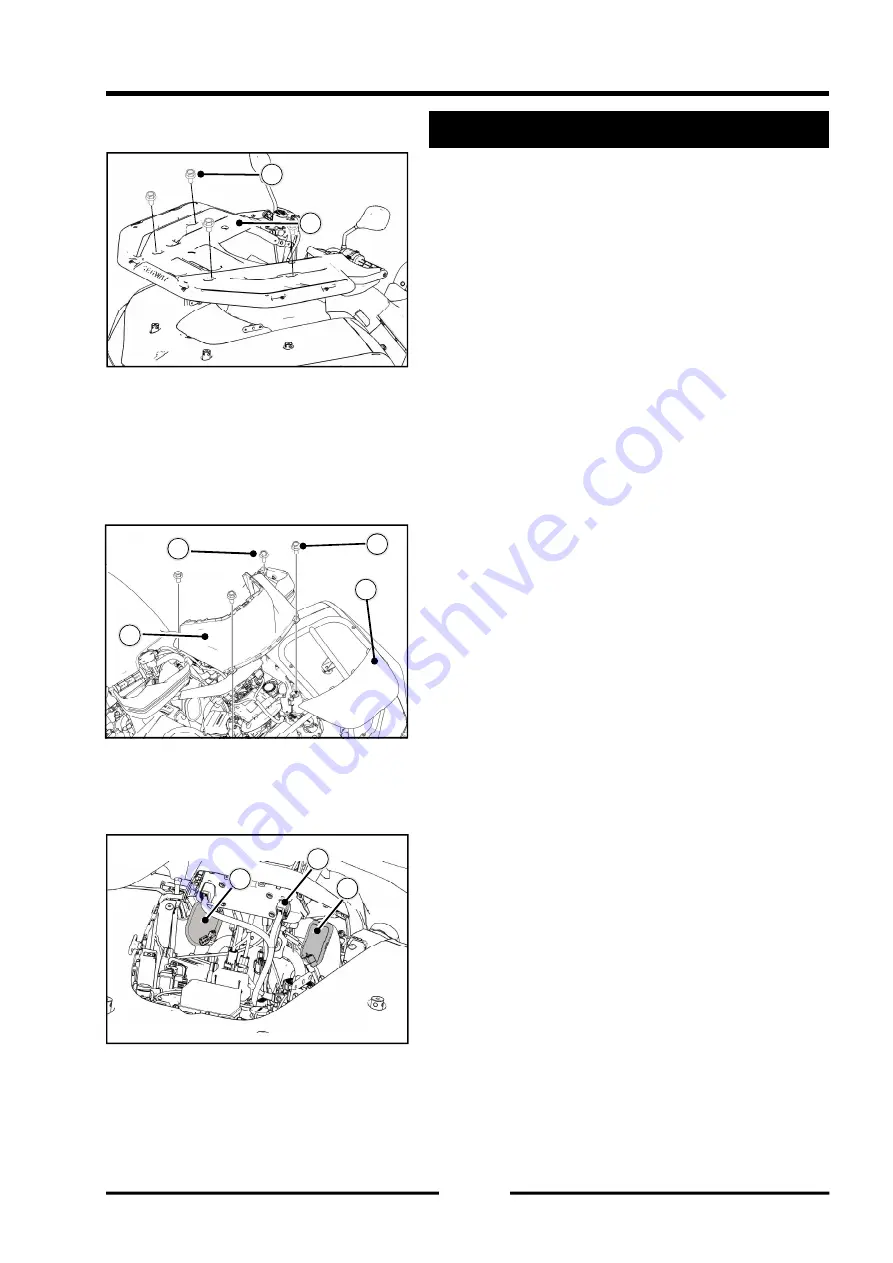
INTAKE / EXHAUST SYSTEM
7 -
3
Disassemble Air Filter
C
D
E
F
【
C
】
maintenance cover
【
D
】
bolt
【
E
】
bolt
【
F
】
Instrument cover assembly
◆
remove maintenance cover
【
C
】
◆
take down bolt
【
D
】
and
【
F
】;
◆
Remove the instrument cover assembly
【
F
】;
【
G
】
Instrument connector
【
H
】
Air fi lter air inlet screen
【
I
】
CVT intake strainer
◆
Unplug the instrument connector
【
G
】
◆
Remove the CVT intake strainer
【
I
】
Air inlet
screen for air fi lter
【
H
】;
G
H
I
A
B
Place the vehicle body in a horizontal position fi rst
【
A
】
bolt
【
B
】
Front rack assembly
◆
Remove the bolts
◆
Remove the front rack assembly as a whole from the
body
Summary of Contents for SNARLER ATV 2021 Series
Page 1: ...SERVICE MANUAL ATV SERIES PRODUCTS 20210804 V01...
Page 39: ...ENGINE LUBRICATION SYSTEM ENGINE LUBRICATION SYSTEM 3 1 2 Exploded view...
Page 99: ...ENGINE COOLING SYSTEM ENGINE COOLING SYSTEM 3 4 2 Exploded view...
Page 120: ...ENGINE TOP END ENGINE TOP END 3 5 10 Spark Plug Valve Cover Throttle Body Camshaft...
Page 153: ...CVT SYSTEM CVT SYSTEM 3 6 2 L L G G G G R R Lh Lh R R R R Exploded view...
Page 155: ...CVT SYSTEM CVT SYSTEM 3 6 4 R R R R G G R R L L Lh Lh M M G G G G G G...
Page 185: ...4 13 FRONT AND REAR DIFFERENTIAL FRONT AND REAR DIFFERENTIAL...
Page 212: ...COOLING SYSTEM 6 6 Special tools and sealants Silicone Sealant...
Page 230: ...FRONT REAR SUSPENSION 9 2 Exploded view of Front suspension...
Page 232: ...FRONT REAR SUSPENSION 9 4 Exploded view of Rear suspension...
Page 249: ...WHEELS AND TIRES 10 5 Special Tools Jack...
Page 264: ...BRAKE SYSTEM 11 5 Inside Circlip Pliers Special tool...
Page 276: ...STEERING SYSTEM 12 2 Exploded View of Steering System 1 2 A A 3 4 5 5 5 6 3 B...
Page 323: ...ELECTRICAL SYSTEM 14 15 EFI system Schematic diagram of EFI system...
Page 383: ...ELECTRICAL SYSTEM 14 75 B10 B11 B12 B14 B15 B16...