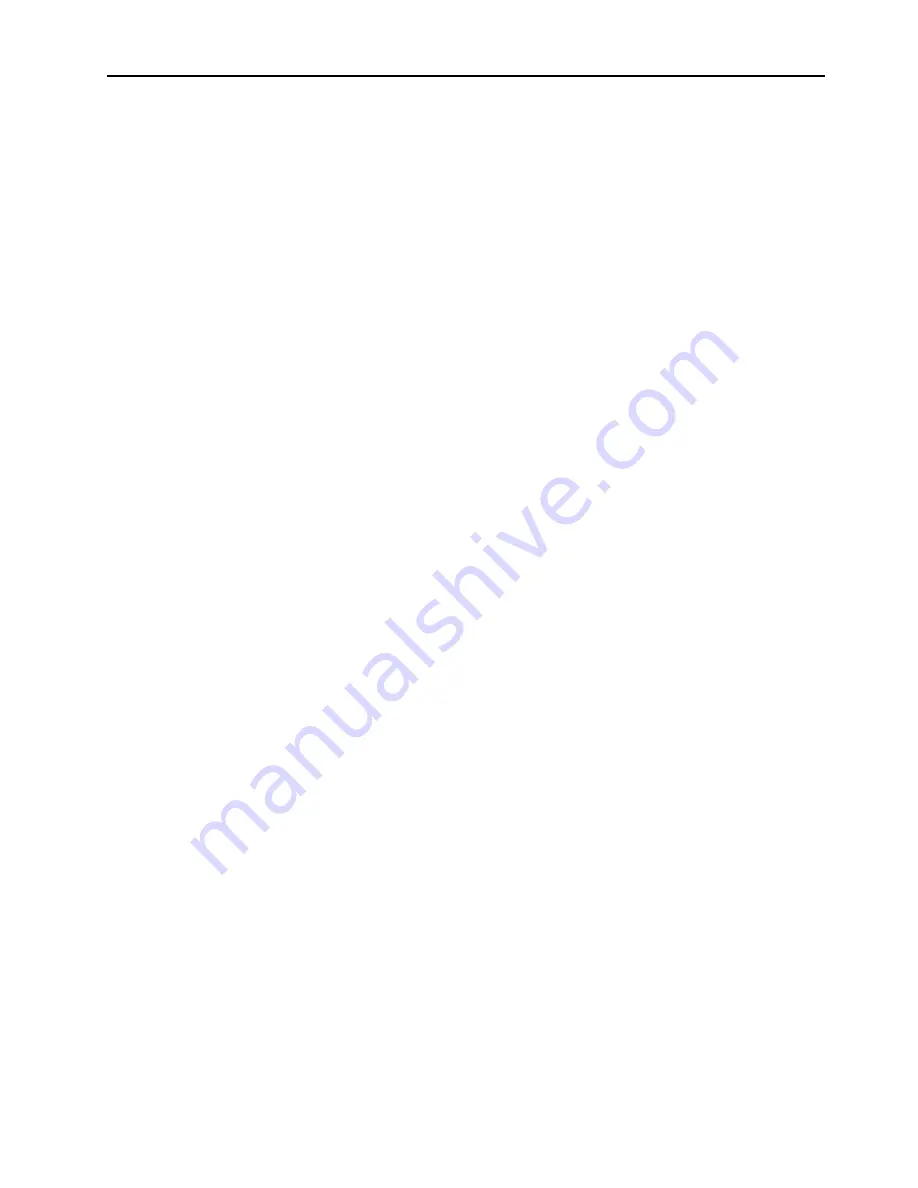
l
F.8L Falco Construction Manual
1–1
Revision 4, March 1, 2002
Chapter 1
Preparing for Construction
“Perfection is finally attained not when there is no longer anything
to add, but when there is no longer anything to take away.”
Antoine de Saint Exupéry
Wind, Sand and Stars
Welcome!
Welcome to the Falco. Like many others before you, you have fallen under the spell of this lovely
airplane. You are about to embark on a unique and enjoyable experience.
We look forward to working with you, hearing of your progress and finally that you have flown
your Falco. We hope you will find, as we have, that the Falco attracts a special type of person.
Where to Start?
The hardest part of building a Falco is getting started, so if you want to build the Falco, send your
order off now for the tail group kits and go to work.
The first step is to study the construction manual and the plans. You can expect to feel
completely overwhelmed at first. As you go over the drawings, your mind will go on “overload”.
Don’t worry, this happens to everyone… and it doesn’t last. At some point, you will begin to
understand the drawings. Little details which escaped your notice at first will start to make sense.
You can expect the project to become something of an obsession, and eventually, as all Falco
builder have done, you will even find that you will see the airplane in your dreams!
A lot of the Falco drawings are for parts which you will buy, so don’t spend a lot of time studying
them. Concentrate on the parts you will make and the assembly work you will do. There will be
many details which will not be clear at first, but they will come into focus as you approach the
assembly. So don’t spend a lot of time worrying about things that lie far in the future.
Concentrate on the first stages of the construction, which will be the tail group.
Family and Friends
It would be a good idea to discuss the Falco project with your family in advance. While you may
be thinking of the project simply as something that you want to do, you should not forget that the
Falco is likely to consume a lot of your time and energies. It will be a happier experience if
everyone in your family is behind the project and understands that you will be spending a lot of
time in the shop.
Friends are a different matter. In the early stages of the project, you will find friends and
acquaintances will not readily understand what you are doing. The notion of building an airplane
is foreign to them, and it will tend to sound like a pipe dream. Once the project is underway,
however, you will find that people can relate to an actual airplane under construction better than
they can to an idea. As the Falco takes shape, you will even find that visitors become something
of a distraction.
Your Shop
You will need a nest for your bird to hatch, so you should make plans for the shop and equip it
with tools. If you are able to have the shop at home, you will be able to spend more time on the
project. Your family will enjoy having you around and being able to check in on you. Nothing is
worse than building an airplane at the airport or some other remote location. Traveling to and
Summary of Contents for F.8L Falco
Page 1: ...F 8L Falco Construction Manual...
Page 7: ...l F 8L Falco Construction Manual Revision 4 March 1 2002...
Page 21: ...l F 8L Falco Construction Manual 1 8 Revision 4 March 1 2002...
Page 29: ...l F 8L Falco Construction Manual 2 8 Revision 4 March 1 2002...
Page 43: ...l F 8L Falco Construction Manual 5 4 Revision 4 March 1 2002...
Page 65: ...l F 8L Falco Construction Manual 9 6 Revision 4 March 1 2002...
Page 81: ...l F 8L Falco Construction Manual 10 16 Revision 4 March 1 2002...
Page 109: ...l F 8L Falco Construction Manual 15 4 Revision 4 March 1 2002...
Page 133: ...l F 8L Falco Construction Manual 17 10 Revision 4 March 1 2002...
Page 145: ...l F 8L Falco Construction Manual 18 12 Revision 4 March 1 2002...
Page 173: ...l F 8L Falco Construction Manual 21 10 Revision 4 March 1 2002...
Page 229: ...l F 8L Falco Construction Manual 23 40 Revision 4 March 1 2002...
Page 387: ...l F 8L Falco Construction Manual 28 26 Revision 4 March 1 2002...
Page 393: ...l F 8L Falco Construction Manual A 6 Revision 4 March 1 2002...