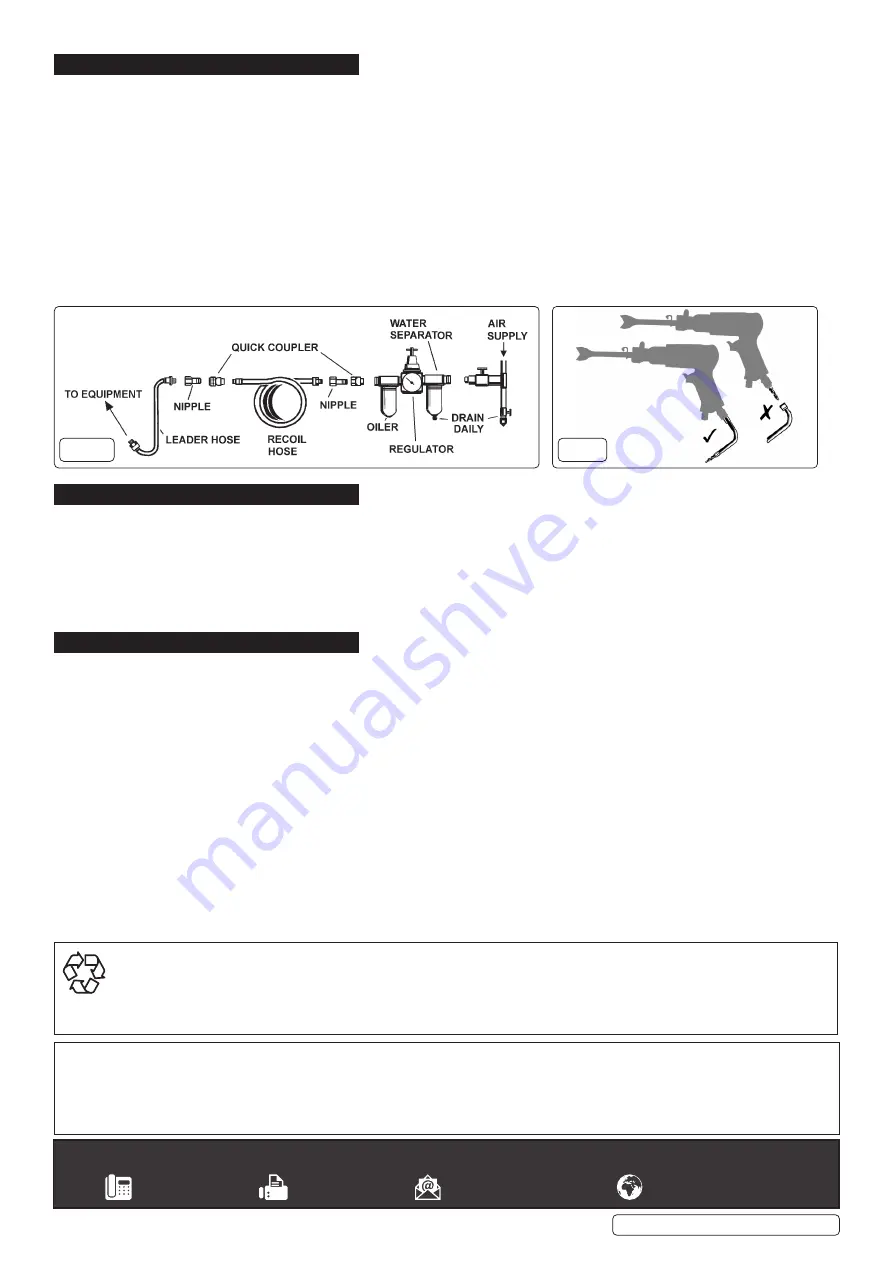
Original Language Version
© Jack Sealey Limited
4. AIR SUPPLY
4.1.
Recommended hook-up procedure is shown in fig.1.
4.2.
Ensure tool air valve (or trigger) is in “off” position before connecting to the air supply.
4.3.
You will require an air pressure of 90psi, and an air flow according to specification.
WARNING!
Ensure the air supply is clean and does not exceed 90psi while operating the tool. Too high an air pressure and unclean air
will shorten the product life due to excessive wear, and may be dangerous causing damage and/or personal injury.
4.4.
Drain the compressor air tank daily. Water in the air line will damage the tool.
4.5.
Clean compressor air inlet filter weekly.
4.6.
Line pressure should be increased to compensate for unusually long air hoses (over 8 metres). The minimum hose diameter should be
1/4” I.D. and fittings must have the same inside dimensions.
4.7.
Keep hose away from heat, oil and sharp edges. Check hose for wear, and make certain that all connections are secure.
4.8.
COUPLINGS
4.8.1.
Vibration may cause failure if a quick change coupling is connected directly to the tool.
4.8.2.
To overcome this, connect a leader hose to the tool. A quick change coupling may then be used to connect the leader hose to the air
line recoil hose. See figs.1 & 2.
5. OPERATION
Note: Numbers in brackets refer to item numbers in the parts list.
5.1.
The air hammer is designed primarily for use on vehicle bodywork. We do not recommend any other use. Ensure you read, understand
and follow the safety instructions in Section 1.
5.2.
Attach the retaining spring (7) by screwing it onto the cylinder (6).
5.3.
Insert the chisel using the hooked end of the spring to hold the chisel in place.
5.4.
Attached the tool to the air supply (see Section 4).
5.5.
To operate the hammer, squeeze the trigger.
6. MAINTENENCE
WARNING!
Disconnect the hammer from the air supply before changing chisels, servicing or performing any maintenance.
6.1.
Keep the hammer oiled for optimum performance.
Lubricate with a good grade of air tool oil such as Sealey ATO/500 or ATO/1000.
If there is no oiler in the air system then a teaspoon of oil can be poured into the air inlet of the hammer, or into the hose at the nearest
connection to the air supply. Then run the hammer for a short time.
Note:
The following external factors may cause loss of power and effect hammer performance:
6.2.
The air supply:
reduced compressor output, excessive drain on the air line, moisture or restrictions in air pipes or the use of hose
connectors having too small a bore. Correct as necessary.
6.3.
The hammer:
grit or gum deposits in the tool. Correct by cleaning the air strainer and flushing out the tool with gum solvent oil or an
equal mixture of SAE No.10 oil and kerosene. If, despite taking action as above, the tool function is still impaired, contact your local
Sealey service agent.
fig.1
fig.2
Sealey Group, Kempson Way, Suffolk Business Park, Bury St Edmunds, Suffolk. IP32 7AR
01284 757500
01284 703534
sales@sealey.co.uk
www.sealey.co.uk
ENVIRONMENT PROTECTION
Recycle unwanted materials instead of disposing of them as waste. All tools, accessories and packaging should be sorted, taken to
a recycling centre and disposed of in a manner which is compatible with the environment. When the product becomes completely
unserviceable and requires disposal, drain any fluids (if applicable) into approved containers and dispose of the product and fluids
according to local regulations.
Note
: It is our policy to continually improve products and as such we reserve the right to alter data, specifications and component parts without prior
notice. Please note that other versions of this product are available. If you require documentation for alternative versions, please email or call
our technical team on technical@sealey.co.uk or 01284 757505.
Important
: No Liability is accepted for incorrect use of this product.
Warranty
: Guarantee is 12 months from purchase date, proof of which is required for any claim.
GSA12.V2 Issue:1 23/12/20