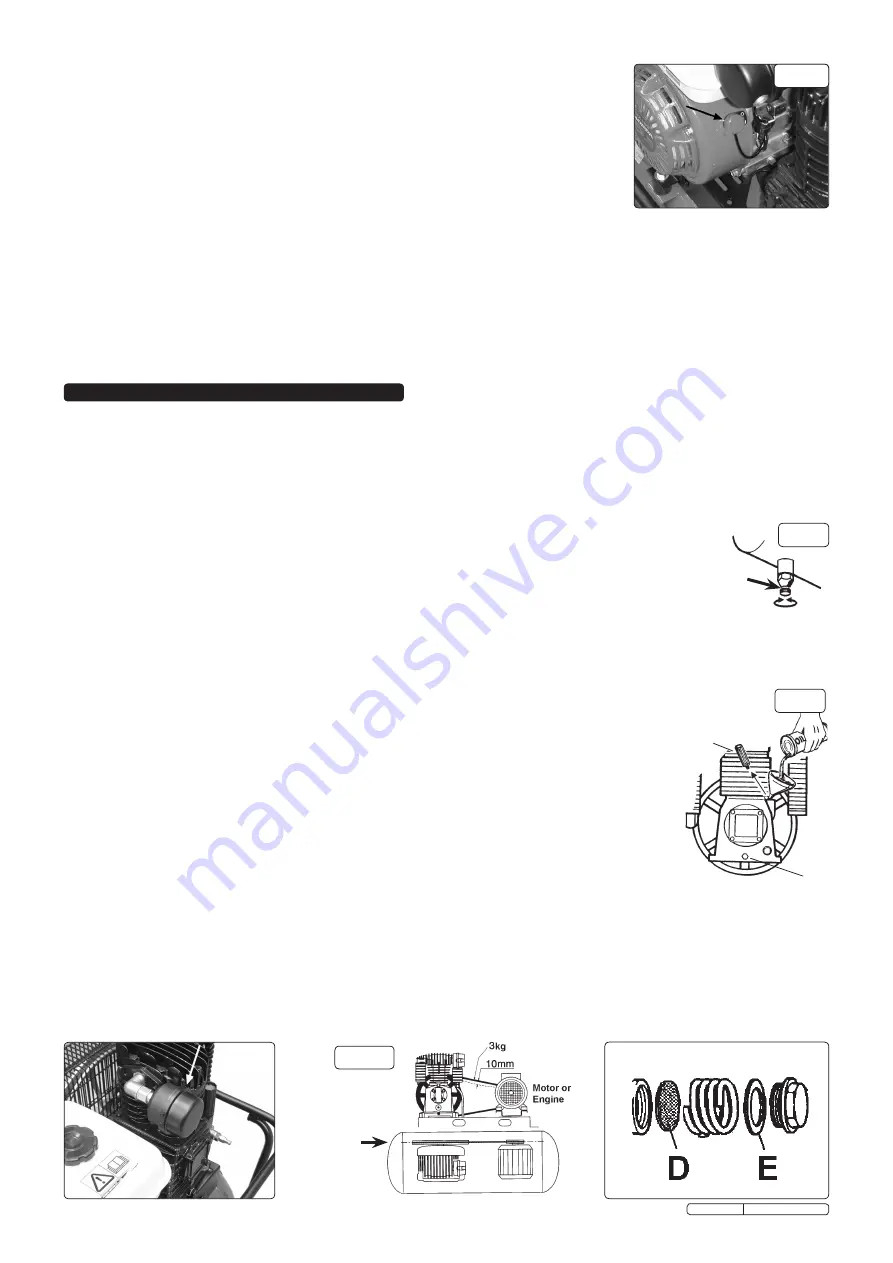
4.2.
STOPPING
4.2.1. To stop the compressor turn the engine ignition switch (fig.4) to Off (O). See the engine
manufacturer’s handbook for the complete engine shutdown procedure.
4.3.
