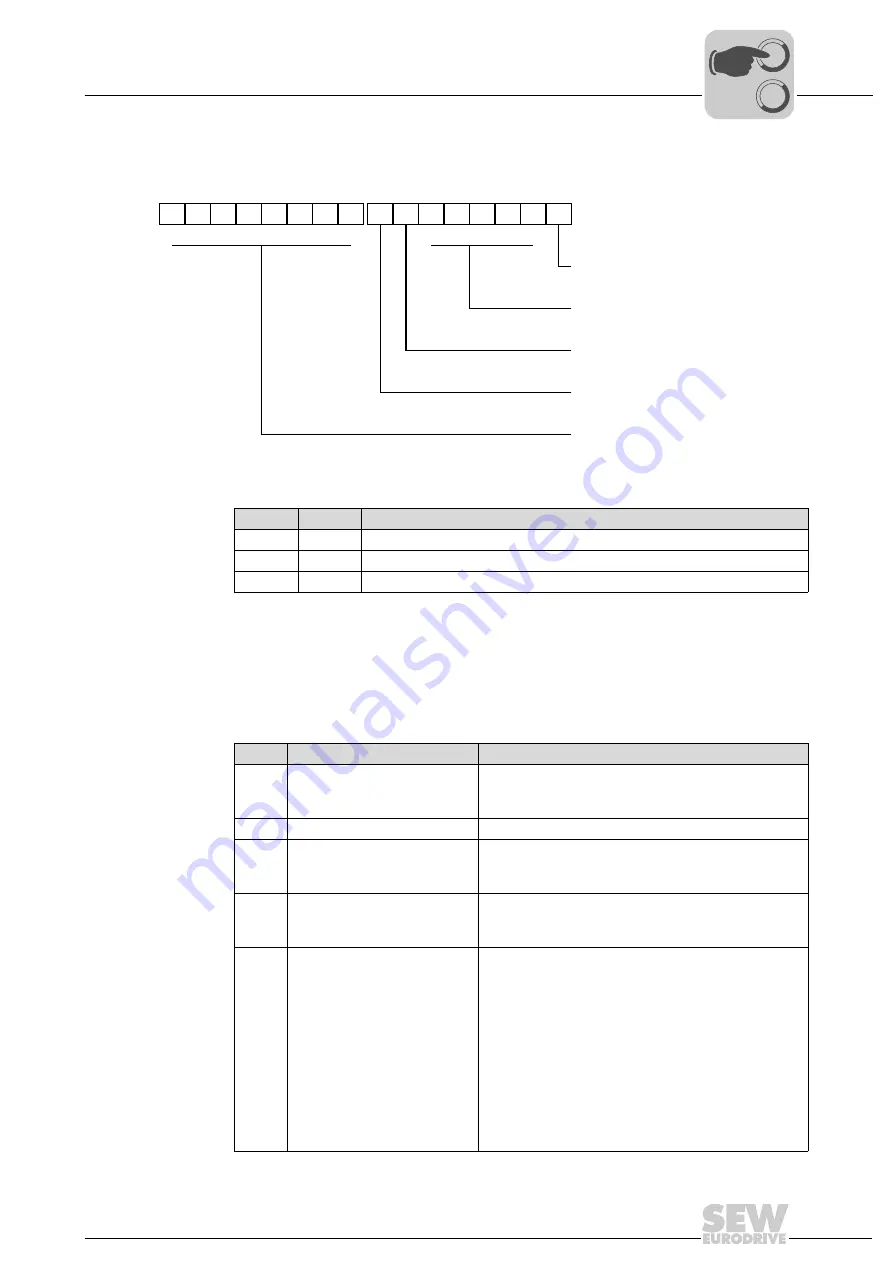
Manual – MOVIPRO® SDC with DeviceNet Interface
53
8
MOVIPRO
®
status word
Process Data Description
8.3
MOVIPRO
®
status word
The following figure shows the assignment of the MOVIPRO
®
status word:
Bits 8 – 15 are assigned depending on the value of bits 6 and 7 according to the following
table:
The following table shows the diagnostics information of theMOVIPRO
®
unit that is pro-
cessed in the higher-level PLC application. The signals are transferred to the controller
via parameters and, if necessary, via the process data channel.
The logical communication status "0" signals the status "OK" for each signal to ensure
that no asynchronous startup sequences from the bus master and the PLC can cause
incorrect diagnostic messages when the systems are started up (bus startup with user
data = 0).
Master
←
15 14 13 12 11 10
9
8
7
6
5
4
3
2
1
0
←
MOVIPRO
®
0:
Maintenance switch (mains
OFF)
1 – 5: Reserved = 0
6: MOVIPRO
®
warning
7: MOVIPRO
®
error
8 – 15:
Unit status/warning/error num-
ber
Bit 6
Bit 7
Assignment of bits 8 – 15
0
0
MOVIPRO
®
unit status
1
0
MOVIPRO
®
warning
0
1
MOVIPRO
®
error
Bit
Diagnostic name via bus
Function and coding
0
Maintenance switch (mains
OFF)
Maintenance switch (mains OFF)
1 = Maintenance switch activated (mains off)
0 = OK (not activated)
1 – 5
Reserved
0 = reserved
6
MOVIPRO
®
warning
MOVIPRO
®
warning
1 = MOVIPRO
®
warning present
0 = OK
7
MOVIPRO
®
error
MOVIPRO
®
error
1 = MOVIPRO
®
error present
0 = OK
8 – 15
Unit status/warning/error num-
ber/
Unit status (bit 6 = 0, bit 7 = 0):
•
0: System startup
•
1: Ready
Warning (bit 6 = 1, bit 7 = 0)
Error number (bit 6 = 0, bit 7 = 1)
•
1: Configuration
→
no configuration available
•
2: Configuration
→
Connection to configured units could
not be established
•
5: Process data to lower-level units stopped
•
99: Internal system error
•
110: Actuator voltage overload
•
120: Overload sensor voltage group 1
•
121: Overload sensor voltage group 2
0
0
I