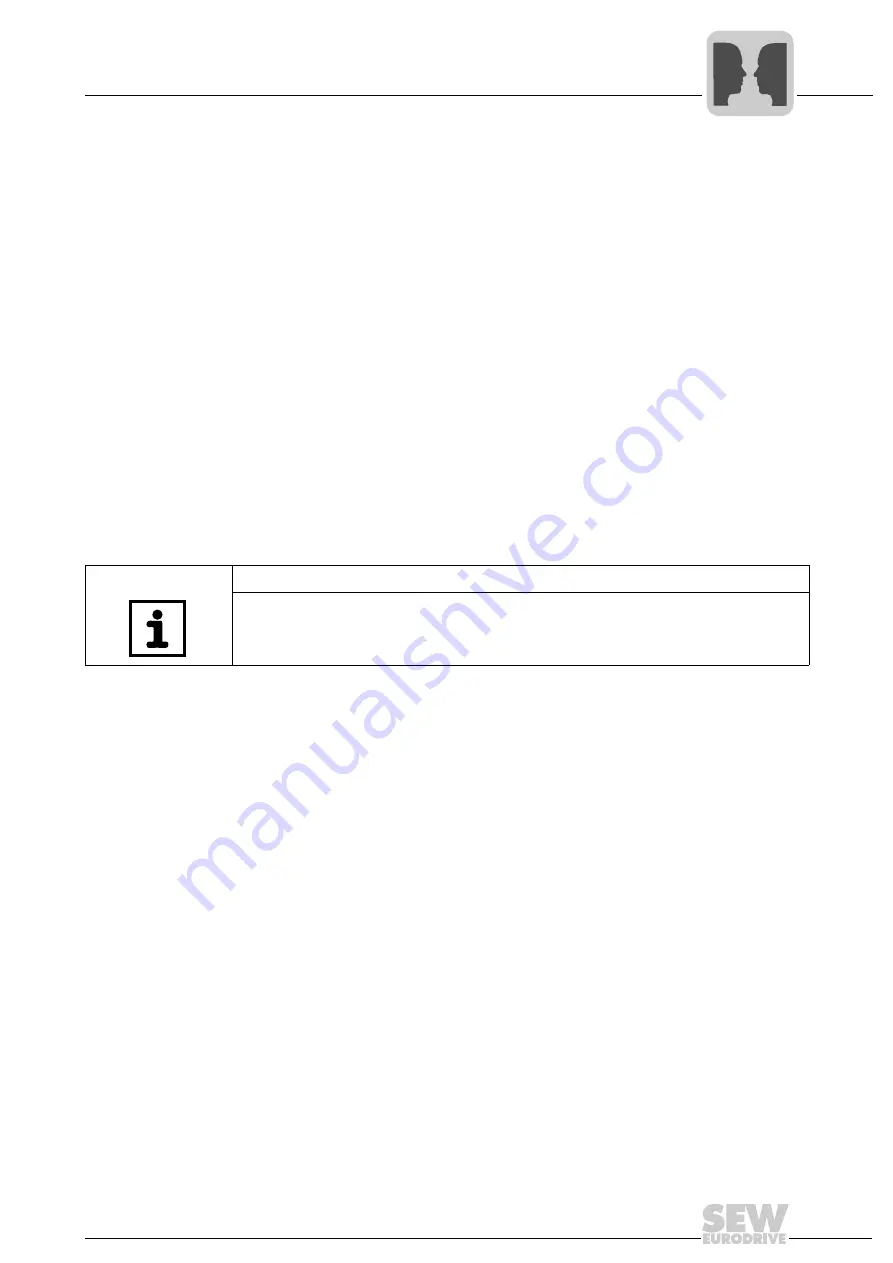
Manual – MOVIDRIVE® MDX60B/61B Communication and Fieldbus Unit Profile
73
6
Process and parameter access via fieldbus
Fieldbus Interfaces via Option Card for MOVIDRIVE® B
6.3
Process and parameter access via fieldbus
The access to process and parameter data differs strongly depending on the bus
systems and controller used.
What applies to most bus systems is that up to 10 process input data words (PI) with
16 bits each are sent to the controller and up to 10 process output data words (PO) with
16 bits each are sent from the controller to MOVIDRIVE
®
via a dual-port RAM. In addi-
tion, certain options (e.g. DFE24B) allow for cyclically reading and writing 8 IPOS
plus®
double words.
6.4
Other unit functions via fieldbus option card
The following additional functions can be used via fieldbus options in addition to the
exchange of process and parameter data between controller and MOVIDRIVE
®
.
6.4.1
Using the fieldbus options in IPOS
plus®
Process data transmitted via fieldbus can be directly accessed in the IPOS
plus®
position
and sequence control system integrated in MOVIDRIVE
®
using the commands
GETSYS PO data and SETSYS PI data. Set the bus type to "3" for this purpose.
6.4.2
Engineering via fieldbus
In addition to accessing process and parameter data by the controller, some fieldbus
options (e.g. DFP21B, DFE32B or DFE33B) also allow for parallel,
controller-
independent
engineering access to MOVIDRIVE
®
via fieldbus. In this case, the
engineering PC is directly connected to the bus system using an appropriate interface
(e.g. PROFIBUS or Ethernet). The controller need not necessarily be in RUN mode for
this purpose. The engineering access is described in the relevant manuals for the field-
bus options.
6.4.3
Engineering via fieldbus and controller
With some fieldbus options (e.g. DFP21B, DFE24B or DFI), access to MOVIDRIVE
®
is
possible using an engineering PC through the controller via fieldbus in addition to the
access to process and parameter data via controller.
For this purpose, the engineering PC is connected to an engineering interface of the
controller (e.g. Ethernet interface of Siemens S7, of the EtherCAT or Interbus master)
and then passes the telegrams of the MOVITOOLS
®
MotionStudio engineering software
to the MOVIDRIVE
®
via fieldbus. The controller usually has to be in RUN mode to do so.
TIP
You find a detailed description of IPOS
plus®
in the "IPOS
plus®
Positioning and
Sequence Control System" manual.
Summary of Contents for MOVIDRIVE MDX60B
Page 2: ...SEW EURODRIVE Driving the world...
Page 142: ......
Page 143: ...SEW EURODRIVE Driving the world...