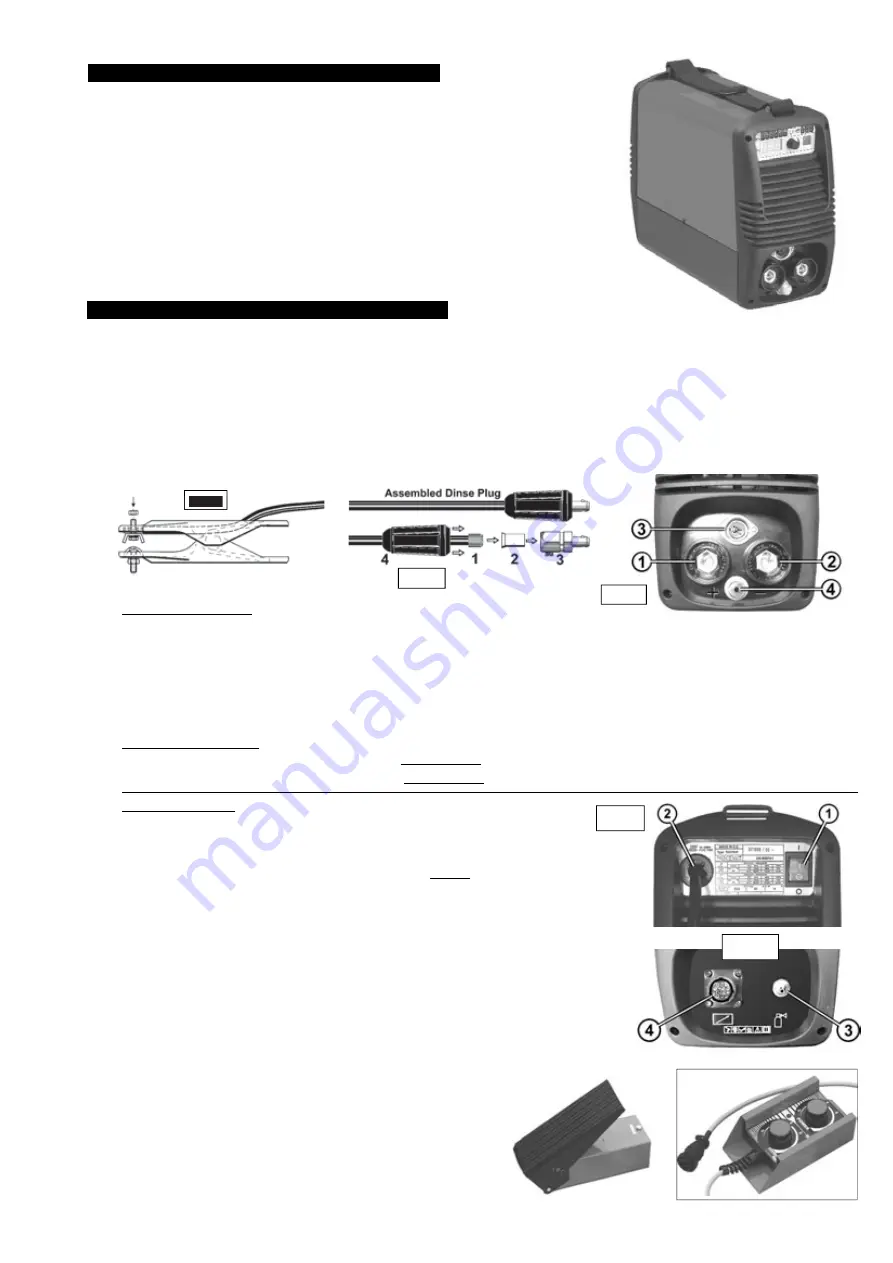
2.1
DESCRIPTION
Fan cooled AC/DC power supply suitable for TIG and ARC welding applications. Suitable for welding a wide
range of materials including steel, stainless steel, titanium, aluminium, copper, bronze and their alloys. LED
power read-out with push button programming in conjunction with an encoder knob.The unit features
regulation of post-gas and current down-slope time as well as control of AC balance and arc force. When TIG
welding the welding current can also be set to vary from one preset value to another using the torch button.
Includes burst HF start device and lift start feature which reduces HF emissions. Includes remote control
connector for foot pedal or hand controller.
