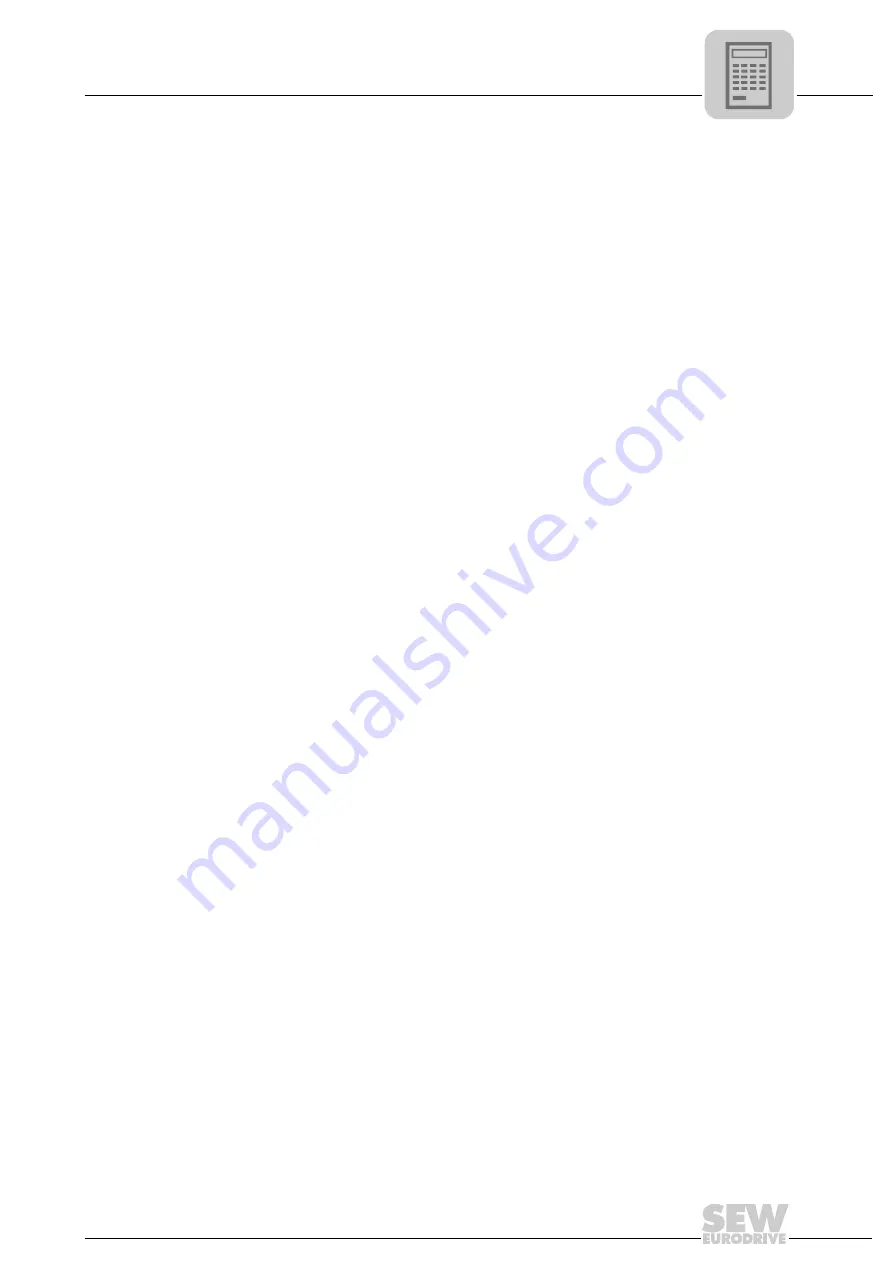
Manual – MOVIDRIVE® MDX60B/61B Communication and Fieldbus Unit Profile
75
7
Other unit functions via fieldbus option card
SEW Unit Profile
7
SEW Unit Profile
MOVIDRIVE
®
offers digital access to all drive parameters and functions via the commu-
nication interfaces. The drive inverter is controlled via the fast, cyclical process data. Via
this process data channel, you can enter setpoints, such as setpoint speed, ramp gen-
erator time for acceleration/deceleration, etc. as well as trigger various drive functions
such as enable, controller inhibit, normal stop, rapid stop, etc. At the same time you can
use this channel to read back actual values from the drive inverter, such as actual
speed, current, unit status, error number or reference signals.
In combination with the IPOS
plus®
positioning and sequency control integrated in the
drive inverter, you can also use the process data channel as direct connection between
PLC and IPOS
plus®
. In this case, the process data are not evalued by the drive inverter
but directly by the IPOS
plus®
program.
While the process data exchange generally occurs cyclically, the drive parameters can
be read or written acyclically using READ and WRITE services. This parameter data
exchange enables you to implement applications in which all the important drive
parameters are stored in the master programmable controller, so that there is no need
to make parameter settings manually on the drive inverter itself.
The use of a fieldbus system requires additional drive system monitoring such as time
monitoring of the fieldbus (fieldbus timeout) or even special emergency stop concepts.
The MOVIDRIVE
®
monitoring functions can be customized to your application. You can
determine, for instance, which of the drive inverter’s error responses should be triggered
in the event of a bus error. A rapid stop is a good idea for many applications, although
this can also be achieved by "freezing" the last setpoints so the drive continues operat-
ing with the most recently valid setpoints (such as with a conveyor belt). As the functions
of the control terminals are still active in fieldbus operation, you can still implement field-
bus-independent emergency stop concepts via the terminals of the drive inverter.
The MOVIDRIVE
®
inverter offers numerous diagnostic options for startup and service.
For example, you can use the DBG60B keypad to control both setpoint values sent from
the higher-level controller as well as the actual values. You are also supplied with a
variety of additional information about the status of the communication interfaces. An
even more convenient diagnostic option provides the MOVITOOLS
®
MotionStudio
engineering software. It lets you set all drive and communication parameters and
displays detailed information of interfaces and unit status.
Summary of Contents for MOVIDRIVE MDX60B
Page 2: ...SEW EURODRIVE Driving the world...
Page 142: ......
Page 143: ...SEW EURODRIVE Driving the world...