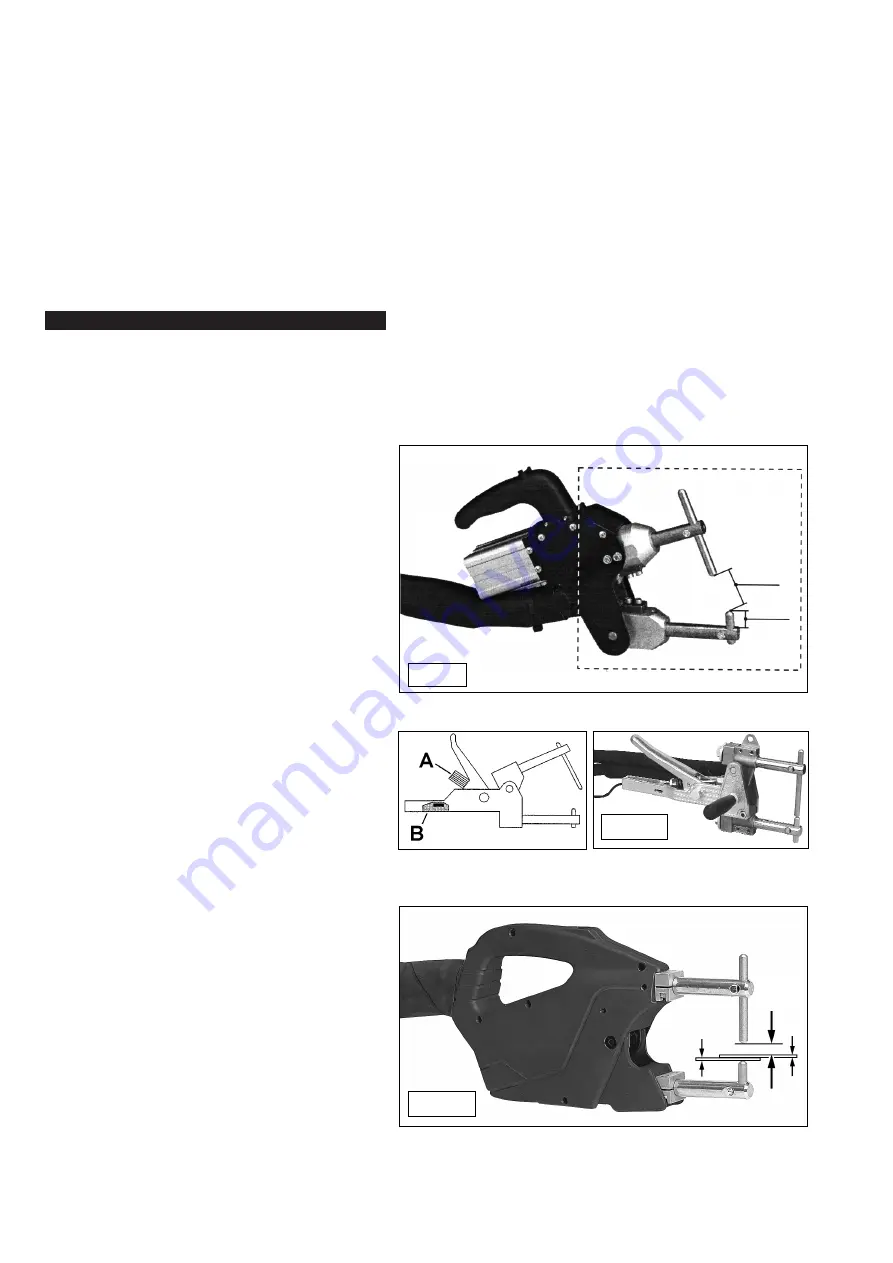
9.2.
KEYS 1 & 2
Key 1 Spot welding time and current
The welder has a programmed 5kA output suitable for a 10kVA supply. If it is necessary to alter this setting
(i.e. the machine indicates low voltage), then it can be increased or decreased with this key before welding commences. Recommended
max. welding current in kA equals half the available power in kVA, i.e. available power 8kVA, then set max. welding current to 4kA.
