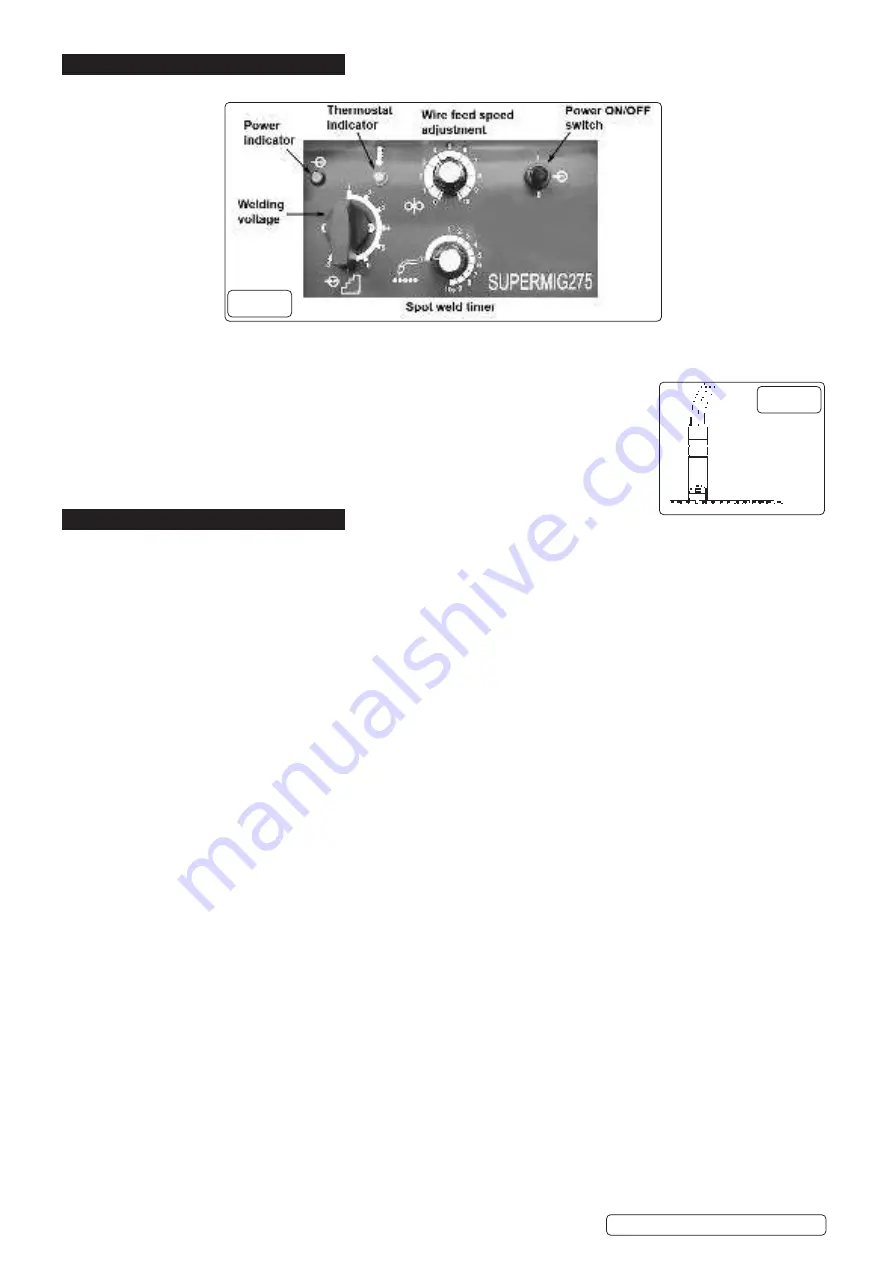
8. CONTROLS
8.1.
Fig 14 illustrates the main panel control for the Supermig 275.
8.2.
SYSTEM PROTECTION
A thermostat is built into the system to protect against overheating. The indicator light comes on when overheating occurs and cuts
off the power supply. It will reset automatically within a few minutes, after cooling down.
8.3.
SPOT WELDING
8.3.1.
Switch the welding set to the SPOT mode position.
8.3.2.
Remove the gas cup, see section 7.1.6 and replace it with the spot welding cap (fig.15).
8.3.3.
Set the voltage to highest setting (fig.14).
8.3.4.
Set the wire speed at almost maximum speed (fig.14).
8.3.5.
Turn ON the Spot Weld Timer to the desired time to suit thickness of plate being spot welded (fig.14).
8.3.6.
Press the torch button until the spot welding timer cuts in to stop the welding.
8.3.7.
Repeat as required.
9. MAINTENANCE
9.1.
WIRE FEED UNIT
9.1.1.
Check the wire feed unit at regular intervals. The feed roller wire guide plays an important part in obtaining consistent welding results.
Poor wire feed affects welding quality. Clean the rollers weekly removing all dust deposits.
9.2.
TORCH
9.2.1.
Protect the torch cable assembly from mechanical wear. Clean the liner from the machine forwards with compressed air. Replace the
liner if it becomes clogged.
9.3.
FEED ROLLER REPLACEMENT
9.3.1.
See section 7.4.
9.4.
CONTACT TIP
9.4.1.
The contact tip is a consumable item and must be replaced when the hole becomes enlarged or oval. The contact tip must be kept
free from spatter to ensure an unimpeded flow of gas.
9.5.
GAS CUP
9.5.1.
The gas cup must also be kept clean and free from spatter. Build up of spatter inside the gas cup can cause a short circuit at the
contact tip which will result in either the fuse blowing on the printed circuit card, or expensive machine repairs.
To keep the contact tip free from spatter, we recommend the use of Sealey anti-spatter spray (MIG/722307) available from your
Sealey stockist.
9.6.
REPLACING THE LINER
9.6.1.
Wind the wire back onto the spool and secure.
9.6.2.
Unscrew the torch from the welding set and undo the brass nut.
9.6.3.
The liner should now be visible.
9.6.4.
Pull the line out and replace with a new one.
fig.14
Supermig275.V2 Issue 1 10/01/22
Original Language Version
© Jack Sealey Limited
fig.15