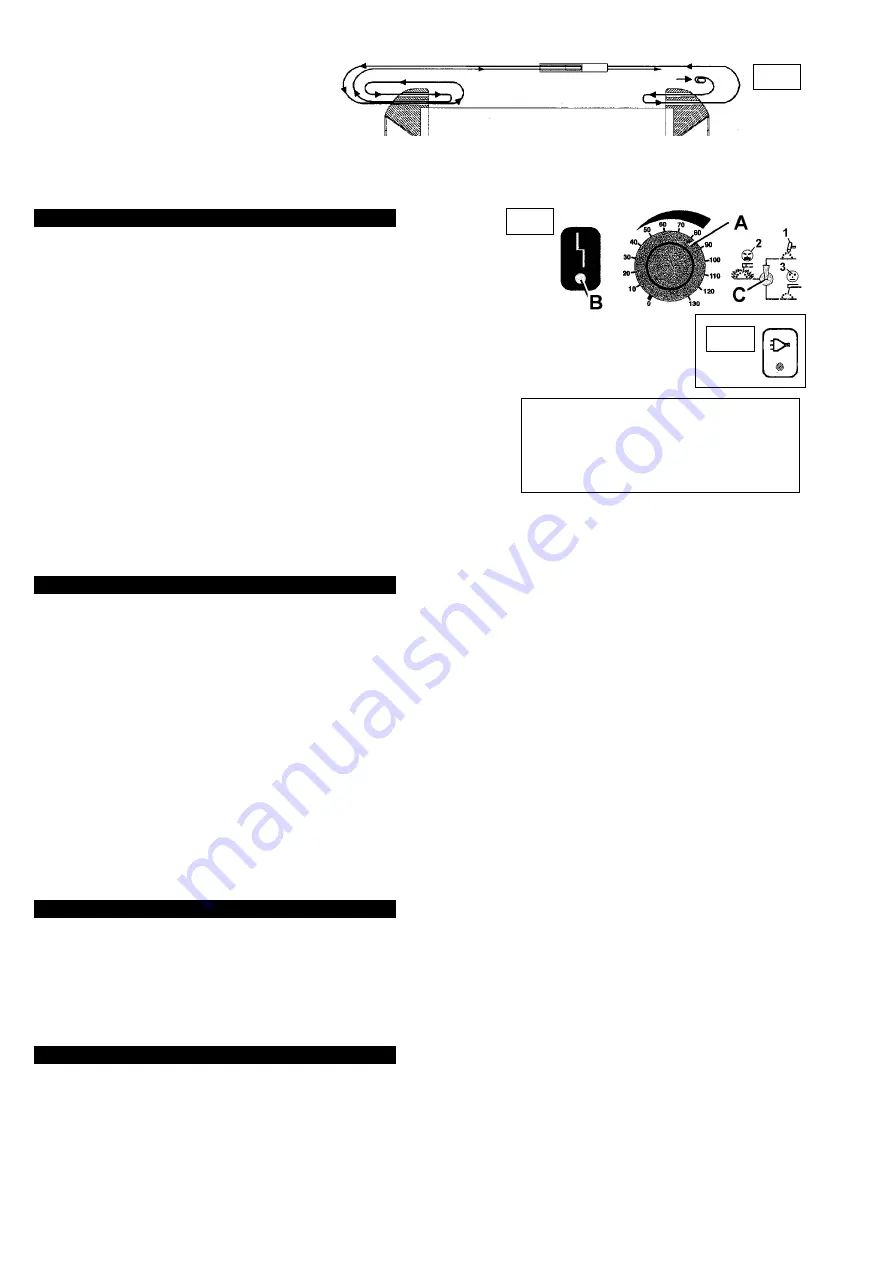
p
p
WARNING! Ensure that you read, understand and follow the safety instructions. Place the welding mask in front of your face before striking the arc.
5.1.
ARC WELDING (Arc welding accessory kits available, contact you Sealey dealer)
5.1.1. Strike the electrode tip on the workpiece as if you were striking a match.
p
p
WARNING! DO NOT hit the electrode on the workpiece, as this may damage the electrode.
5.1.2. As soon as the arc is ignited, maintain a distance from the workpiece equal to the diameter of the electrode being used. Keep this distance as constant
as possible for the duration of the weld. As you advance along the workpiece the angle of the electrode must be maintained between 20
O
to 30
O
.
5.1.3
.
At the end of the weld bead, bring the end of the electrode backward in order to fill the weld crater, quickly lift the electrode from the weld pool to
extinguish the arc.
5.2.
TIG WELDING (TIG welding accessory kits available, contact you Sealey dealer).
