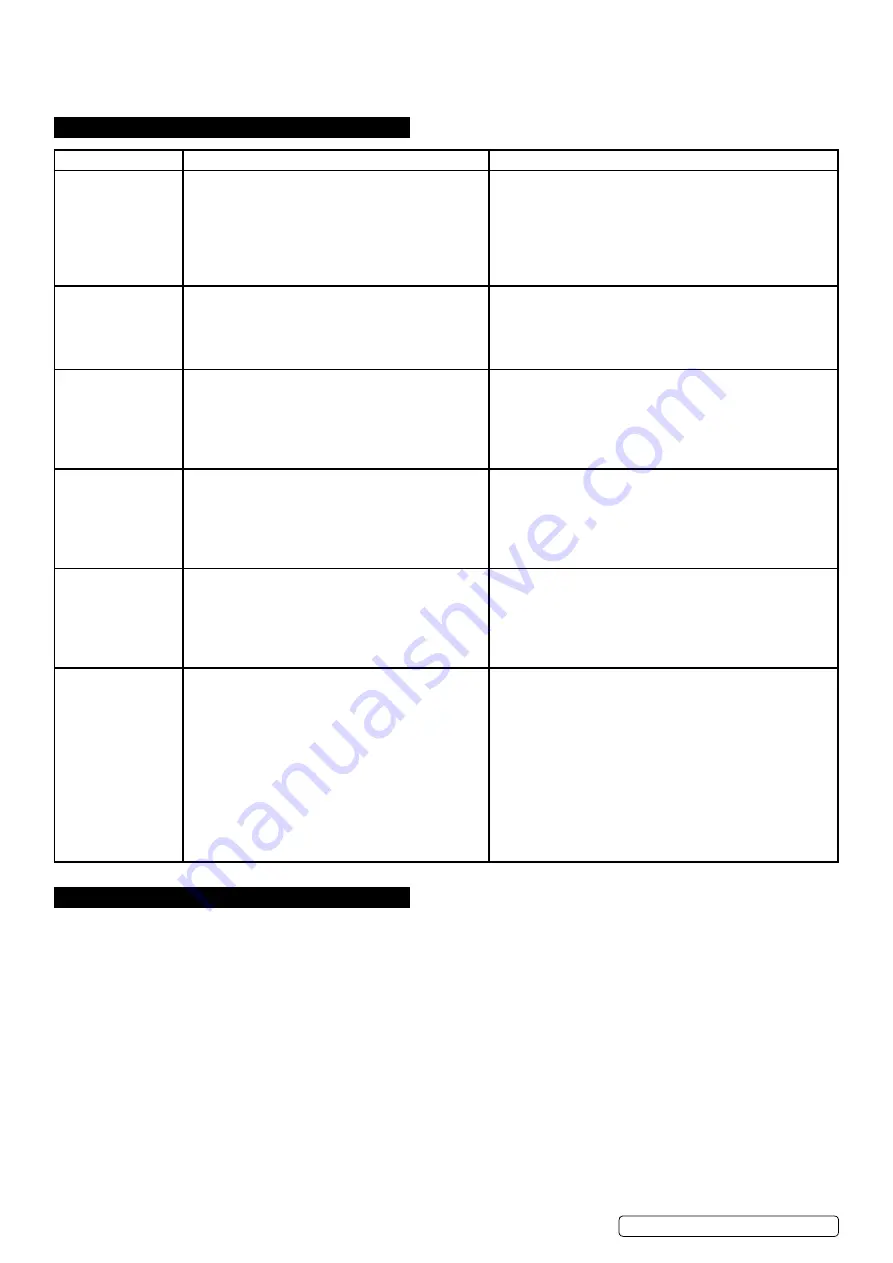
Keep a space between the nozzle and the workpiece. Pressing the nozzle on the workpiece could cause the nozzle to stick, reducing the
smoothness of the cutting action.
