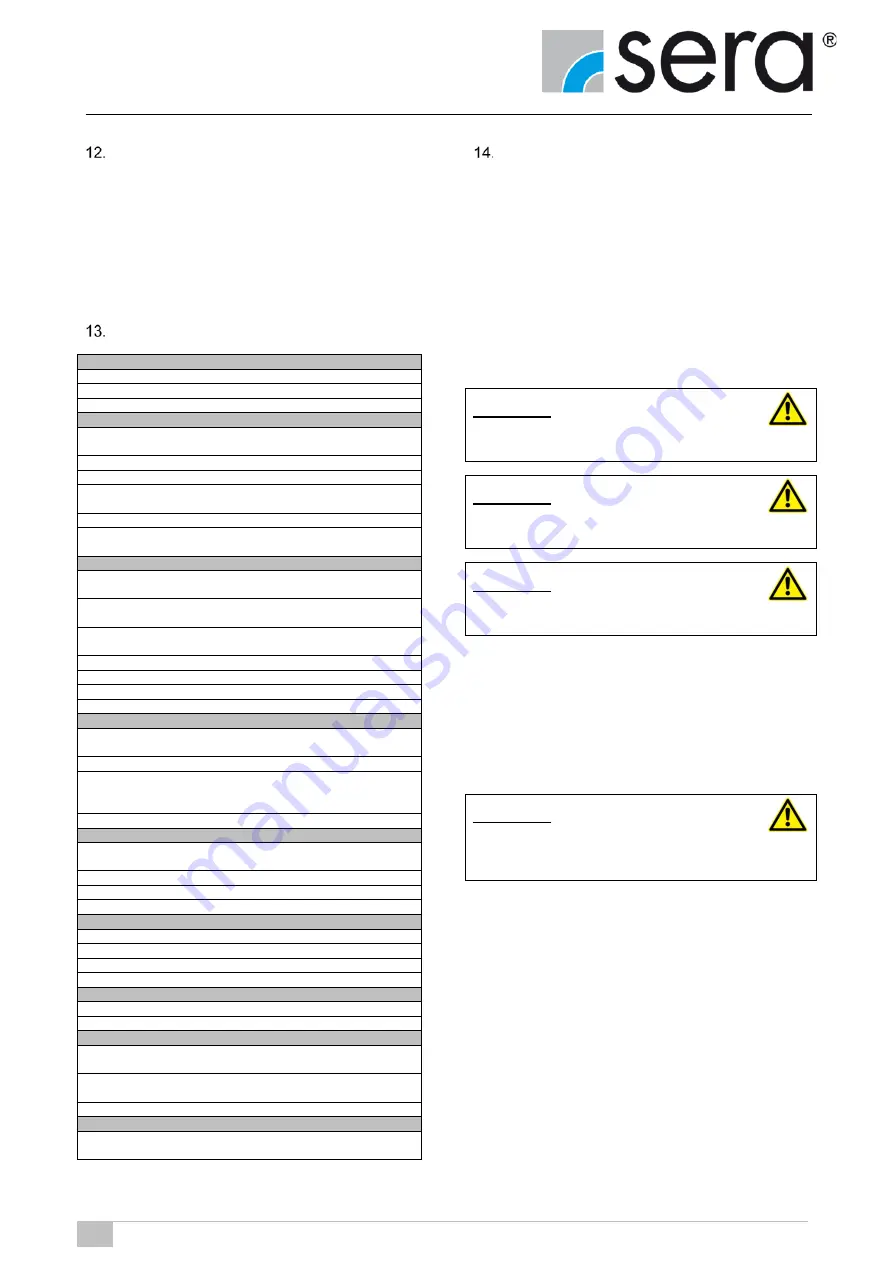
Systèmes de dosage – construction verticale
CVD 1 (s) / CVD 2
Notice d’utilisation
50
Sous réserve de modifications techniques !
Subject to technical modifications!
www.sera-web.com
TA450-11 / fr/en /01.2017 / PM
Fault analysis and corrective action
sera
products are sophisticated technical products which are
only shipped after having been thoroughly tested and checked
at our factory.
Should there be any faults, these can be detected and rectified
easily and quickly according to the following instructions.
•
For fault analysis and corrective action of the dosing
pumps, please see the separate instructions on the data
carrier.
Remaining risk / foreseeable faults
Transport of the system
Load is not sufficiently secured for transport.
Transport by untrained personnel.
Removal of transport lock of the pump.
Installation
Installation of the system at an improper site (outside, direct
sunlight, explosion-hazardous area etc.)
Confusion of the suction and pressure pipes.
Threads overturned/damaged
Do not replace the transport closure at the oil filler cap with
the vent screw.
Piping bent when it was mechanically connected
Non-conforming electrical connection
(without ground wire, mains not fuse-protected etc.)
Commissioning
Non-observance of the design data/operating conditions (me-
dium, pressure, suction height, temperature etc.)
Incomplete removal of the test medium (water) before start-
up with the chemical (dangerous reactions)
Non-observance of the electrical characteristics (motors, sen-
sors)
Cover on vent openings (motor)
Closed suction and pressure pipes
Wrong settings of the overflow valves
Overfilling of the multifunction device during suction
Operation
Operation of the pump/overflow valve with defective dia-
phragm
Ignoring a pump fault
Operation of the system beyond the limit values
(nominal pressure exceeded, pressure peaks, contaminated
medium (with particles))
Sudden closure of the pressure pipe
Maintenance
Disregard of the maintenance schedule according to the op-
erating instructions
Improper maintenance
Use of non-original spare parts
Insufficient rinsing before maintenance work
Cleaning
Protective clothing insufficient or missing
Wrong rinsing/cleaning agent
Use of unsuitable cleaning utensils
Rinsing/cleaning agent residues in the system
Repair/corrective action
Repair work by untrained personnel
Improper execution of repair work
Decommissioning
Insufficient removal of the pumped medium from the pipes
with subsequent rinsing
Disassembly of pipes with the pump running (residual pres-
sure)
Disconnection from the power supply not ensured
Disposal
Improper disposal of the pumped medium, utilities and mate-
rials
Disposal
Shut-down the system. Please see “Decommissioning”.
14.1 Disassembly and transport
•
Remove all fluid residues, clean thoroughly, neutralize
and decontaminate.
•
Rinse the pipes with water (water quality see Chapter 2)
or a suitable medium and empty the pipes afterwards.
•
Package the dosing system appropriately and ship.
•
If the system is shipped for repair the gearing must be
filled with oil.
CAUTION !
Transport the system in a horizontal position!
CAUTION !
Check if the transport lock of Pump is mounted!
CAUTION !
Close the pipe openings for transport!
14.2 Complete disposal
•
Remove all fluid residues (incl. utilities) from the unit.
•
Drain lubricants and hydraulic fluids and dispose off ac-
cording to the regulations!
•
Rinse the pipes with water (water quality see Chapter 2)
or a suitable medium and empty the pipes afterwards.
CAUTION !
The consignor is responsible for damage caused by leak-
ing lubricants and fluids!