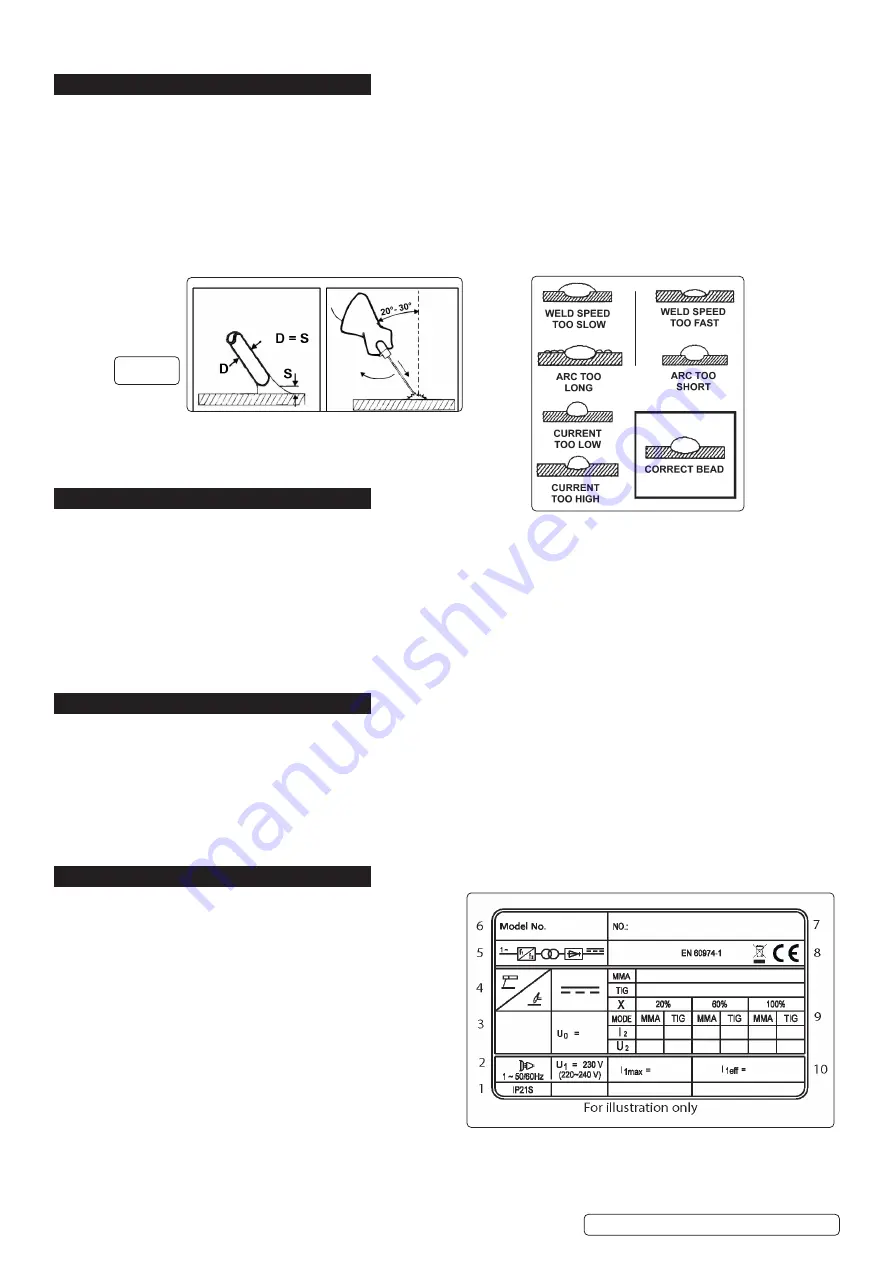
5. WELDING PROCEDURE
WARNING!
Ensure that you read, understand and follow the safety instructions. Place the welding mask in front of your
face before striking the arc.
5.1.
ARC WELDING
5.1.1.
Strike the electrode tip on the workpiece as if you were striking a match.
WARNING! DO NOT
hit the electrode on the workpiece, as this may damage the electrode.
5.1.2.
As soon as the arc is struck, maintain a distance from the workpiece equal to the diameter of the electrode. Keep this distance as
constant
as possible for the duration of the weld. As you advance along the workpiece the angle of the electrode must be maintained
at between 20º and 30º. See fig.4.
5.1.3.
At the finish of the weld, bring the end of the electrode backward in order to fill the weld crater and then quickly lift the electrode from
the weld pool to extinguish the arc.
WARNING!
Hot metal such as electrode stubs and workpieces should never be handled without gloves.
6. MAINTENANCE
WARNING!
Before carrying out routine maintenance, switch off the welding and disconnect it from the mains power supply.
WARNING!
If the welding machine is not functioning properly repairs should be carried out only and by authorised service
engineers.
WARNING!
Before removing the welding machine panels switch off the machine and disconnect it from the mains power
supply. Wait 10-15 seconds after the unit is switched off for the capacitor to discharge.
6.1.
Periodically remove the casing and, with a low pressure air flow (max 1bar or15psi),remove dust from inside the machine.
8
DO NOT
direct compressed air onto the electronic circuit boards, these should be cleaned with a very soft brush.
6.2.
Ensure that all electrical connections are tight and check the wiring for damage to the insulation.
6.3.
Ensure that the casing is correctly replaced and secured before attempting to use the inverter.
6.4.
Keep the outside of the machine clean by wiping with a soft, dry cloth.
6.5.
For any other service or maintenance, contact your local Sealey service agent.
7. TROUBLESHOOTING
7.1.
If you have a problem with the inverter, check to ensure that the following are correct:
7.1.1.
Check that the welding current is suitable for the diameter and type of electrode being used.
7.1.2.
When the mains switch is on, check that the power lamp is on. If this is not the case then there may be a mains supply problem.
7.1.3.
Check the overheat indicator - has the thermal cut-out activated? This indicates either an over or under voltage or short circuit. If the
thermal interrupter has activated, wait for the machine to cool down before restarting.
7.1.4.
Ensure that you are using the correct supply voltage.
7.1.5.
Check the machine output and ensure there is nothing causing a short-circuit.
7.1.6.
Check that all circuit connections are correct. In particular check that the work clamp is correctly attached to the workpiece. Ensure that
there is no grease, paint etc. on the surface.
8. RATING PLATE
The rating plate on the inverter gives the following data:
1 - Rating of internal protection provided by casing.
2 - Symbol for power supply line: 1= Single-phase AC.
3 - Indicates that welding may be carried out in
environments with a heightened risk of electric shock eg very close to
large metallic objects.
4 - Welding procedure: manual arc welding with covered electrode
5 - Symbol for internal structure of the welding machine.
6 - Model No.
7 - Manufacturers Serial Number for welding machine identification.
8 - The EUROPEAN standard relating to the safety and construction of
arc welding machines.
9 - Output.
Uº: Maximum no load voltage.
I², U²: Current and corresponding normalised voltage that the welding
machine can supply during welding.
X: Welding ratio based on a 10 minute duty cycle. 30% indicates 3
minutes welding and 7 minutes rest, 100%
indicates continuous
welding. A/V-A/V: Shows the adjustment for the welding current (min - max) the corresponding
arc voltage.
10 - Power Supply
U
1
: Alternating voltage and power supply frequency of welding machine.(allowed limit ± 10%)
Fig. 4
Original Language Version
© Jack Sealey Limited
MW180i, MW200i Issue:1 24/11/21