TIG (Tungsten Inert Gas) welding uses an arc between a tungsten electrode and the work to fuse the joint. The electrode itself is not consumed and filler
metal may be required to build the weld profile.The process is protected from atmospheric contamination by a shield of inert gas. This gas is normally pure
argon, but helium by itself or a mixture of helium and argon may be used for special applications. For stainless steel use a mixture of argon and hydrogen.
5.2.1. Strike the electrode tip on the workpiece as if you were striking a match.
p
p
WARNING! DO NOT hit the electrode on the workpiece, as this may damage the electrode.
5.2.2. Point the electrode in the direction of the weld at about 2.5mm distance from the surface and use the arc to melt the metal at the joint.
5.2.3. To increase or decrease flow of gas, use the control knob on the torch handle.
5.2.4. Filler metal may be added by using cut lengths of wire over 1.5mm diameter (usually 1 metre in length). To use filler metal (for example when making a
fillet weld), add it to the leading edge of the weld pool.
4. CONTROLS & PREPARATION
fig. 4
4.1.
CONTROLS figs. 4 & 5
A.
Potentiometer:
To regulate welding current with scale graduated in Amps. May be regulated during welding.
B
.
Yellow LED:
Normally off. When on it means no welding current due to one of the following faults:
1. Thermal protection: Inside machine the temperature is excessive. The machine is ON but will not
deliver current until a normal temperature is reached. Once this happens the re-start is automatic.
2. Mains over/under voltage protection: When mains voltage is too high (over 260V) or too low
(under 190V) the machine is blocked.
3. Short circuit protection: If there is a short-circuit lasting more than 1.5 seconds (i.e. electrode sticking), machine stops.
Re-start is automatic.
C.
Models MW150 & MW170 Function Selection Switch:
Enables the setting of the machine dynamics:
1. TIG: To gain maximum arc current stability.
2. HARD: To get maximum welding dynamics (hot start and arc force. Suitable for welding with hard electrodes (basic, aluminium etc).
3. SOFT: To weld with soft electrodes (rutile, inox etc.).
Models MW140.V2 & MW140PLUS: Green LED,
mains power indicator, machine ready (fig. 5).
4.2.
WELDING CURRENT
The welding current must be regulated according to the diameter of the electrode in use (see
chart on right) and the type of joint to be welded.
Further consideration must be given to the location of a weld, for example: Welds that are
performed on a horizontal surface require a higher voltage than those performed on a vertical
or overhead surface.
The mechanical character of the weld will be determined not only by the current intensity used, but also by the diameter and quality of the electrode, the
length of arc, the speed and position of the user. The condition of the electrode is an important factor and must never be wet or damp.
Electrode Diameter (mm)
Welding Current (Amp)
Min
Max
1.6 . . . . . . . . . . . . . . . . . . . . .25 . . . . . . . . . .50
2.0 . . . . . . . . . . . . . . . . . . . . .40 . . . . . . . . . .80
2.5 . . . . . . . . . . . . . . . . . . . . .60 . . . . . . . . .110
3.2 . . . . . . . . . . . . . . . . . . . . .80 . . . . . . . . .160
4.0 . . . . . . . . . . . . . . . . . . . .120 . . . . . . . . .200
5. WELDING PROCEDURE
fig. 5
3.3.
CARRY STRAP
If not already fitted, follow the carrying strap
assembly as pictured in fig. 3.
fig. 3
Should you have a problem with the welder, check the following:
l
That the welding current is correct for the diameter and type of electrode being used.
l
That when the main switch is on, the power lamp is ON. If this is not the case then there may be a mains supply problem.
l
That the yellow LED is not illuminated. If it is this indicates either an over-voltage, an under-voltage or a short circuit.
l
That the normal intermittence ratio is correct, and that the fan is working correctly.
l
That you are using the correct voltage.
l
That the cables are undamaged and that there is nothing causing a short-circuit.
l
That all circuit connections are correct. In particular check that the work clamp is correctly attached to the workpiece. Ensure that there is no grease, paint etc on the contact surfaces.
7. TROUBLESHOOTING
6. MAINTENANCE
p
WARNING! DISCONNECT FROM THE MAINS ELECTRICAL SUPPLY AND WAIT FOR CIRCUIT LIGHT TO GO OUT BEFORE ATTEMPTING TO OPEN THE UNIT.
Periodically remove cover and lightly remove dust inside the machine by passing a low pressure air flow through. Ensure the cover is correctly replaced and secured
before attempting to use the welder.
Keep the outside of the machine clean by wiping with a soft dry cloth.
For any other service or maintenance, contact your local Sealey service agent.
MW140.V2, MW140PLUS, MW150, MW170 - 1 - 110303