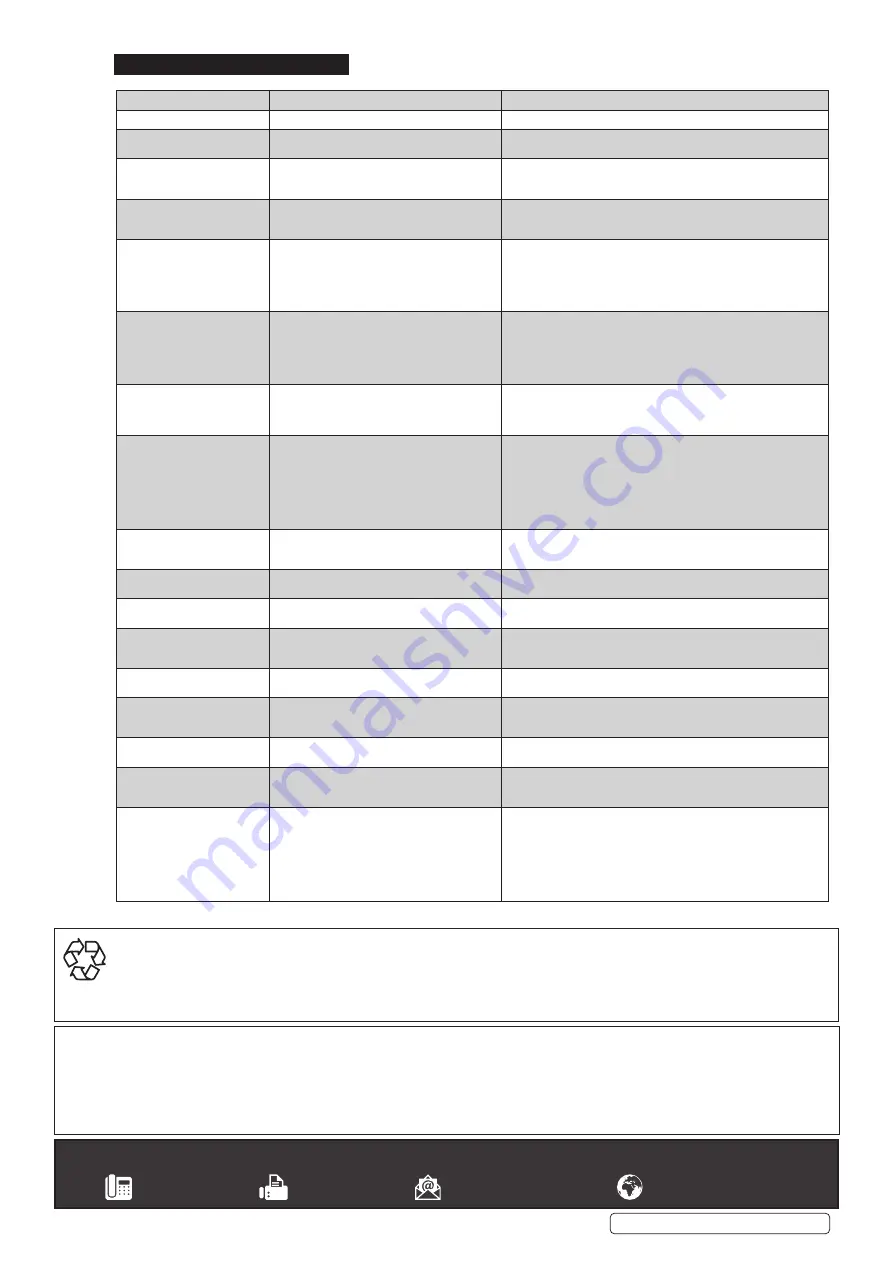
10. TROUBLESHOOTING
Supermig275.V2 Issue 1 10/01/22
Original Language Version
© Jack Sealey Limited
Sealey Group, Kempson Way, Suffolk Business Park, Bury St Edmunds, Suffolk. IP32 7AR
01284 757500
01284 703534
sales@sealey.co.uk
www.sealey.co.uk
ENVIRONMENT PROTECTION
Recycle unwanted materials instead of disposing of them as waste. All tools, accessories and packaging should be sorted, taken to
a recycling centre and disposed of in a manner which is compatible with the environment. When the product becomes completely
unserviceable and requires disposal, drain any fluids (if applicable) into approved containers and dispose of the product and fluids
according to local regulations.
