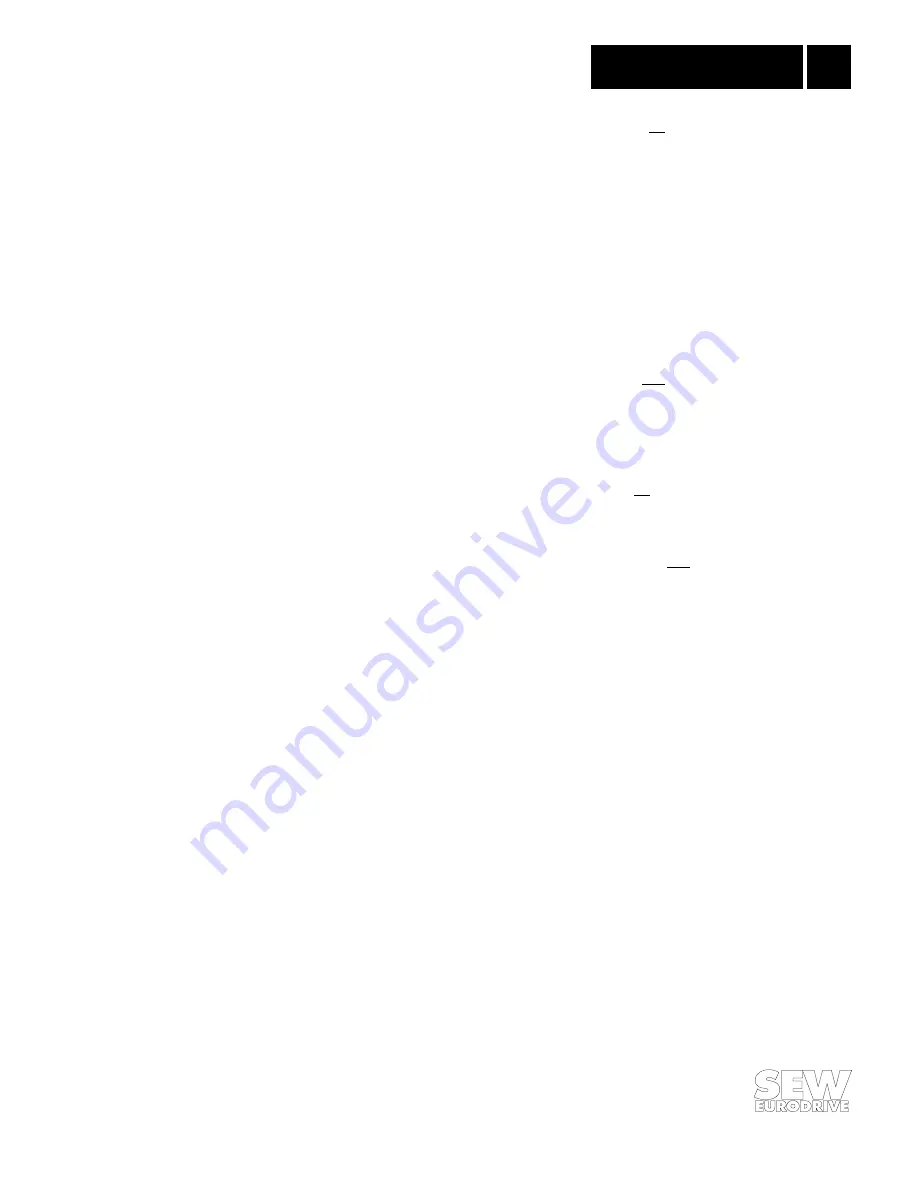
MOVITRAC
®
31.. – FRS 31
13
Parameters
4
P 554
Positional tolerance of slave
Value range = 10...25...32,768
Various requirements must be satisfied to ensure
accurate positioning of the slave
.
The brake on the slave drive is applied when
all the following conditions
are satisfied:
• setpoint stop function
P 180 = “Yes”
activated
• the master is stationary
• the
master
is current free (no premagnetization, no hold control, no residual magnetization, no
resistance measurement (SxR), no rapid start magnetization, no DC injection braking and no
heating current)
• the
slave is stationary
and in the
position window
This signal can be used, for example, as a position signal and can be programmed as a signal
output
– on one of the three binary outputs, terminals 62/63/64 (P 611/612/613).)
P 555
LED counter
Value range = 10...100...32,768
The “MASTER-SLAVE DIFFERENCE” LED V11 (green) lights up if the angular offset exceeds the
value entered here. This enables the actual maximum angular difference between master and slave
to be indicated. This is particularly helpful during commissioning.
ON = angular difference > value of P 555 / OFF = angular difference < value of P 555
P 556
Time constant position signal
Value range = 5...10...2,000 ms
The “slave in position” binary output signal is not issued until the master and slave have remained
within the positional tolerance P 554 for the time specified in P 556.
P 557
Cable break master-slave
Yes / No
Monitoring of the setpoint line between the master and the slave uses the connection between the
binary output “zero speed” on the master and the binary input “FRS CTRL” on the slave as a refer-
ence signal. If “zero speed” = 0 and the FES 31 pcb is not receiving any setpoint input, the unit
assumes a cable break on the setpoint line or the line between “zero speed” and “FRS CTRL”. It
then issues error message 36 “master slave connection”.
For “open-circuit monitoring”, the MOVITRAC
®
31.. of the master must be fitted with the FEN 31
“Speed Detection” option. Speed control must be activated.
Note:
Set P 557 = “No” if:
- master motors with no inverter or
- encoders with < 512 increments/revolution (P 773)
(open-circuit monitoring is not possible in all modes of operation)
P 600 ... 606
Binary inputs
The programmable binary inputs on terminals 42/43/47/48/49/50/51 can be allocated four addi-
tional signal types for synchronous operation.
• The internal counter for the angular offset can be set to zero with
“FRS set zero”
.
“1” signal = present angular difference will be cleared.
“1”
→
“0” = new reference point for synchronous operation. If this function is only required
during commissioning, the binary input can subsequently be reassigned; this will be necessary
if the master and slave need to be lined up with one another.
• The terminal to which
“FRS CTRL”
is assigned is connected to the “zero speed” binary output
on the master. This is for open-circuit monitoring purposes (P 557).
Phone: 800.894.0412 - Fax: 888.723.4773 - Web: www.clrwtr.com - Email: info@clrwtr.com