Keep the torch vertical against the workpiece and watch to make sure the arc is moving along the cutting line.
8
Do not
rapidly switch the torch trigger on and off this will damage the pilot arc system and the work piece.
7. troUBleshootinG
8. electromaGnetic compatiBilitY
8.1.
this eqUipment is in conFormitY with the eUropean stanDarD on the electromaGnetic compatiBilitY
oF arc welDinG eqUipment anD similar processes (e.g. arc anD plasma cUttinG )
8.2.
protection against interference.
(e.m.C.) The emission limits in this standard may not, however, provide full protection against
interference to radio and television reception when the equipment is used closer than 30m to the receiving antenna. In special cases,
when highly susceptible apparatus is being used in close proximity, additional mitigation measures may have to be employed in order
to reduce the electromagnetic emissions.
8.3.
installation and use
. The user is responsible for installing and using the equipment according to these instructions. If electromagnetic
disturbances are detected, then it shall be the responsibility of the user of the equipment to resolve the situation with the technical
assistance of the supplier. In some cases this remedial action may be as simple as earthing the circuit (see note:). In other cases it
could involve constructing an electromagnetic screen, enclosing the welding power source and the work, complete with associated
input filters. In all cases the electromagnetic the electromagnetic disturbances shall be reduced to the point where they are no longer
troublesome. note: The welding/cutting circuit may or may not be earthed for safety reasons. Changing the earthing arrangements should
only be authorised by a person who is competent to assess whether the changes will increase the risk of injury, e.g. by allowing parallel
welding/cutting circuit return paths which may damage the earth circuits of other equipment.
Original Language Version
© Jack Sealey limited
symptom
possible cause
corrective action
Power Indicator
light is off after
turning on the power
supply.
1. The light is broken.
2. Fuse is blown.
3. not 230V Input Voltage.
4. Power supply switch is broken.
5. Controlling board or cutter is damaged.
1. Replace.
2. Replace.
3. Connect the 240V Input cable.
4. Replace.
5. examine and repair.
Fan doesn’t work
after turning on the
power supply.
1. Fan is damaged.
2. Fan’s ground lead is broken.
3. Fan’s blade is blocked
4. Transformer is damaged.
1. Replace.
2. examine and repair.
3. Clean the block.
4. Replace.
Will not cut
1. discharge gap is too big.
2. main controlling board is damaged.
3.Ground lead is broken
1. Adjust to suitable gap.
2. Replace.
3. Replace.
4. examine and repair.
5. examine and repair.
no response after
turning on the torch
switch.
1. Switch and ground-lead are broken.
2. Switch board is broken.
3. main controlling board is damaged.
4. Transformer is damaged.
5. Ground lead is broken.
1. examine and repair or replace.
2. examine and repair or replace.
3. examine and repair or replace.
4. Replace.
5. examine and repair.
no response after
turning on power
supply.
1. Power cord hooked up wrong.
2. Power supply switch is broken.
3. Fuse is damaged.
4. Transformer is broken.
5. main controlling board is ruined.
1. examine and repair.
2. Replace.
3. Replace.
4. Replace.
5. examine and repair or replace.
Protection indicator
light comes on.
1. High/low voltage
2. The High/low voltage setting is incorrect.
3. over heating from exceeding the duty cycle.
4. The bad or broken connection in the thermal relay.
5. main PCB board is broken.
1. The tolerant voltage range is 200V ~ 250V. The machine
will stop working and indicator will come on if the input power
voltage is not between 220V and 240V AC. Please check the
voltage with a volt meter.
2. Please open the case to adjust the potentiometer RP3 (for
high voltage setting or low voltage setting) on the main control
PCB. note: RP3 should be adjusted clockwise, the RP3
should be adjusted counter clockwise.
3. Wait until the machine cools down.
4. Repaired by the qualified people.
5. Replace.
PP40PlUS | Issue:1 29/08/18