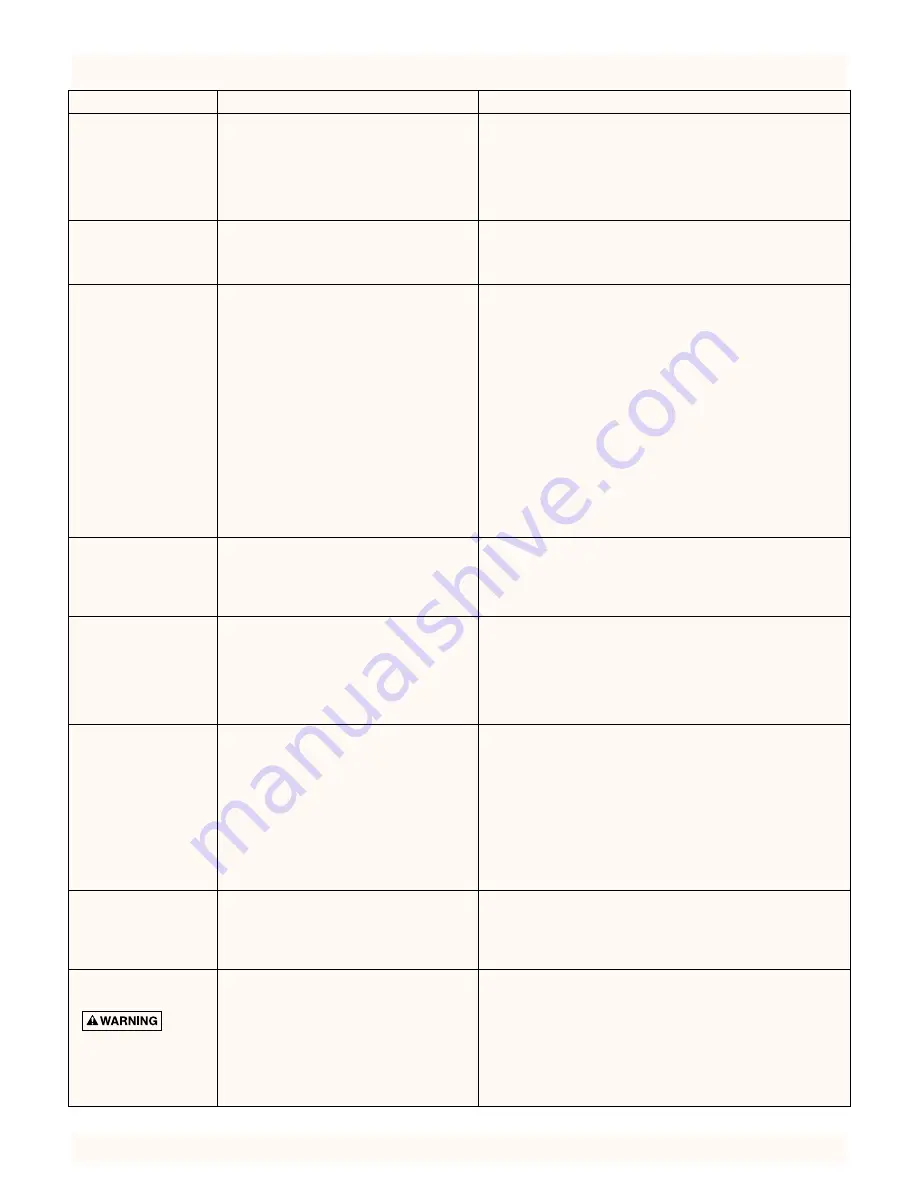
TROUBLESHOOTING GUIDE
11
TROUBLE
POSSIBLE CAUSES
REMEDIES
Motor will not run
1. Disconnect switch is off
1. Be sure switch is on
2. Fuse is blown
2. Replace fuse
3. Starting switch is defective
3. Replace starting switch
4. Wires at motor are loose,
4. Refer to instructions on wiring
disconnected, or wired incorrectly
*5. Motor is wired incorrectly
5. Refer to instructions on wiring
6. Pressure switch contacts are dirty
6. Clean by sliding piece of plain paper between contacts
Motor runs hot and
*1. Motor is wired incorrectly
1. Refer to instructions on wiring
overload kicks off
2. Voltage is too low
2. Check with power company. Install heavier wiring
if wire size is too small. See wiring instructions
3. Pump cycles too frequently
3. See section below on too frequent cycling
Motor runs but no
*1. Pump in a new installation did
1. In new installation:
water is delivered
not pick up prime through:
a. Improper priming
a. Re-prime according to instructions
b. Air leaks
b. Check all connections on suction line and jet
c. Leaking foot valve
c. Replace foot valve
*2. Pump has lost its prime through:
2. In installation already in use:
a. Air leaks
a. Check all connections on suction line, jet and shaft seal
b. Water level below suction of pump
b. Lower suction line into water and re-prime. If receding
water level in a shallow well operation exceeds
suction lift, a deep well pump is needed
3. Jet or impeller is plugged
3. Clean jet or impeller according to instructions
4. Check valve or foot valve is stuck
4. Replace check valve or foot valve
in closed position
5. Pipes are frozen
5. Thaw pipes. Bury pipes below frost line. Heat pit or
pump house
6. Foot valve and/or strainer are
6. Raise foot valve and/or strainer above well bottom
buried in sand or mud
Pump does not
1. Water level in well is lower than
1. A deep well jet pump may be needed (over 20 ft. to water)
deliver water to full
estimated
capacity (also check
2. Steel piping (if used) is corroded or
2. Replace with Plastic Pipe where possible, otherwise with
point 3 immediately
limed, causing excess friction
new steel pipe
above)
3. Offset piping is too small in size
