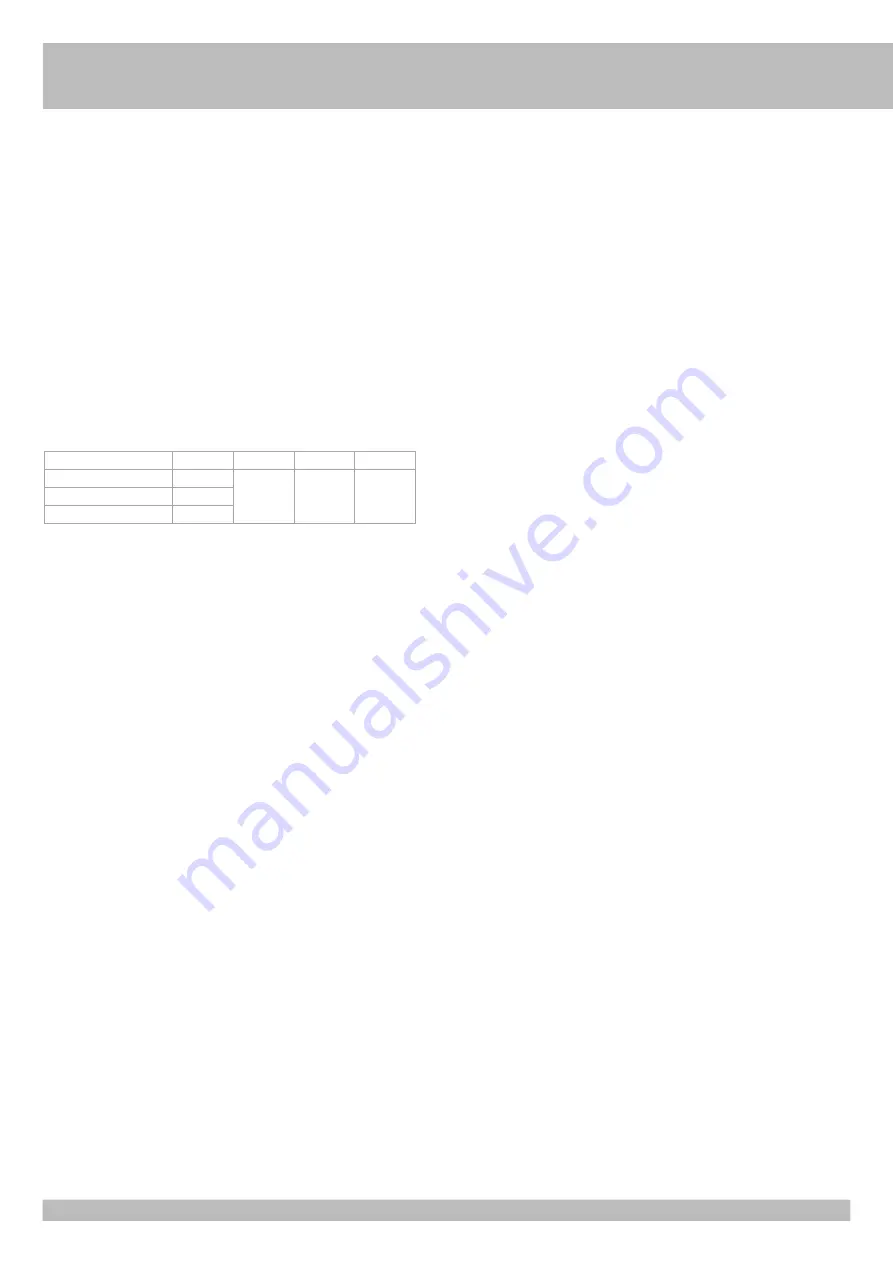
49
POINT B - SETTINGS
DIP 1
(ON) MOTORS ROTATION DIRECTION CHECK (See Point C
)
Dip 2 (ON) - setting the times (point D)
Dip 2-1
setting the pedestrian opening times (point E)
Dip 1-2
save/delete
radio control codes for total opening (point F)
Dip 1-3
save/delete
radio codes for pedestrian opening (point G)
Dip 1-2-3
save/delete
radio codes for relay r-aux command (point H)
DIP SWITCHES CONTROL
DIP 4
Photocells always active (OFF) - Photocells active only during closing (ON)
DIP 5
Pre-blinking (ON) - Normal blinking (OFF)
DIP 6
Single pulse command (START) and RADIO - step-by-step (ON) - automatic (OFF)
DIP 7
Photocells AUTO-TEST activation (ON-activated).