CONNECTING AIR POWERED EQUIPMENT
4.3.1. After fitting the desired coupling to the outlet valve (fig.3.B) connect the air hose and
equipment.
4.3.2. Adjust the regulator valve (fig.3.A) to the required output pressure (in accordance with the air
equipment instructions) by lifting and turning the regulator knob. Push the knob down to lock
it at the required pressure (see output gauge, fig.3.c). Turn on outlet valve (fig.3.B).
Note:
To determine the correct working pressure and air flow requirements for any piece of
equipment
check the corresponding manual. Be aware that the air flow figure stated on tools and
accessories refers to ‘Free Air delivery’ and not the piston displacement of the compressor. When adjusting the regulator, always adjust
up to
the required pressure.
4.3.3. To disconnect equipment, turn the regulator valve anti-clockwise to ‘zero’ (0) bar. Operate the equipment to depressurise the air line
and then disconnect from the compressor.
4.4.
WHEN WORK IS COMPLETE
At the end of each working day, drain any moisture from the main tank. Place a container under the drain plug and then carefully
unscrew it (fig.5).
DO NOT
allow moisture to accumulate in the tank as this will corrode the inside and affect the pressure rating of the
tank.
WARNING!
Wear safety goggles when performing this task.
5. MAINTENANCE
fig. 4
fig. 9
fig. 7
In order to keep the compressor in good working condition, periodic maintenance is essential.
IMPORTANT! Failure to carry out maintenance tasks may invalidate the warranty on your compressor.
WARNING! Service and maintenance must be performed by an authorised agent. DO NOT tamper with, or attempt to adjust, the
pressure switch or safety valve. Before moving, or carrying out any maintenance on the compressor,
ensure that the ignition switch
is ‘off’ and that the air tank pressure has been vented.
5.1.
ENGINE
See the engine manufacturer’s handbook (supplied) for the engine maintenance schedule.
5.2.
COMPRESSOR (LESS ENGINE)
5.2.1. Operations to be carried out
after the first 50 working hours:
a) check that all bolts/nuts are tight, particularly those retaining the crank case and cylinder head.
b) Replace the lubricating oil - see para 5.2.6.
5.2.2. Operation to be carried out daily:
a) drain condensation by opening the valve (fig.5.c) located under the tank.
5.2.3. Operations to be carried out monthly (or more frequently, if the compressor operates in a very dusty atmosphere):
a) check oil level and, if necessary, top-up.
b) Remove the air filter element (fig.7) by twisting of the filter end cover. clean the filter by blowing through from the clean side,
with an air line at low pressure. do not operate compressor without filter as foreign bodies or dust could damage the pump.
WARNING!
Wear safety goggles when performing this task.
c) check belt tension
d) check for oil leaks
5.2.4. Operation to be carried out 3-monthly:
a) check tank for internal corrosion.
5.2.5. Operations to be carried out every 500 hours:
a) change air filter element
b) check the automatic cut-out at max. pressure and the automatic cut-in at 2 bar below.
5.2.6. Operations to be carried out every 1000 hours:
a) Replace the lubricating oil. For oil specifications see 5.4.
Remove the oil breather (fig.6.A) and screw (fig.6.B), draining the oil into a container. drain
when the compressor is hot so that oil drains rapidly and completely.
Replace the screw and refill through the filler aperture. do not overfill. Replace the breather.
WARNING! Never mix different oils and do not use non-detergent/low quality oils as the
compressor may be damaged.
WARNING! Dispose of waste oil only in accordance with local authority requirements.
b) check belt tension. A weight of 3kg applied at the belt mid-point should give a deflection of approx. 10mm (fig.8). If
adjustment is required remember to maintain the alignment of the two pulleys (fig.8). Adjust by repositioning the engine,
using the screw adjuster provided in the base plate.
c) check all tube fittings and electrical connections.
d) Inspect pressure tank inside and out for damage or corrosion.
A
B
C
ALIGNMENT
fig. 8
fig. 5
fig. 6
Original Language Version
SA4050/55 Issue: 3 - 06/10/10