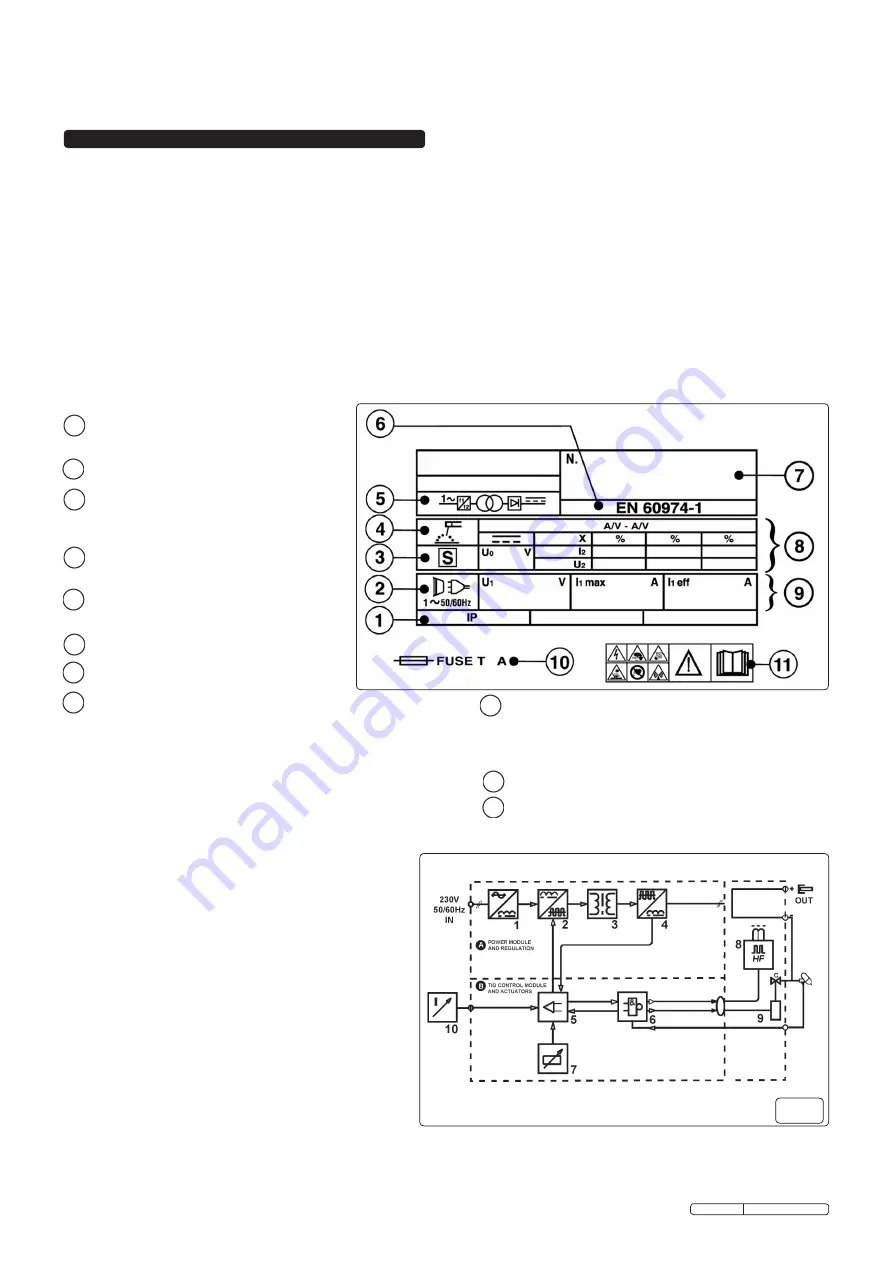
DO NOT
touch the workpiece close to the weld as it will be very hot. Allow to cool.
DO NOT
touch the torch immediately after use. Allow the torch to cool.
DO NOT
operate inverter when tired or under the influence of drugs, alcohol or intoxicating medication.
When not in use store the inverter in a safe, dry, childproof area.