DIP 8
Electric lock activation (ON-activated)
DIP 9
Electric lock pulse release (ON-activated)
DIP 10
Motors manual release facilitation (ON-activated)
DIP 11
Electric lock pulse engagement (ON-activated)
DIP 12
Selection of 1 or 2 motor operation (default OFF 2 motors)
DIP 13
Activate the radio system SUN/MOON (ON) - SUN-PRO (OFF)
DIP 14 Timed operation (OFF) - Operation with limit switches (ON)
DIP 15 Slowdown (ON - activated)
DIP 16 Contactors management (ON - activated)
DIP 17 Encoder management (ON - activated)
TYPE OF MOTOR
CODE
DIP 18
DIP 19
DIP 20
IDRO C 1/27B
AA10884
ON
ON
ON
IDRO C 2/27B
AA10882
IDRO C 27/R
AA10883
TORQUE TRIMMER - Electronic regulator for motor torque
Adjustment of motor torque is carried out using the TORQUE Trimmer which varies the output
voltage to the head/s of the motor/s (turn clockwise to increase torque).
This torque control is activated after 2 seconds form any manoeuvre begging, whereas the
motor is turned on at full power to guarantee the starting at the manoeuvre begging.
PAY ATTENTION: IF THE TORQUE TRIMMER SETTING IS CHANGED, IT IS PREFERABLE
TO REPEAT THE TIME PROGRAMMING.
LOW SPEED TRIMMER - Electronic regulator for low speed on approach
Adjustment of low speed is carried out using the LOW SPEED Trimmer which varies the
output voltage to the head/s of the motor/s (turn clockwise to increase speed). Adjustment
is carried out to establish the correct speed at the completion of opening and closing,
depending on the structure of the gate, or if there is any light friction that could compromise
the correct working of the system. The low speed is activated (DIP 15 ON) when the gate leaf
is 0.50-0.60 meters away from the complete close or open position.
ATTENTION: WHEN USING HYDRAULIC OPERATORS
When using the hydraulic operators the deceleration phase may not operate correctly;
in that case it is advisable to disable the feature of the deceleration by putting DIP
15 in the OFF mode.
TCA TRIMMER - AUTOMATIC CLOSING pause time regulator for TOTAL or PEDESTRIAN
openings
normally NOT ACTIVATED and LED DL11 OFF
(trimmer fully rotated counterclockwise)
This trimmer makes it possible to adjust the pause time for total or pedestrian automatic
closing. Only with gate completely open (total) or partially open (pedestrian) and LED DL11
ON (trimmer rotated clockwise to activate the feauture).
The pause time (for a totally opened gate) can be adjusted from a minimum of 2 s up to a
maximum of 2 minutes.
The pause time (for gate open with PED. control) can be adjusted from a minimum of 2
seconds to a maximum of 30 seconds.
Ex: With TCA trimmer setted halfway, you will have 1 minute pause after the total opening and
15 seconds of pause after the pedestrian opening prior to have the auto-close of the gate.
R-AUX - AUXILIARY RELAY CONTACT (NO)
By default this relay is set as courtesy light (max 700 W - 3 A - 230 Vac) to operate 3 minutes
at each command, with time renewed at each command.
You can activate the R-AUX contact by TRANSMITTER by performing the memorization
procedure described in point H.
