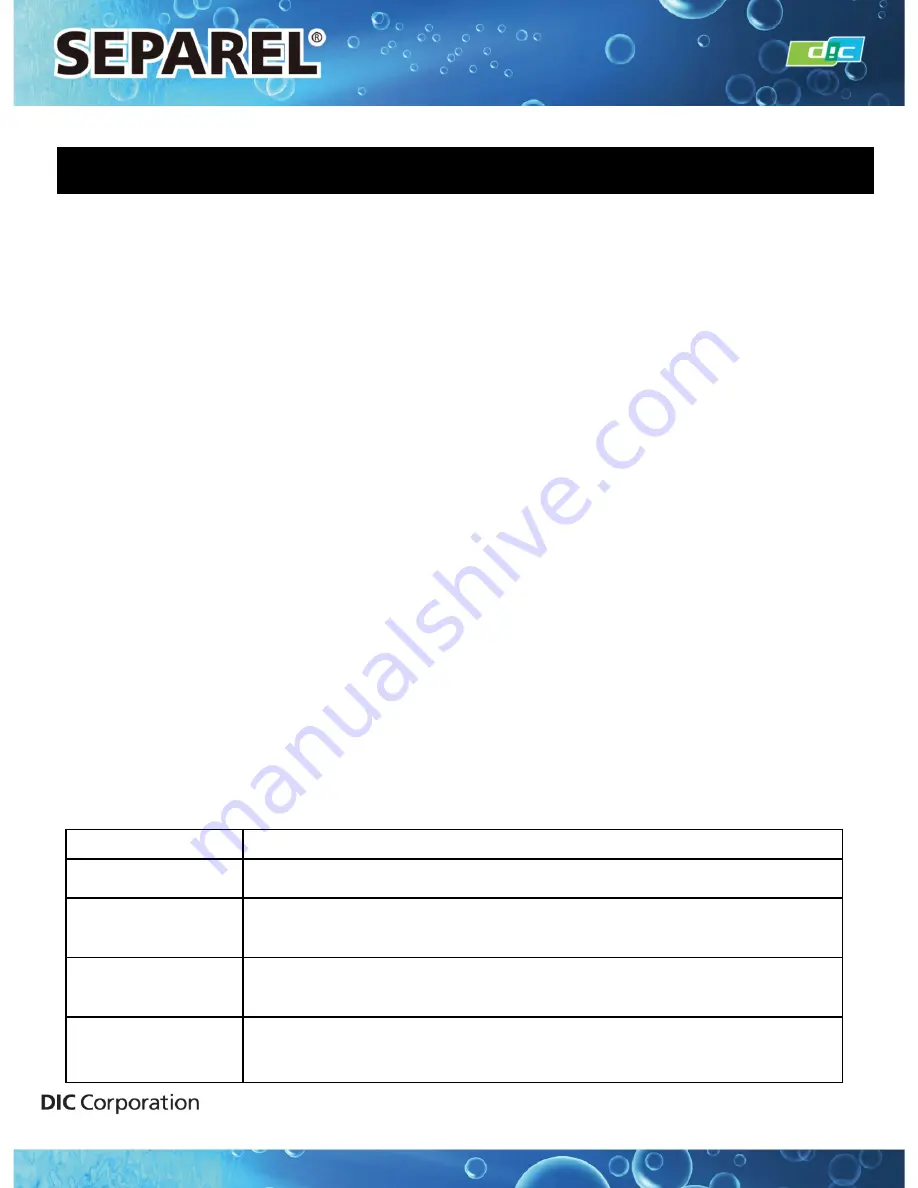
4. START UP
10
10
4-1. Open a valve on the outlet side first. Next, open a valve on the inlet side gradually to
make the liquid flow rate and pressure lower than the designated value for actual use
until liquid is filled. Do not flow liquid at a very high flow rate nor at a very high pressure.
Even if it is instantaneous, very high flow rates or pressure may damage hollow fibers
and cause leakage. For efficient removal of remaining air in the liquid area of
SEPAREL modules, filling the liquid with a vacuum is recommended. During the
vacuuming process, check the airtightness of the vacuum line and not the air that
is leaked from pipe, connector, and SEPAREL module.
4-2. Observe liquid quality, temperature, and pressure specified in the specification sheet.
4-3. Do not flow oxidizing agents, such as highly concentrated chlorine water and ozone
water, strong acids, strong bases, organic solvents, oil, or any other liquid which has
not been confirmed as compatible by DIC. The warranty will not apply if liquid, which
has not been confirmed as compatible by DIC, is used.
4-4. Do not change the flow rate dramatically in order to ensure that the hollow fibers are
not damaged by drastic pressure fluctuations.
4-5. If vacuum pressure is very strong, and conditions are close to a perfect vacuum
situation, stop the vacuum pump when liquid flow has stopped. Strong vacuuming for
an extended period of time without liquid flow may freeze and damage hollow fibers via
vaporization heat and liquid may leak from the damaged hollow fibers.
4-6. Check the items below periodically. If obvious deterioration is found, replace with a
new degassing module .
Item
Points to be Checked
Liquid Inlet Pressure
Do not exceed maximum pressure specified in the specification sheet.
Liquid Temperature
・
Do not exceed the maximum temperature specified in the specification sheet.
・
Do not fall below the minimum temperature specified in the specification sheet.
Pressure Drop
Significant increase from initial value may be caused by clogging of hollow fiber
or liquid flow path. In this case, replacement or cleaning is necessary.
Drain/Trap
in Vacuum Line
Continuous leaking of liquid to the vacuum means the product is reaching the
end of its lifetime and replacement with a new degassing module is necessary.
Application Materials Product Division
INSTRUCTION MANUAL