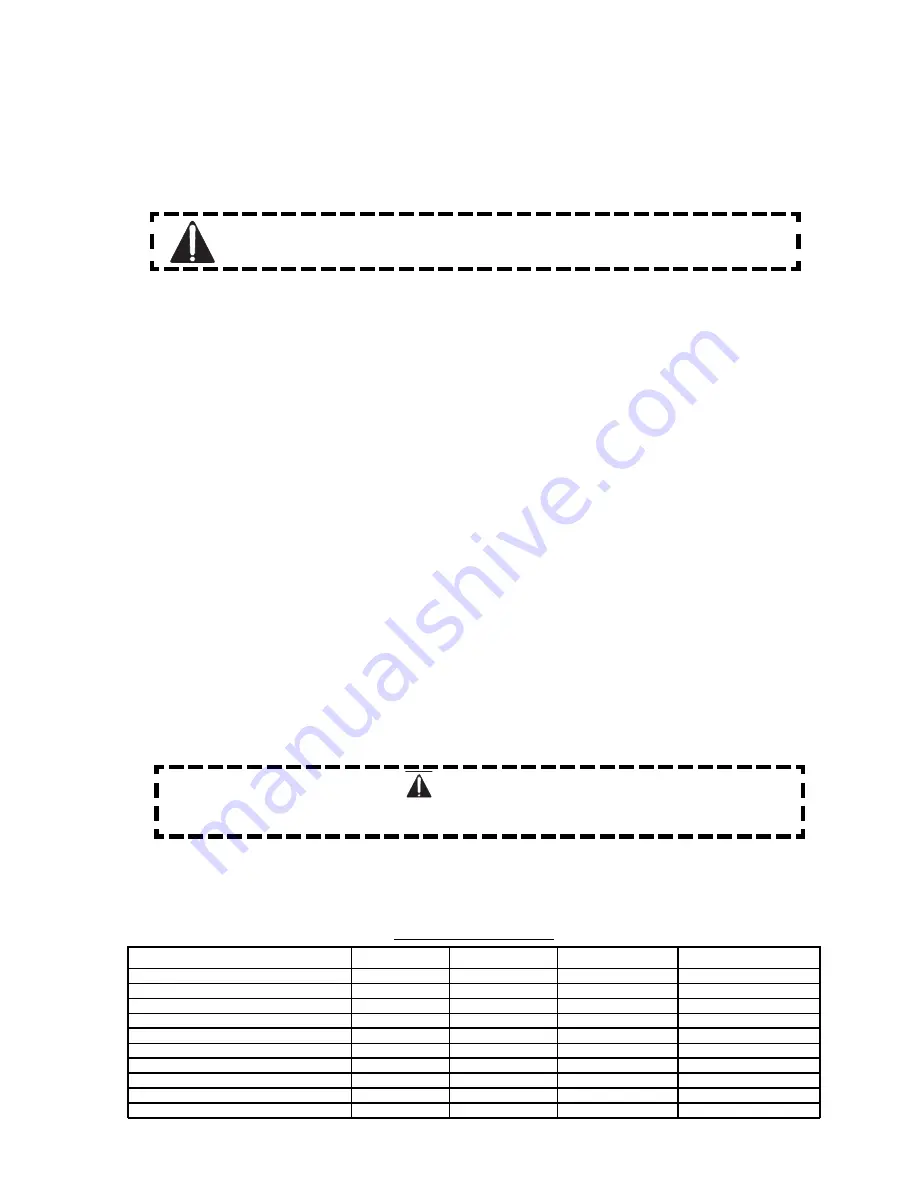
11
OPERATION
PRE-START CHECKLIST:
1. Check oil level. Add if necessary.
2. Remove any moisture in the air compressor air tank. Remove excessive pressure with an air tool, then open
the air tank drain valve in the bottom of the air tank. Close tightly when drained.
WARNING: Risk of bodily injury. NEVER attempt to open the drain valve when
more than 10 PSI of air pressure is in the air tank!
3. Make sure the air compressor Motor Switch is in the “OFF” position.
4. Make sure all safety valves are working correctly.
5. Make sure all guards and covers are in place and securely mounted.
START-UP:
1. Ensure the lever on the pressure switch box is in the “OFF” position.
2. Plug the power cord into a grounded outlet.
3. Move the lever on the pressure switch box to the “AUTO” position.
4. START/STOP OPTION: Turn it completely clockwise to the fully closed position. This will allow the air compressor
to “START” building up pressure in the air tanks and “STOP” when correct pressure is achieved. When pressure
drops with usage, the air compressor will “START” building up pressure again.
CONSTANT RUN OPTION: Locate the adjustment knob at the top of the pilot valve. Turn it completely
counterclockwise to the fully open position. The air compressor is now set up to “CONSTANTLY” build up
pressure. When pressure reaches the preset level in the air tank, pressure will bleed through the pilot valve.
5. Set pressure by adjusting the pressure regulator knob counterclockwise for less pressure and clockwise for
more pressure.
6. If you notice any unusual noise or vibration, stop the air compressor and refer to “Troubleshooting”.
SHUTDOWN:
1. To stop the air compressor, move the lever on the pressure switch box to the “OFF” position. NEVER stop the
air compressor by unplugging it from the power source. This could result in risk of electrocution.
2. Drain air from the air tanks by releasing air with an attached air tool or by pulling on the safety relief valve rings.
3. Once pressure in the air tanks register under 10 pounds, open the drain valve under each air tank to drain any
moisture.
4. Allow the air compressor to cool down.
5. Wipe air compressor clean and store in a safe, non-freezing area.
MAINTENANCE
Read the instruction manual before performing maintenance. The following procedures must be performed when
stopping the air compressor for maintenance or service.
1. Turn off air compressor.
WARNING: Never assume the air compressor is safe to work on just because it is not
operating. It could restart at any time!
2. Disconnect cord from main power supply.
3. Open all drains.
4. Wait for the air compressor to cool before starting service.
MAINTENANCE CHART
PROCEDURE
DAILY
WEEKLY
MONTHLY
200 HOURS
Check pump oil level
X
Oil leak inspection
X
Drain condensation in air tank(s)
X
Check for unusual noise/vibration
X
Check for air leaks
X
Inspect air filter
X
Clean exterior of compressor
X
Check safety relief valve
X
Change pump oil*
X
Replace air filter
X
*The pump oil must be changed after the first 50 hours of operation and every 200 hours or 3 months, whichever
comes first. Recommended non-detergent straight weights.