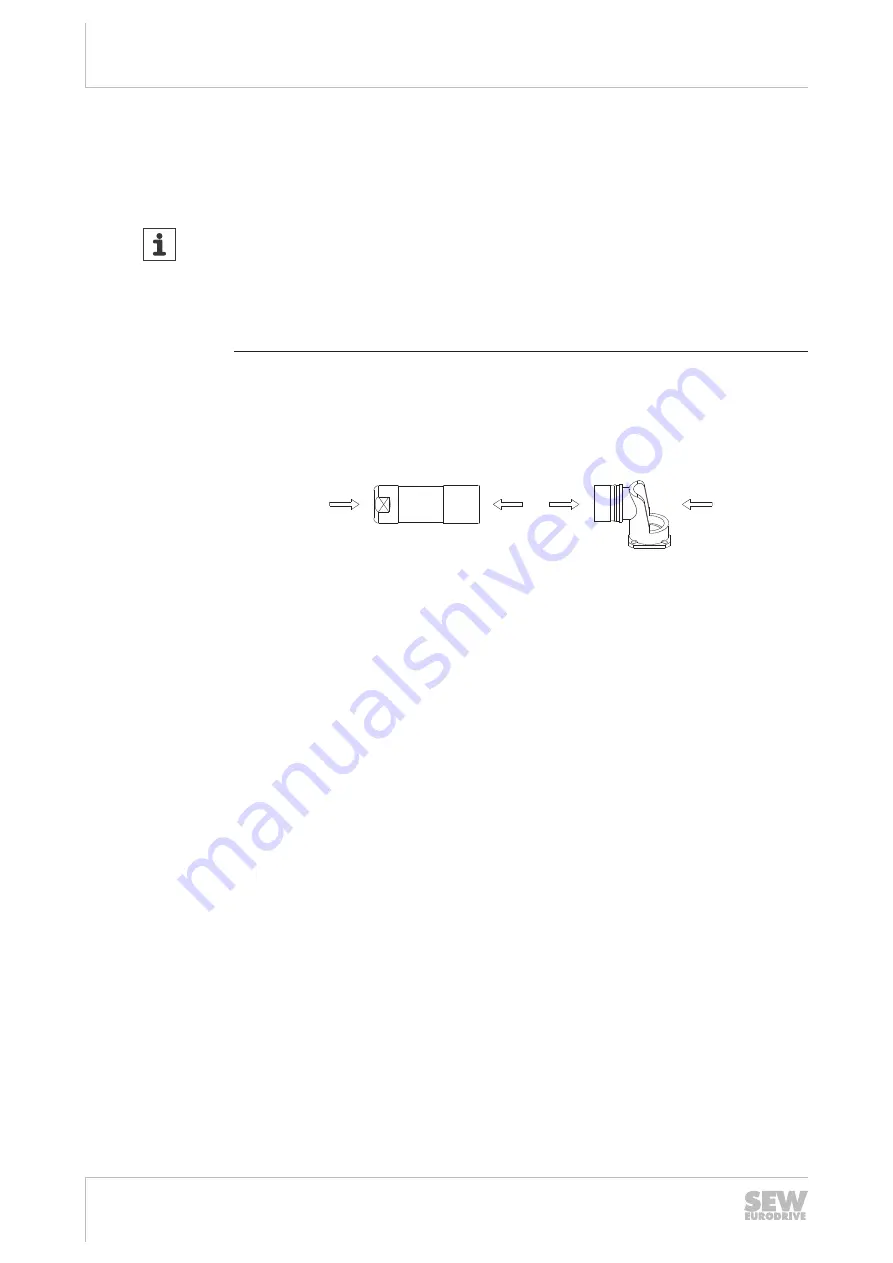
5
Electrical installation
Connecting the plug connectors – Single-cable technology for CM3C.. motors in encoderless design
Operating Instructions – CM3C63 – 100
44
5.7
Connecting the plug connectors – Single-cable technology for CM3C..
motors in encoderless design
INFORMATION
Using an inverter with suitable control mode is mandatory for operating a CM3C.. mo-
tor in encoderless design.
The following control modes by SEW‑EURODRIVE are available:
•
ELSM
®
control mode (Encoderless Synchronous Machine)
•
PMVC control mode (Permanent Magnet Vector Control)
The wiring diagrams of the motors are available in the SEW‑EURODRIVE Online Sup-
port.
5.7.1
Key
[A]
[C]
[B]
[A]
[D]
[B]
8790995467
[A] View A
[B] View B
[C] Customer connector with socket contacts
[D] Flange socket with pin contacts installed at the factory
26870460/EN – 05/2021