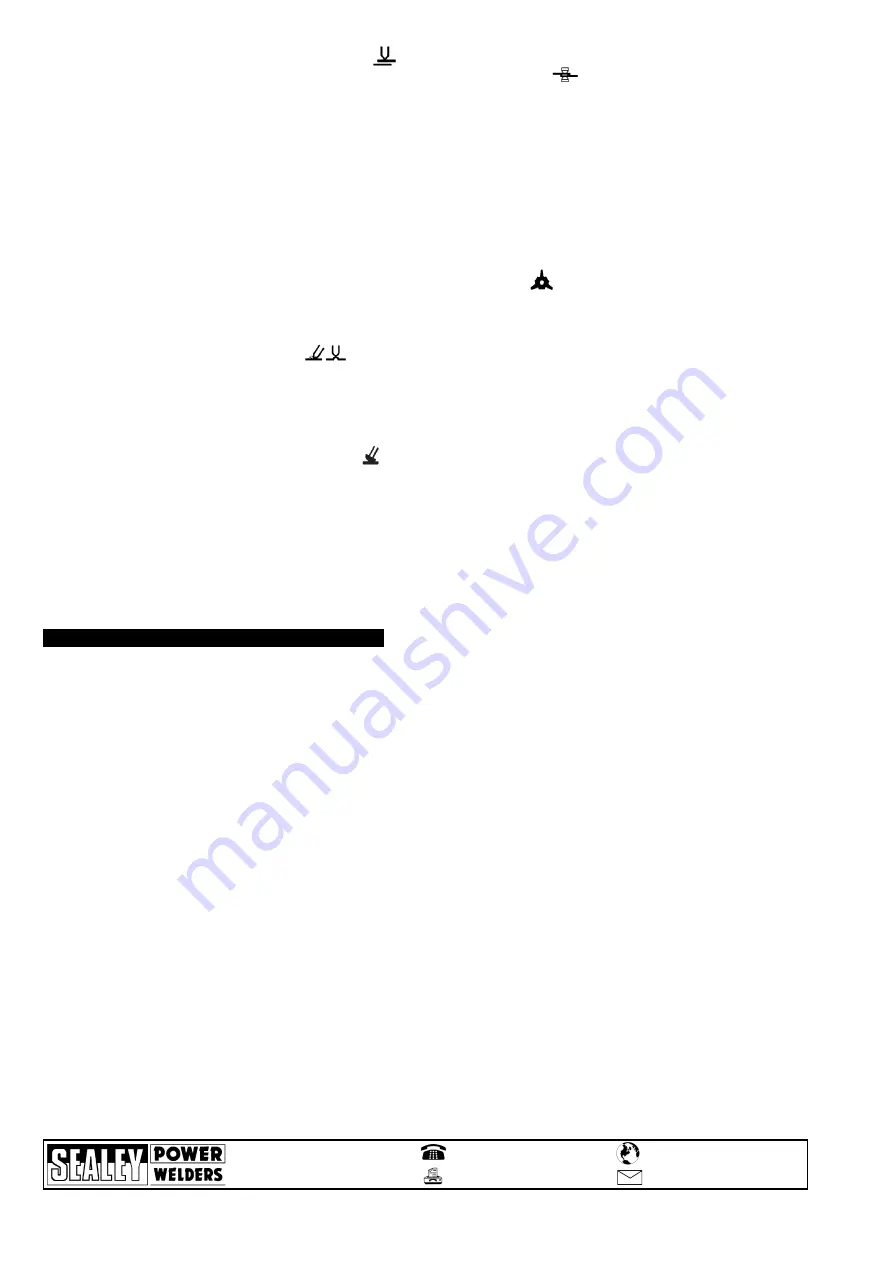
10.2.8.
SPOT WELDING SHEETS ON ONE SIDE ONLY
Fit the electrode (fig. 15.6) in the spindle and press on the surface to be
welded. Press the clamp push-button and release only after the green LED goes out.
NOTE:
The maximum sheet thickness that can be welded in this way is 1mm (i.e. 1mm per sheet, 2 sheets would therefore have a
maximum thickness of 2mm).
This method is not allowed on load bearing structures of vehicle bodies.
In order to achieve good results when spot welding sheets the following conditions must be met:
1.
A perfect ground connection.
2.
Sheets to be welded must be clean and free from varnish, grease, oil, paint etc.
3.
Sheets to be welded must be in contact with no air gap. If pressure is required to achieve this, apply pressure with a
separate tool and not with the welding clamp as too much pressure from the clamp will result in a poor weld.
4.
The thickness of the upper sheet must not exceed 1mm.