LED WARNING
DL1 PROG programming activated
(red)
DL2 M1 - gate opening
(green)
DL3 M1 - gate closing
(red)
DL4 M2 - gate opening
(green)
DL5 M2 - gate closing
(red)
DL6 STOP command (NC)
(red)
DL7 PHOTO 1 contact (NC)
(red)
DL8 PHOTO 2 contact (NC)
(red)
DL9 EDGE 1 contact (NC)
(red)
DL10 EDGE 2 contact (NC)
(red)
DL11 TCA - automatic closure time enabled
(red)
DL12 Remotes programming enabled
(two colors)
DL13 Card managed by APP
(blue)
DL14 Opening limit switch LSO M1/ENC
(red)
DL15 Closing limit switch LSC M1
(red)
DL16 Opening limit switch LSO M2/ENC
(red)
DL17 Closing limit switch LSC M2
(red)
DL18 PROG and RADIO (on MOLEX connector) commands (green)
B.I.O Clock command (NO)
(green)
PED. Pedestrian command (NO)
(green)
START Single impulse command (NO)
(green)
CLOSE CLOSE command (NO)
(green)
OPEN OPEN command (NO)
(green)
C - MOTOR/S ROTATIONAL DIRECTION CONTROL
1 - Unlock the operators with the Manual Release - swing open the leaves about halfway
and lock again the operators.
2 - Turn DIP1 to ON position The red LED DL1 starts blinking.
3 - Press the PROG button and hold it - When GREEN LEDS DL2 and DL4 are on, the gate
leaves are opening (with a phase shift of 2 seconds). Check the leaves swinging and the
opening mechanical stopper position (movement is now performed in “man present”
mode, open-close-open-etc.).
If any of the leaf closes instead of opening, release PROG button, turn off the main power
and reverse the two phase wires (V1/2 and W1/2) of the relevant motor/s.
4 - Press the PROG button and hold it to CLOSE completely the gate. When RED LEDS DL5
and DL3 are on, the gate leaves are closing (with a phase shift of 2 seconds). Check
leaves swinging and the closing mechanical stopper position.
5 - After 2 seconds motor starting and for the next 10 seconds motor working, the torque
controls automatically activated. Set the motor torque by the TORQUE Trimmer/s which
varies the output voltage to the motor/s (turn clockwise to increase the torque).
6 - After other 10 seconds motor working, the low speed controls automatically activated
(DIP 15 ON). Set the motor low speed by the LOW SPEED Trimmer to select the gate leaf
low speed in approaching.
7 - Close completely the gate.
8 - Turn DIP1 to OFF position, LED DL1 turns off.
During Point C procedure, safety devices (photocells and safetystrip) are not active.
D - TIMES PROGRAMMING
N.B.: DURING PROGRAMMING THE SAFETY DEVICES ARE ACTIVE AND THEIR
INTERVENTION STOPS PROGRAMMING (THE DL1 LED FROM FLASHING
REMAINS ON FIXED) AND THE BUZZER PLAYS FOR 10 SECONDS. TO REPEAT
THE PROGRAMMING PROCEDURE POSITION THE DIP 1 AND DIP 2 TO OFF,
CLOSE THE GATE THROUGH PROCEDURE «CHECKING THE DIRECTION OF
MOTOR ROTATION» AND REPEAT THE PROGRAMMING OF THE CHOICE.
N.B.:
The deceleration is automatically determined during the times programming, and is
activated about 50÷60 cm before the end of opening or end of closing.
- FOR 2 MOTORS - DIP 12 OFF
1 - The gate must be completely closed.
2 - Set DIP 2 to ON => LED DL1 will flash briefly.
3 - Press the PROG./RADIO/OPEN/START button => M1 opens.
4 - Reached the mechanical stopper in opening => after 1 second press the PROG./RADIO/
OPEN/START button to stop M1 and open M2.
5 - When the mechanical opening stopper has been reached => after 1 second press the
PROG./RADIO/OPEN/START button => M2 stops.
6 - Press the PROG./RADIO/OPEN/START button => M2 closes.
7 - After a few seconds press the PROG./RADIO/OPEN/START button => M1 closes and
determine the phase displacement between M2 and M1.
At the same time the LED DL1 will stop flashing, signaling the exit from the programming
procedure.
From this moment the safety devices or other gate commands will work normally (inversions,
stops, alarms, etc.).
8 - When the time is over, the gate stops.
9 - AT THE END OF PROGRAMMING, RESET THE DIP 2 IN OFF POSITION.
G
B
Summary of Contents for IDRO C 27/1B
Page 74: ...74 ...