2. DESCRIPTION & SPECIFICATIONS
2.2
SPECIFICATION
Power Output: . . . . . . . . . . . . . . . . . . . 5-160 A
Duty Cycle: . . . . . . . . . . . . . . . . . .60% @ 90 A
Electrode Capacity: . . . . . . . . . .Ø1.6 - 4.0 mm
Maximum absorbed power: . . . . . . . . . .4.5 KW
Mains Voltage: . . . . . . . . . . . . . . . . .230V -1ph
Insulation Class: . . . . . . . . . . . . . . . . . . . . . . .H
Protection: . . . . . . . . . . . . . . . . . . . . . . . . .IP23
Dimensions: . . . . . . . . . . .L430 x W170 x H340
Weight: . . . . . . . . . . . . . . . . . . . . . . . . .12.8 kg
TIG Accessory Ref: . . . . . . . . . . . . . .INV/TIG/3
ARC Accessory Ref: . . . . . . . (optional) INV/25
3.
PREPARING INVERTER FOR USE
3.1
CONNECTION TO MAINS:
3.1.1
Whilst welding at low power levels is possible on a 13amp supply the Inverter will normally be connected to a 30amp supply in order to TIG weld
at higher power levels and in order to perform ordinary ARC welding. See section 1, item 1.1.10
3.2
WELDING CABLE CONNECTION.
3.2.1 The torch cable is supplied ready assembled but it may be necessary for you to assemble the work clamp cable. Attach the work clamp to one end of the
cable as shown in fig.2. To connect the Dinse Plug as shown in fig.3 first thread the cable through the outer cover of the plug ( see fig.3 - 4 ). Now remove
20mm of insulation sheath from the end of the cable and fold back the copper wire all around the outside of the sheath ( 1 ). Push the cable end into the
copper sleeve ( 2 ) so that the folded back wire makes good contact with the inside of the sleeve. Push the copper sleeve into the brass plug body ( 3 ) and
tighten the large grub screw until the cable is firmly held. Now slide the outer plug cover up the cable and press the brass body into it as shown in fig.3.
3.2.3
TIG CONNECTIONS:
TIG TORCH CABLE.
Dinse plug at end of the torch cable will be connected to the
negative socket ( - )
on lower front panel ( see fig.4 item
2
).
3 pin torch plug at end of torch cable will be connected to circular 3 pin socket on the lower front panel. ( see fig.4 item
3
)
Black gas pipe with brass fitting at end of torch cable will be screwed to brass fitting on lower front panel. ( see fig.4 item
4
)
WORK CLAMP CABLE.
Dinse plug at end of the clamp cable will be connected to the
positive socket ( + )
on lower front panel ( see fig.4 item
1
).
3.2.4
( * ) Please note that the way the welding cables are connected to the inverter for ordinary ARC welding may be different to the way the cables are
connected for standard TIG welding. Whilst most stick electrodes are connected to the positive terminal certain types need to be connected to the
negative terminal. It is therefore essential that the user refers to the manufacturers instructions for the electrodes to ensure that the correct
polarity is selected.
3.2.5
ARC CONNECTIONS:
( You will need optional ARC Accessory Kit INV/25 )
ELECTRODE HOLDER
Plug at the end of electrode cable
will normally (* )
be connected to the
positive socket ( + )
on the front panel (see fig.4 item
1
).
WORK CLAMP CABLE.
Plug at the end of the clamp cable
will normally (* )
be connected to the
negative socket ( - )
on the front panel (see fig.4 item
2
).
Fig 2
Fig 3
Fig 4
fig 5
3.3
REAR PANEL LAYOUT (refer to Figs 5 & 5A).
1. ON/OFF SWITCH
: O = Off, I = On.
2. MAINS CABLE
3. GAS INLET FITTING.
For connecting the gas cylinder to the welder using clear tubing provided.
4. REMOTE CONTROL CONNECTOR.
For the connection of the
optional
remote controls shown below.
3.4
REMOTE CONTROLS ( Optional.)
Two types of remote control can be connected to the machine via the
14 pin connector situated on the back panel (See fig.5a-4). The device will be automatically recognised.
The encoder knob on the main control panel will become inoperative for those functions taken over by the
remote control.
3.4.1
Remote control pedal
.
(Model No. INV/TIG/5)
When activated the pedal will control the main welding
current. Also in 2 step TIG welding mode the first movement of the pedal will initiate the striking of the arc in
place of the torch button.
3.4.2
Remote control with two potentiometers. (Model No. INV/TIG/7)
The knob furthest away from the cable
entry, controls the main welding current. The second knob will control one other parameter depending on the
active welding mode. ( See table below.) The rotation of the second knob automatically selects the
appropriate parameter and brings it up on the display.
3.4.3
Welding mode set up.
Parameter for second Knob.
ARC welding with stick electrode . . . . . . . . . . . . . .Arc force. ( Not displayed )
TIG DC, HF or LIFT, 2 or 4 steps, . . . . . . . . . . . . . . . . . . . . . . . . . . .Post Gas
TIG AC , 2 or 4 steps . . . . . . . . . . . . . . . . . . . . . . . . . . . . . . . . . . . .Post Gas
TIG175HF - 1 - 061003
fig 5a