5.
The electrode face must have a 2.5mm diameter.
6.
Take care with the electrode fastening nut and ensure that the cable connectors are locked.
7.
When spot welding press lightly (3-4kg) on electrode. DO NOT move electrode until the weld is completed - green LED goes out.
8.
DO NOT attempt to weld at a position more than 300mm from the ground bar.
10.2.9.
SIMULTANEOUS TRACTION AND SPOT WELDING ON SPECIAL WASHERS.
Mount and fasten the spindle (fig. 15.4) on
the threaded end of the extractor body (fig. 15.1), and then fasten the other end of the extractor into the studder. Insert the special
washer (fig. 15.14) into the spindle and lock in place with the special screw. Spot weld washer in desired position as for normal
washer spot welding and then apply traction. Once finished, rotate extractor by 90
O
to remove the washer which can then be re-used.
10.2.10. HEATING AND SHEET UPSETTING
For these operations the timer is inoperative. The current duration is thus
determined by the operator. Current is controlled automatically according to the sheet thickness.
Mount the carbon electrode (fig. 15.12) on the studder spindle and lock in place by tightening the nut ring.
Touch the carbon face of the electrode on the work area and press clamp push-button. Operate from the outside towards the inside
of the work area, using circular movements to heat the sheet, which will go back to its original position. In order to prevent the sheet
from tempering too much, work on a small area and, when finished, immediately wipe with a wet cloth to cool.
10.2.11. INTERMITTENT SPOT WELDING (PATCHING)
To weld small rectangular pieces of sheet over holes caused by corrosion or
minor damage. Mount the electrode (fig. 15.5) on the studder spindle and tighten ring nut.
Position the patch piece and press the electrode on it - press the clamp push-button and keep it pressed. Move the electrode during
each ‘pause’ in the weld/pause cycle provided by the machine.
The work/pause cycles are controlled automatically by the spot welder according to sheet thickness.
Keep a light pressure on the electrode (3-4kg) and weld along a line ideally 2-3mm in from the edge of the new piece.
To achieve good results:
DO NOT weld more than 300mm from ground point.
Use sheet of 0.8mm maximum thickness.
Only move electrode during the ‘pauses’ - never when welding.
10.2.12. EXTRACTOR (fig. 12.1)
Mount and lock the hook spindle (fig. 15.3) onto the extractor (fig. 15.1). Hook washer (fig. 15.13), previously
welded as in 10.11, and begin traction. When finished, rotate the extractor through 90
O
to break off washer.
11. MAINTENANCE
!
WARNING! DO NOT remove any panels without first switching the machine off and unplugging the unit from mains power supply.
11.1.
Periodically, depending on environmental conditions, remove panels and clean dust and metallic particles from inside the welder using
dry, compressed air at no more than 10 bar pressure (wear safety eye protection and dust mask).
Avoid directing compressed air at the electronic circuit board - rather, clean with a soft brush and suitable solvents.
11.2.
Check that all cables are in good condition with undamaged insulation and clean un-oxidised connectors.
11.3.
Check that screws connecting the transformer secondary circuit to the welding cable taps are secure and do not show signs of
overheating or oxidation.
11.4.
If the welder is not operating correctly check the following before contacting your service agent.
a) With welder connected to mains supply and welder mains switched ‘Off’ green LED should be on. If not there is a supply fault or
the supply voltage is too low.
b) That the microswitch in the clamp is operating correctly and signalling the electronic circuits - green (welding) LED on.
c) Thermal protection has not triggered (yellow LED flashed).
d) The connections in the secondary circuit (fuse, arm holders, arms, electrode holder), are not producing high resistance due to
loose screws or oxidised contact surfaces.
e) The electrode face diameter and the electrode pressure being used are appropriate to the weld being produced.
11.5.
Periodically clean the water cooler filter (ElectroSpot 9500 only).
NOTE:
It is our policy to continually improve products and as such we reserve the right to alter data, specifications and component parts without prior notice.
IMPORTANT:
No liability is accepted for incorrect use of this equipment.
WARRANTY:
Guarantee is 12 months from purchase date, proof of which will be required for any claim.
INFORMATION:
For a copy of our latest catalogue and promotions call us on 01284 757525 and leave your full name and address, including postcode.
01284 757500
01284 703534
sales@sealey.co.uk
Sole UK Distributor
Sealey Group,
Bury St. Edmunds, Suffolk.
www.sealey.co.uk
Web
ElectroSpot 8000/9500.V2 - 2 - 040903
Summary of Contents for ELECTROSPOT 8000
Page 17: ......