Note
: It is our policy to continually improve products and as such we reserve the right to alter data, specifications and component parts without prior
notice. Please note that other versions of this product are available. If you require documentation for alternative versions, please email or call
our technical team on technical@sealey.co.uk or 01284 757505.
Important
: No Liability is accepted for incorrect use of this product.
Warranty
: Lifetime guarantee on Transformer - Comprises 1 year unconditional parts and labour on all parts, followed by a lifetime guarantee (parts
and labour) conditional on registering your purchase with us online at www.sealey.co.uk.
PROBLEM
POSSIBLE CAUSE
REMEDY
1. Power source stops
Overheating protection activated due to overload
Protection automatically resets when transformer has cooled (about 15 min)
2. No weld current
Rectifier blown
Replace rectifier
3. No weld current
Bad connection between clamp & workpiece
Break in earth lead
Break in torch lead
Clean or grind contact surface and weld area
Repair or replace earth lead
Repair or replace torch lead
4. Feed motor not working. Lamp
is on
Fuse blown
Gear damaged or worn
Motor defective
Replace fuse 1.5 amp
Contact service agent
Replace motor (Contact service agent)
5. Wire does not feed. Feed roller
rotates
Pressure roller improperly adjusted
Dirt, copper, dust, etc, have collected in torch liner
Gas cup (Nozzle) or tip defective. Faulty speed control
Deformed wire
Adjust tension
Clean the liner from the machine forward. Use compressed air. If too much
dirt, replace the liner
Replace gas cup (nozzle) and/or tip
Check roller tension and adjust it if necessary
6. Wire feeds unevenly
Dirt, etc, in liner
Gas cup (Nozzle) or Tip defective
Gas cup (Nozzle) spattered
Feed roller groove clogged
Feed roller groove deformed
Pressure roller tension improper
Clean the liner from the machine forward. Use compressed air
Replace gas cup (nozzle) and/or tip
Clean or replace gas cup (nozzle)
Clean feed roller
Replace feed roller
Adjust tension
7. Unstable arc
Incorrect settings
Impurities in weld area
Worn or defective gas cup (nozzle)
Check settings
Clean and/or grind workpiece
Replace gas cup (nozzle)
8. Porous weld
No gas
Gas cup clogged
Draft blowing away shielding gas
Rusty or dirty joints
Torch too far from or at wrong angle to work
Gas leak
Dirty Workpiece
Open gas cylinder, regulate gas flow
Clean or replace cup
Screen off welding site or increase gas flow
Clean or grind the workpiece
The distance from gas cup to workpiece should be 8-10mm
Check contact tip and nozzle
Check hoses, connections and torch assembly
Press the gas cup into correct position
9. Electrode sticking in gas cup
(nozzle)
Worn or defective gas cup (nozzle)
Electrode deformed
Wire speed too slow
Replace gas cup (nozzle)
Check roller tension
Adjust wire feed rate control
10.Irregular weld bead
Torch incorrectly held
Wire weaving in weld pool
Use correct torch angle
Check roller tension and adjust as needed
11.Weld bead too narrow and
raised
Weld current too high
Weld speed too low
Increase power and wire speed
Move torch slower and weave a little more
12. Weld bead too wide
Weld current too high
Weld speed too low
Arc too long
Decrease power and wire speed
Move torch faster and weave less
Bring torch closer to workpiece
13. Poor penetration
Weld current too high
Arc too long
Increase power and wire speed
Bring torch closer to workpiece
14. Excessive penetration
Weld current too high
weld speed too slow
incorrect distance of torch to workpiece
Decrease power and wire speed
Move torch faster
Torch distance should be 8-10mm
15. Fuse blowing
Tension too great
Gas cup contact tip clogged
Release tension
Clean gas cup and contact tip
16. Coils of wire on reel overlap, or
wire is oxidised. Coils break or fall
under wheel.
Tension to loose or tight. Coil damaged or wire
twisted.
Reset tension. Change wire reel
17. Wire runs through torch but
there is no welding current
Defective contactor.
Worn contacts of contactor regulator
Regulation switch problem
Faulty rectifier.
Fault on electronic circuit of contactor
Work cable not connected correctly.
Check coil ends, change coil if necessary.
Check, clean contacts, change if oxidation is present.
Check secondary voltage for each switch setting.
Disconnect rectifier from secondary, check each diode goes one way only.
If not change rectifier.
Change control module.
Connect work clamp directly to workpiece. Check wire is in good condition and
making good contact with clamp.