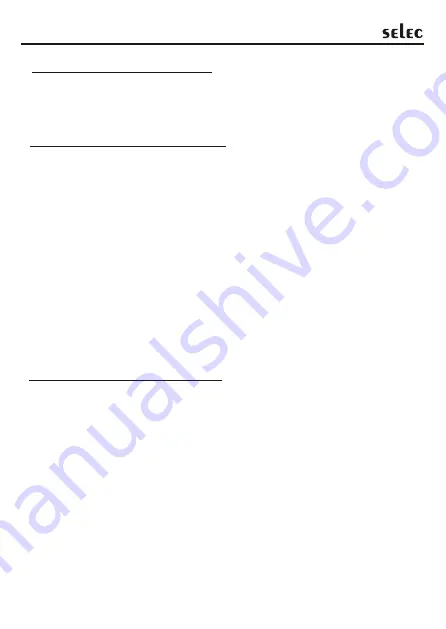
For most applications, set this parameter to 0.0 prior to starting Autotune. After the
completion of Autotune, this parameter may need to be reset. It is important that external
load disturbances be minimized, and if present, other zone controllers idled as these may
have an effect on the PID constant determination.
2. The output is scaled by use of Analog low and high scaling points in level 2 of the
output to an external device.
1. The analog retransmission output feature allows the retransmission of the control
!
AUTO-TUNE OF HEAT/COOL SYSTEMS:
!
DERIVATIVE APPROACH CONTROL:
4. Note that the main output selection in level 4 has to be relay 2.
Derivative approach control (DAC) helps in reducing overshoot at startup. The control
output cutoff point is derived as DAC x Proportional band. Note that the DAC value is
automatically calculated and fed after autotuning (if tuning is initiated at startup).
During Autotune of heat/cool systems, the controller switches the cooling output (O2) ON
and OFF in addition to the heat output (O1). The heat/cool overlap deadband parameter
(db in Level 2) determines the amount of overlap or deadband between the two outputs
during Autotune.
Some water cooled processes exhibit an extreme non-linear gain characteristic. That is,
the process cooling gain starts very high and flattens out deeper into the cooling region.
This effect may result in regular oscillations at setpoint as the controller applies heat to
counteract the effect. These processes may benefit from a lower cooling fan setting
and/or reduced water flow in the jacket or manifold. The process heat and cool gains
should be balanced as much as possible, and the controller gains adjusted to the
process.
programming menu. The analog output will be proportional to PV (derived from
3. A-LO : Displays the value that corresponds to 0V, 0/4mA as selected.
Analog Low and High scaling.)
!
ANALOG OUTPUT-RETRANSMISSION:
A-HI : Displays the value that corresponds to 10V or
20mA as selected.
35
User Guide