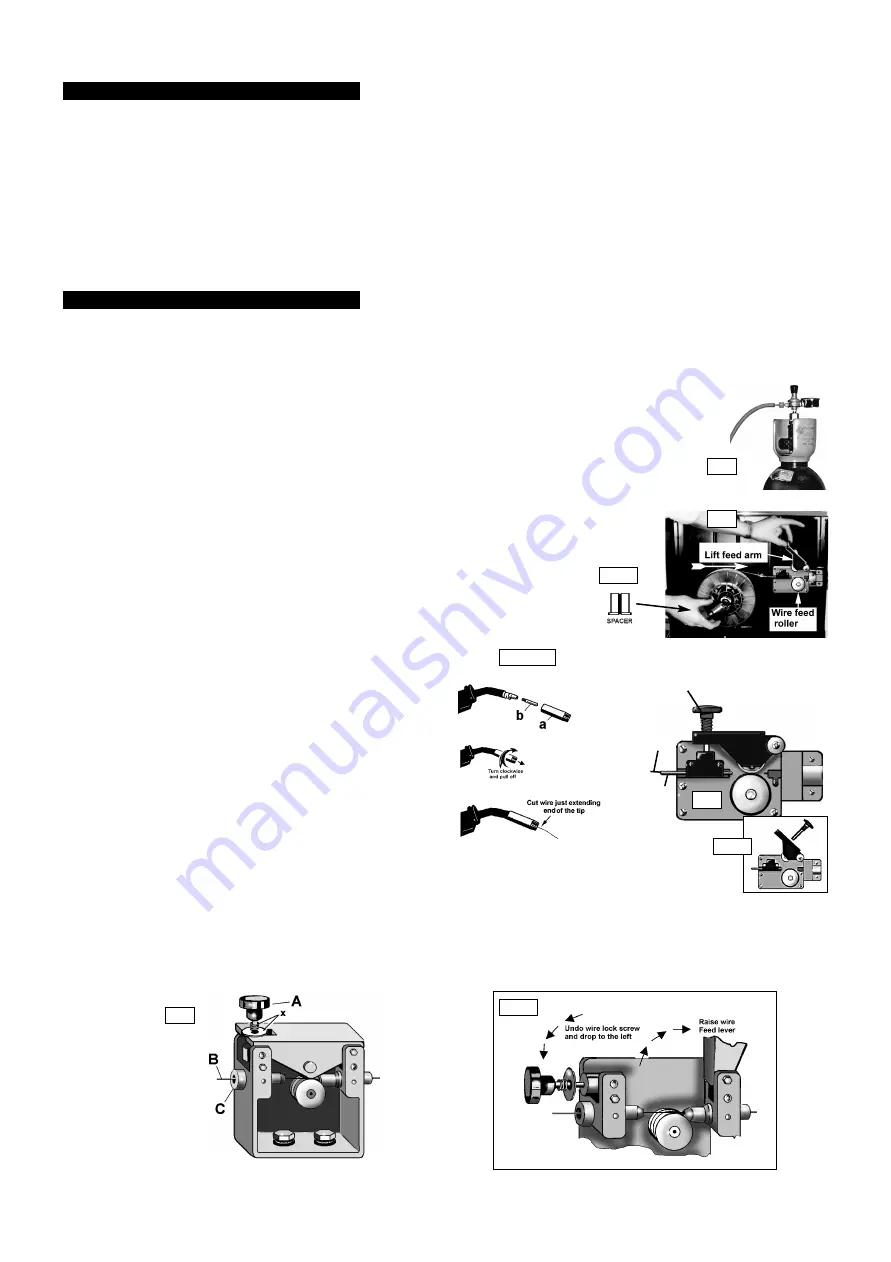
3. 1.
Wheel Assembly
Turn machine upside down and attach the front castor wheels with screw provided. Take the rear axle and fit a wheel to one end by placing on a
washer, the wheel, then a locking washer and then insert a split pin to attach the cap indents to the wheel hubs. Pass the axle through the tube under
the gas cylinder carrier, then fit the other washer, wheel, locking washer, and cap indents.
3. 2.
Connecting the gas cylinder
3. 2. 1.
When using Argon or Argon mixtures, you will need to use the bull nose adaptor enclosed. If you intend to use CO2 gas
the regulator will fit directly onto the cylinder. Fit the bull nose adaptor to the cylinder with a spanner.
3. 2. 2.
Fit the gas regulator on the bull nose adaptor and connect it to the machine gas hose (fig.1).
3. 2. 3.
Set the regulator flow rate to 5-8 litres/min depending on the material to be welded, and whether there are draughts which
are strong enough to disturb the gas flow.
3. 3.
Fitting a reel of wire -
Ensure the welder is unplugged from mains power.