2. DESCRIPTION & SPECIFICATION
2.2 GENERAL SPECIFICATION.
Power Output: . . . . . . . . . . . . . . . . . . . . . . . . . . . . . . . . . 5-160A
Duty Cycle:. . . . . . . . . . . . . . . . . . . . . . . . . . . . . . . .25% @ 160A
Electrode Capacity: . . . . . . . . . . . . . . . . . . . . . . . . Ø1.6 - 3.2mm
Power Absorbed: . . . . . . . . . . . . . . . . . . . . . . . . . . . . . . . . . .4kW
Mains Voltage: . . . . . . . . . . . . . . . . . . . . . . . . . . . . . . . .230V-1ph
Insulation Class:. . . . . . . . . . . . . . . . . . . . . . . . . . . . . . . . . . . . . H
Protection: . . . . . . . . . . . . . . . . . . . . . . . . . . . . . . . . . . . . . . . . . . . . . . . . IP23
Weight: . . . . . . . . . . . . . . . . . . . . . . . . . . . . . . . . . . . . . . . . . . . . . . . . . .6.8kg
TIG Accessories included. . . . . . . . . . . . . . . . . . . . . . . . . . . . . . . . . . . . . YES
ARC Accessory Ref (Optional). . . . . . . . . . . . . . . . . . . . . . . . . . . . INVMMA2
Foot Pedal Ref (Optional) . . . . . . . . . . . . . . . . . . . . . . . . . . . . . . . . INV/TIG/5
Current Control Ref (Optional) . . . . . . . . . . . . . . . . . . . . . . . . . . . . . INV/TIG/7
2.1
DESCRIPTION.
Fan-cooled DC power supply for TIG and MMA welding applications. Lightweight, compact unit with high quality technology, suitable for welding stainless
steel, steel, deoxidised copper, nickel and titanium. TIG cycle included current down-slope regulation. Features HF or lift striking. Includes connector for
foot pedal or hand controller for when more control is required. Supplied with shoulder strap.
2.3
EXPLANATION OF RATINGS PLATE SYMBOLS.
Detailed technical data relative to the performance of the machine is located on the underside of the base.
Please note
that the ratings plate shown below
is an example only intended to assist with the explanations of symbols. To determine the correct technical values of the machine in your possession, you
must refer to the machine data plate.
9
DATA REGARDING THE MAINS.
U1
:
Alternating current and power supply frequency of the
machine (allowed -10%).
I1max
: Maximum current absorbed by the line.
I1eff
:
Effective current supplied.
10
Size of delayed action fuses to be used to protect the power line.
11
Symbols refering to safety regulations.
1
Case protection grade: IP23. Standard governing the
required protection from water ingress and isolation
of internal parts from persons and objects.
2
Mains symbol : AC - single-phase supply.
3
Symbol S: Indicates that welding operations may be
carried out in areas with greater risk of electric shock
(e.g. close to metal masses).
4
Symbol of welding procedure chosen: Manual Arc
welding with stick electrode or welding with TIG.
5
Symbol of the main internal parts of the welder : i.e.
frequency converter (inverter) - transformer - rectifier.
6
The EUROPEAN standard relating to safety and the
construction of Arc welding machines.
7
Manufacturer’s identifying serial number.
8
PERFORMANCE OF THE WELDING CIRCUIT.
U
O
:
Maximum no-load peak voltage (welding circuit open).
12 / U2
:
Current and corresponding normalised voltage that may be supplied
from the machine during welding.
X
:
Duty cycle: Indicates the time during which machine can
supply the corresponding current (same column). This is expressed
as % on the basis of a 10min. cycle (e.g. 60% = 6 min of work, 4 min.
break and so on).
A/V-A/V
: Indicates the regulation range of the welding current (maximum -
minimum) at the corresponding arc voltage.
2.4. CIRCUIT SYSTEM DESCRIPTION (Refer to fig 1).
1.
Mains input (single phase), rectifier unit and condenser.
2.
Transistors and drivers switching bridge (IGBT). Turns the
mains rectified voltage into high frequency alternating
voltage (60khz) and permits power regulation according to
the current/voltage of the weld to be done.
3.
High frequency transformer: The primary windings are fed
by the voltage converted by Block 2. It has the function of
adapting voltage and current to values required by the ARC
welding procedure and, simultaneously, isolates the welding
circuit from the mains.
4.
Secondary rectifier bridge with inductance. Changes the
alternating voltage/current supplied by secondary windings
into continuous current/voltage at a low wave-length.
5.
Electronic and regulation board: Instantly checks the value
of the welding current against that selected by the user. It
modulates the commands of the IGBT drivers, which control
regulation.
6.
Control logic for welding machine operation: determines the
dynamic response of the current while the electrode melts
(instantaneous short circuits) and supervises the safety system
7.
Panel for setting parameters and operating modes.
8.
HF striking generator.
9. Protective gas electrovalve.
10. Remote regulation.
fig 1
Original Language Version
TIG160HF Issue: 1 - 31/10/11