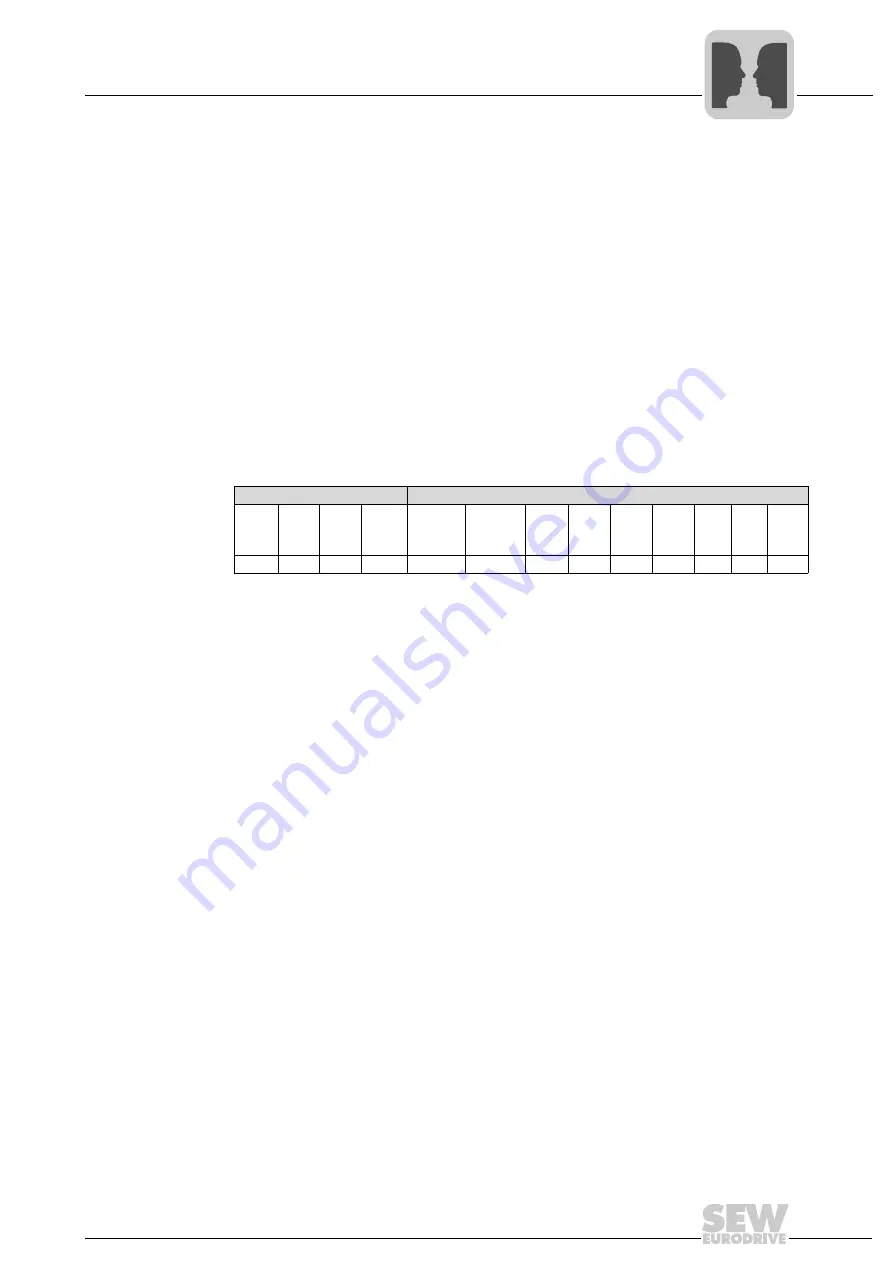
Operating Instructions – Electronic Motor DRC.-..-DAC
159
9
Transmitting individual parameters via AS-Interface
Communication with AS-Interface Double Slave GLK31A
MOVILINK
®
parameter
exchange with
"Exchange
request"
Executing the CTT2 service "Exchange request" 0x1D, the AS-Interface master sends
a telegram with the DRC parameter data to the double slave and receives the response
data immediately with the response telegram.
Select index 0x02
hex
and length 0x09
hex
.
• If this service has been executed correctly, the GLK31A double slave sends the
response telegram 0x5D
hex
"Exchange response OK" and the read data.
• If errors occur, the GLK31A double slave sends the response telegram 0x9D
hex
"Exchange response not OK" (for the error code, refer to the AS-Interface specifica-
tion).
• If the response data of the DRC inverter are not available yet, the GLK31A double
slave sends a response with error code "Busy" = "4" after the read access.
Example:
Changing the fixed setpoint value n4 (parameter
10096.38
) to 1000 rpm:
"Exchange request" service:
CTT2 service
MOVILINK
®
protocol
Code Index Read
length
Write
length
Address-
ing
Manage-
ment
Sub-
index
High
index
Low
index
MSB
data
Data Data
LSB
data
0x1D
0x02
0x09
0x09
0x00
0x32
0x26
0x27
0x70
0x00 0x0F 0x42 0x40
Code 0x1D =
Exchange request
Index 0x02 =
MOVILINK
®
parameter service
Read length 0x09 =
Length of the MOVILINK
®
response
Write length 0x09 =
Length of the MOVILINK
®
request
Addressing 0x00 =
Addressing the command PCB because this is where the parameter is stored
Management 0x32 =
Write parameter
Subindex 0x26 =
Subindex of parameter fixed setpoint n4 (10096.38) 38
dec
= 0x26
High index 0x27 =
High value of the index
Low index 0x70 =
Low value of the index
=> Index of the parameter = 10096
dec
= 0x2770
hex
The value 0x2770
hex
is written on the high index and low index bytes.
Data MSB 0x00
The internal scaling of the DRC inverter is 1000 times higher than the real
scaling.
The scaling factor then is 1 000 000
dec
= 0xF4240.
This value is written to the 4 data bytes.
Data 0x0F
Data 0x42
Data LSB 0x40