Your machine comes with a mini spool of wire, but will accept up to 5kg spools without modification.
3. 3. 1.
Push the reel of wire over the reel holder end springs and onto the reel holder ensuring the spool rotates clockwise,
with the wire drawing off the reel from the top (see white arrow in fig 2). Large spools of wire have a guide hole
which must be pushed onto the plastic pin located at the end of the reel holder. This pin will stop larger reels
from free wheeling around the holder.
3. 3. 2.
To secure the reel of wire take the plastic spacer and gently open the diameter of the spacer whilst
placing over the reel holder end spring and onto the reel holder (fig 2a).
3. 3. 3.
Undo the wire lock screw (fig 3 & 4A) and lift the wire feed lever up (fig 3.1. & 4.1.).
3. 3. 4.
Straighten 40-50mm of spool wire (
do not allow wire to uncoil
), and gently push wire (fig 3 & 4 B)
through the guide (C) and through the 6 or 8mm feed roller groove (see 6.3) and through to the torch.
3. 3. 5.
Carefully return the wire feed lever and secure with the wire lock screw.
3. 3. 6.
Remove torch gas cup (fig 3.3.6. a) and contact tip (b) from end of torch as follows:
a) Take torch in left hand with the torch tip facing to the right.
b) Grasp gas cup firmly in your right hand.
c) Turn gas cup
clockwise only (c)
and pull cup out to the right.
p
WARNING!
do not turn gas cup anti-clockwise, as this will
damage internal spring.
d) Unscrew the copper contact tip (
right hand thread
) to remove.
3. 3. 7.
Check welder is switched off 0, and that the earth clamp
is away from the torch tip. Connect the welder to the mains
power supply and set the voltage switch to 4.
3. 3. 8.
Set the wire speed knob to maximum. Keep the
torch cable as straight as possible and press the torch switch.
The wire will feed through the torch.
3. 3. 9.
When wire has fed through, switch welder off, unplug from mains.
a) Take torch in left hand and screw contact tip back into place.
b) Grasp gas cup in right hand, push onto torch head and
turn
clockwise only
.
p
WARNING!
do not turn gas cup anti-clockwise, as this
will damage internal spring.
c) Cut wire so that it is just protruding 1/4 from the cup.
3. 4.
Setting wire tension
IMPORTANT: You must set the correct tension, too little or too much tension
will cause problematic wire feed and result in poor welding.
3. 4. 1.
For mild steel 0.6mm wire the wire lock screw must be fully tightened and undone
approximately two complete turns (figs 3 & 4A).
3. 4. 2.
Correct tension between the rollers is checked by slowing down the wire between the fingers. If the top feed roller skids the tension is correct. Try to
use the lowest tension possible as too high a tension will disfigure the wire and may result in blowing a fuse on the printed circuit board. When you
have completed welding, remove the torch and store in a safe, dry place.
Note: Damaged torches and cables are not covered under warranty.
fig 4
fig 1
fig 3
3. ASSEMBLY
To fit the mains power plug see safety instructions (Chapter 1).
Fig 3.3.6.
c
MODELS:
190, 190ARC,
& 210 wire
Feeder
MODELS:
235, 250,
& 260ARC.
WIre Feeder
fig 4.1
fig 3.1
fig 2a
A
This Manual
contains instructions to assist you prepare your mig set for welding, together with information on maintenance, and trouble shooting. Read this manual
carefully in order to get the best results from your machine. These instructions are not intended to show you how to be an expert welder. It is with continued practice
that you will achieve the desired results. Mig welding requires a steady hand, and time spent practising with scrap metal will be rewarded when you progress to an
actual workpiece.
These Automigs
are compact power sources with integral wire feed which protects the wire from dust and dirt (especially in Body Shops). Your Automig
is designed to operate with two diameters of welding wire, 0.6mm, & 0.8mm. (We recommend that 0,8mm wire is used for welding stainless steel and aluminium).
With correct wire & gas fitted, tune the wire speed for most favourable weld using the trim control on the front panel. Thereafter if the power output control is changed,
the autospeed device will automatically re-tune the drives speed to maintain a stable arc thus producing a consistent weld.
Automigs 190/ARC & 260/ARC
have a socket on front panel for Arc welding. Plug the electrode holder into the socket and change the Continuous Switch from
Gas to ARC position. These units may be used with hard facing, or rutile rods as well as basic electrodes (See 4.6).
ALL MODELS ARE EQUIPPED WITH:
3
Torch,
3
Mini reel of 0.6mm wire,
3
Regulator,
3
Gas hose.
2. INTRODUCTION & DESCRIPTION
fig 2
C
B
AUTOMIGS 190,210,235,250, 190ARC & 260ARC - (0095) - (1) - 010299