In order to program the current press key 2 for at least 5 seconds, to enter programming mode. Release key 2 and press key 1
to select required current - scale is marked in units of 1000(1k) amps. Press key 2 for another 5 seconds to exit programming mode.
The lower the selected current the thinner the weldable sheet and the welder will automatically indicate if the sheet thickness selected
exceeds that suitable for the programmed current.
Key 1 - as well as selecting welding current as above - will adjust spot welding time either side of the factory-set default, when not in
programme mode.
Key 2 Programme mode and sheet thickness
Key 2, if pressed for more than 5 seconds gives entry to, and exit from, the programming
mode. It is also used to specify the thickness of the sheet to be welded. If the LED corresponding to the selected thickness flashes,
then the programmed current is insufficient to weld such sheet correctly.
10. OPERATING INSTRUCTIONS
10.1.1. PRELIMINARY CHECKS
At the start of each work cycle it is important to perform the following checks,
1. Ensure that the machine is compatible with your mains supply by checking the data plate.
2. Check that the electrical connections are safe and fully engaged.
3. When you use the pneumatic clamp, connect to an air supply as described in Section 4, check the compressed air connections and
set the pressure regulator to between 5 and 8 bar.
10.1.2. PNEUMATIC CLAMP mechanical adjustment. (Standard clamp/gun for Electrospot 8000)
Mechanical adjustment of the electrodes should be carried out
with the machine switched off and the clamp to machine air
unions disconnected.
10.1.3. The electrodes should be set up to the dimensions
shown in fig.11. The lower arm should be inserted
fully into its socket and secured with the two grub
screws provided. Adjust the upward protrusion of the
short electrode to 22mm and ensure that it is vertical.
The upper arm and electrode should then be adjusted
so that the electrodes are vertically aligned when
viewed from the front and so that the tips coincide
when the clamp closes. When at rest the distance
between the electrodes should be 55mm.
10.1.4. The air pressure controls the clamping force and
should be set at between 4 and 8 bar (58 to 116psi).
The required pressure will increase with sheet thick
ness and with the diameter of the electrode faces.
10.1.5. MANUAL CLAMP adjustment. (Optional accessory 120/801043)
Position a shim (having the same thickness as the sum
of the two sheets to be welded) between the electrodes.
Ensure that, when the lever is operated, the electrode
arms are parallel and the electrode holders are in line.
Make adjustments by loosening the locking screws on
the electrode holders until you find the most suitable
position for the job to be performed. Re-tighten the
locking screws. Adjust the force of the electrodes during
welding phase by adjusting the knurled nut (fig.12.A).
Screw this nut clockwise to increase the clamp force, but adjust so that clamp will close exerting enough force to activate the
microswitch (fig. 12.B).
10.1.6. PNEUMATIC CLAMP mechanical adjustment
( Optional accessory for the Electrospot 8000
Model No.120/801045 )
1. Turn ‘ON’ the main switch
(located at the rear of the welder).
2. Position between the electrodes a shim of the same
thickness as the sheet to be welded.
3. Press the clamp push-button to close the electrodes.
4. Without any welding current:
Ensure that the electrode faces align squarely and adjust
the arms if necessary. Tighten all adjustment locking
screws. The electrode lengths should be adjusted so that
the distance between the electrodes is 8mm plus a
double thickness of the sheet material to be welded as
indicated in fig14.
This will ensure that the correct clamping force is
applied. The air pressure controls the clamping force and should be set at between 4 and 8 bar (58 to 116psi). The required pressure will
increase with sheet thickness and with electrode diameter.
55mm
22mm
fig.11
8
mm
T
T
fig.12
fig.13
fig.14
ElectroSpot 8000/9500.V2 - 2 - 040903
Summary of Contents for ELECTROSPOT 8000
Page 17: ......