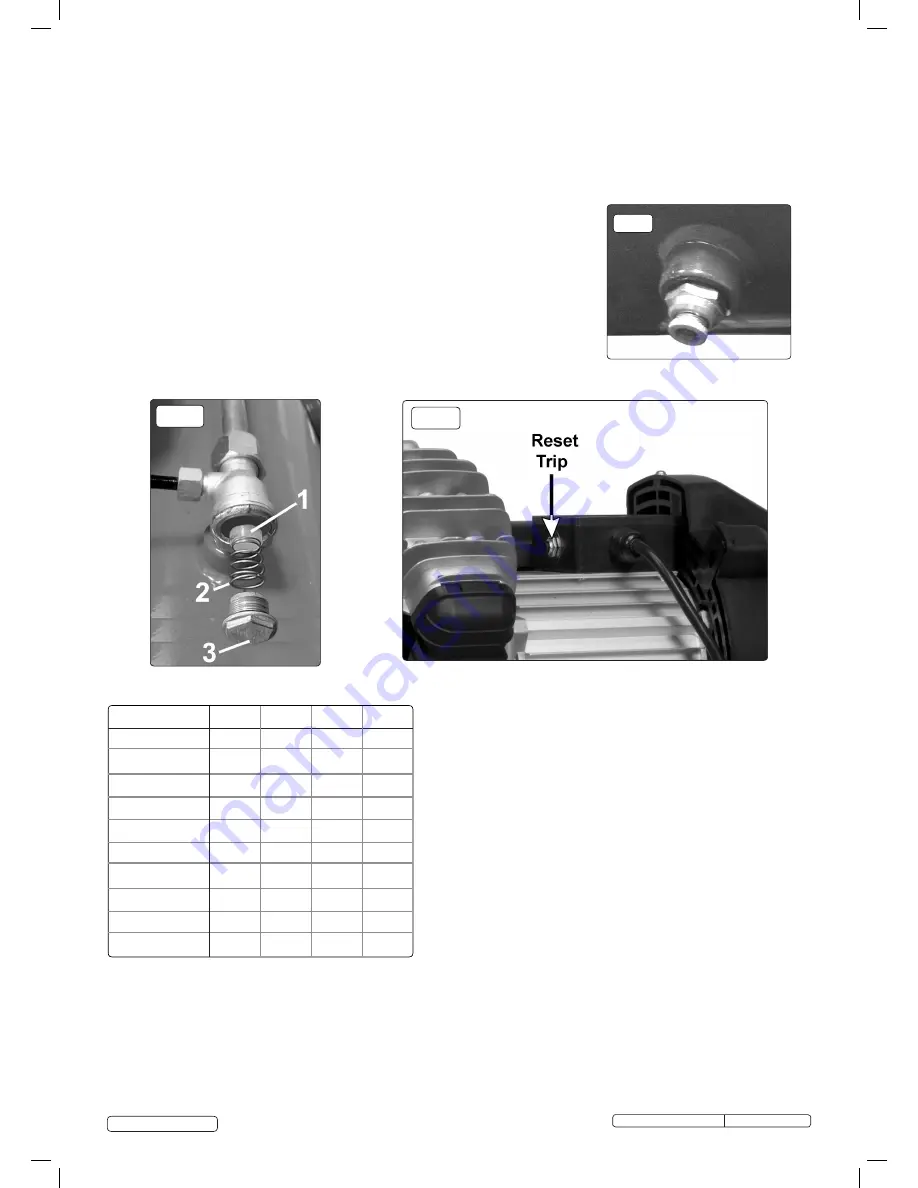
6.4. Operations to be carried out every 100 hours:
(or more frequently, if the compressor operates in a very dusty atmosphere)
a)
Check oil level, top up if necessary.
b)
Remove the filter elements. Turn off the compressor and using stored air from it's tank, clean the filters with compressed air. (Wear
eye protection and
DO NOT
direct air towards the body or hands).
DO NOT
operate the compressor without the filters as foreign
bodies or dust could seriously damage the pump. Replace the filter elements.
c)
Check for oil leaks.
6.5. Operations to be carried out every 200 hours:
a)
Check the automatic cut-out at maximum pressure, and the automatic cut-in at 2 bar below maximum pressure.
b)
Replace air filters (See 5.4).
6.6. Operations to be carried out every 400 hours:
a)
Replace the lubricating oil. For oil specifications see below.
Remove the oil filler/breather plug (fig.2.A) then unscrew oil sight glass (fig.2.B).
Drain oil into a suitable container. Drain when the compressor is hot if possible,
so that the oil drains rapidly and completely. Incline the compressor to ensure complete
drainage. Replace oil sight glass and refill with fresh oil through the oil filler/breather aperture.
Do not overfill. Replace oil filler/breather plug.
WARNING! Never mix different oils and do not use non-detergent/low quality oils, as
the compressor may be damaged.
Recommended oils: Recommended oil for compressors, suitable for temperatures ranging
from +5°C to +25°C: SEALEY CPO or equivalent SAE 40 compressor oil.
WARNING! Dispose of waste oil only in accordance with local authority requirements.
b)
Check all tube fittings and electrical connections.
c)
Inspect pressure tank inside and out for damage or corrosion.
fig.4
fig.5
fig.6
5.7. Scheduled maintenance table
•
•
Internal & external
inspection of tank
•
General cleaning of
compressor
Check tube fittings and
electrical connections
•
•
Check for oil leaks
Replace air filter
•
•
Clean intake filter
•
•
Check oil level
•
Drain condensation
400 hrs.
200 hrs.
100 hrs.
Daily
Maintenance
Operations
Replace oil
Check cut-out
5.8. IMPORTANT WARNING
- Air contaminants taken into the compressor will affect optimum performance. Example: Body filler dust or paint
overspray will clog the pump intake filter and may cause internal damage to pump/motor components. Please note that any parts damaged
by any type of contamination will not be covered by warranty.
SAC05030.V2, SAC10030.V2 Issue: 2 (L) -15/08/18
Original Language Version
© Jack Sealey Limited