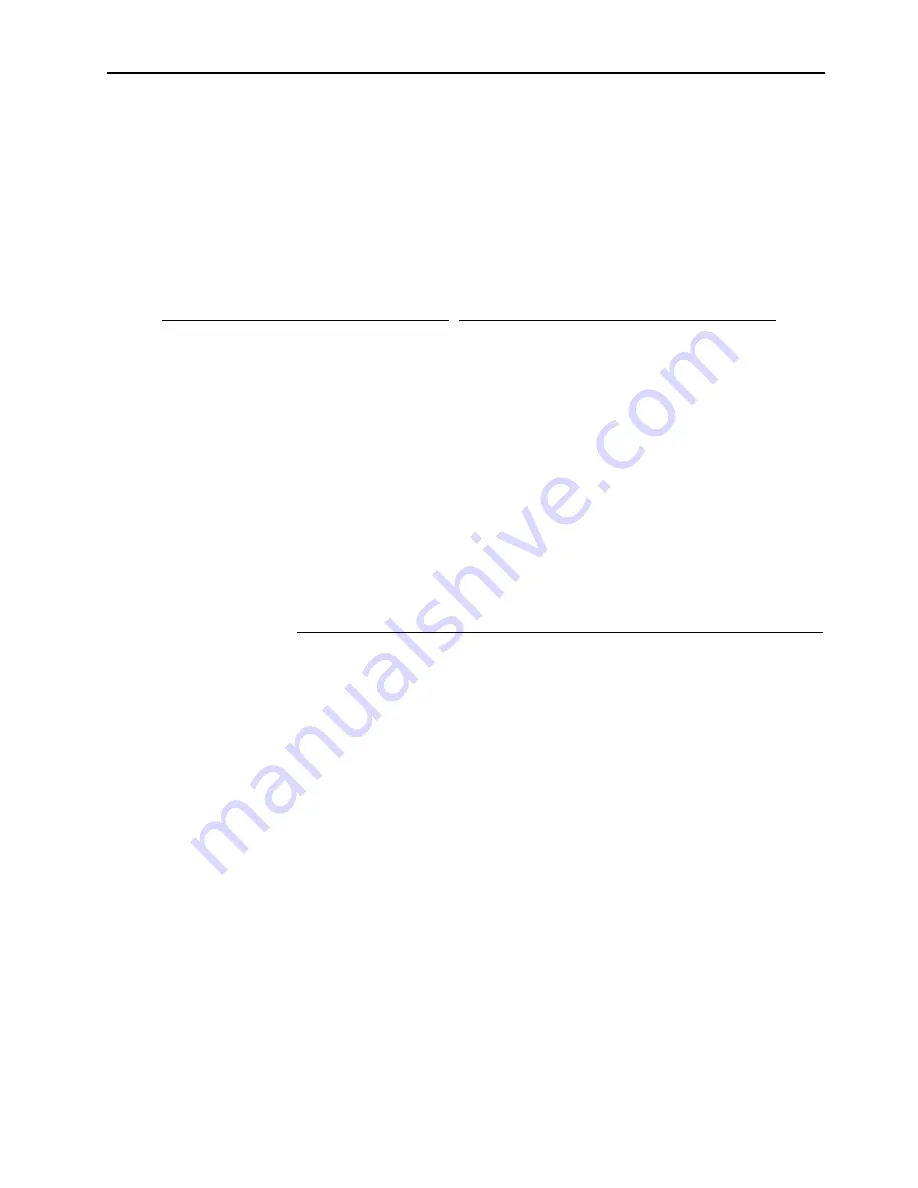
l
F.8L Falco Construction Manual
D–17
Revision 4, March 1, 2002
* Since resin and hardener have slightly different densities, but are supplied by weight,
mixing by volume will result in uneven consumption of the components.