3. Use larger offset piping
Pump pumps water
1. Pressure switch is out of adjustment
1. Adjust or replace pressure switch
but does not shut off
or contacts are “frozen”
2. Faucets have been left open
2. Close faucets
3. Jet or impeller is clogged
3. Clean jet or impeller
*4. Motor is wired incorrectly
4. Refer to instructions on wiring
5. Water level in well is lower than
5. Check possibility of using a deep well jet pump
estimated
Pump cycles too
1. Pipes leak
1. Check connections, replace pipe fittings
frequently
2. Faucets or valves are open
2. Close faucets or valves
3. Foot valve leaks
3. Replace foot valve
4. Pressure switch is out of adjustment
4. Adjust or replace pressure switch
5. Air charge too low in SEARS
5. Disconnect electrical power and open faucets until all
Captive Air® Tank
pressure is relieved. Using automobile tire pressure
gauge, check air pressure in tank at the valve stem
located at top of tank. If less than 20 pounds, pump air
into tank from outside source, until 20 pounds pressure
is reached. Check air valve for leaks, using soapy
solution, and replace core if necessary
Air spurts from
1. Pump is picking up prime
1. As soon as pump picks up prime, all air will be ejected
faucets
2. Leak in suction side of pump
2. Check suction piping, make sure joints are not sucking air
3. Well is gaseous
3. Change installation as described in manual
4. Intermittent over-pumping of well
4. Lower foot valve if possible, otherwise restrict discharge
side of pump
Leaks at the metal
1. Loose clamps or “O” ring
1. First check the clamp tightening screw to see if it is tight.
clamps
not sealed
If it is tight and slight leakage still occurs, place a piece
of wood on the periphery of the clamp and firmly tap the
wood with a hammer. Repeat this operation around the
edge of the clamp and retighten the clamp screw. If leak
continues, disassemble clamp and pump halves and
check to see that “O” ring is properly seated and no
foreign material is on “O” ring or “O” seat.
Reassemble pump.
(*Note: Check prime
before looking for
other causes.
Unscrew priming plug
and see if there is
water in priming hole)
Release all pressure
in system before
working on clamp!