Viscosity of Mixture
. Viscosity, 15-20 minutes after mixing, is similar for each grade of resin
used:
Viscosity:
1.5-2 Pa s (15-20 poises) at 25°C/77°F
Extension
. Wood flour or mineral filler may be added to increase the viscosity and reduce glue
costs. Typical mixtures are:
Lightly-Filled Mix
Heavily-Filled Mix
Aerodux 500: 100 parts by weight
Aerodux 500:
100 parts by weight
Hardener 501: 100 parts by weight
Hardener 501:
100 parts by weight
China clay:
40 parts by weight
China clay:
200 parts by weight
The lightly-filled mix still complies with the requirements of BS 1204: Part 1 (Type WBP). It
may be necessary to adjust the viscosity of the heavily-filled mix with water but the water addition
should be kept to a minimum. This mix is suitable for bonding uneven-surfaced boards, such as
asbestos-based boards, where maximum strength and full weatherproof properties are not required
Mixing
. Hardener 501 must be well stirred before removal from the container. Add the required
amount of Hardener 501 to the Aerodux 500 and mix thoroughly. Addition may be measured by
weight or volume.
Pot Life
. Pot life of resin-hardener mixture in relation to temperature:
Temperature of Resin-Hardener Mixture (°C/°F)
Resin
5°/41°
10°/50°
15°/59°
20°/68°
25°/77°
30°/86°
35°/95°
500.F (fast)
9-10 hrs
6-7 hrs
4-5 hrs
1.5-2 hrs —
—
—
500.M (med) —
—
5.5-6.5 hrs 3-3.5 hrs 2-2.5 hrs 1-1.5 hrs —
500.S (slow) —
—
—
—
3.5-4 hrs 2.5-3 hrs 1.5-2 hrs
Surface Preparation
. The surfaces to be bonded should be free from dust and other deposits.
Wood, panels, laminates, etc., should be of uniform thickness. Solid timber should be freshly
machined, but does not usually require sanding. Smooth dense surfaces to be bonded—except
expanded plastics and asbestos-based boards—should also be thoroughly sanded.
Metal surfaces should be abraded and coated with Primer L.62 before bonding to porous materials
(such as wood). Directions are given in Ciba-Geigy Instruction Sheet No. AD.4.
Moisture Content
. Satisfactory results may be obtained when the moisture content of the
surfaces to be bonded is within the range 6-25%, but for best results, 12-16% is preferred.
Artificial drying will be required to reduce the moisture content to 16% or lower. Adjacent
surfaces should not differ by more than 3% moisture content.
Application
. Whenever practicable it is advisable to spread the resin-hardener mixture evenly on
both of the bonding surfaces. For coverage see "Control of Spread to Counteract Drying-Out"
below.
Summary of Contents for F.8L Falco
Page 1: ...F 8L Falco Construction Manual...
Page 7: ...l F 8L Falco Construction Manual Revision 4 March 1 2002...
Page 21: ...l F 8L Falco Construction Manual 1 8 Revision 4 March 1 2002...
Page 29: ...l F 8L Falco Construction Manual 2 8 Revision 4 March 1 2002...
Page 43: ...l F 8L Falco Construction Manual 5 4 Revision 4 March 1 2002...
Page 65: ...l F 8L Falco Construction Manual 9 6 Revision 4 March 1 2002...
Page 81: ...l F 8L Falco Construction Manual 10 16 Revision 4 March 1 2002...
Page 109: ...l F 8L Falco Construction Manual 15 4 Revision 4 March 1 2002...
Page 133: ...l F 8L Falco Construction Manual 17 10 Revision 4 March 1 2002...
Page 145: ...l F 8L Falco Construction Manual 18 12 Revision 4 March 1 2002...
Page 173: ...l F 8L Falco Construction Manual 21 10 Revision 4 March 1 2002...
Page 229: ...l F 8L Falco Construction Manual 23 40 Revision 4 March 1 2002...
Page 387: ...l F 8L Falco Construction Manual 28 26 Revision 4 March 1 2002...
Page 393: ...l F 8L Falco Construction Manual A 6 Revision 4 March 1 2002...