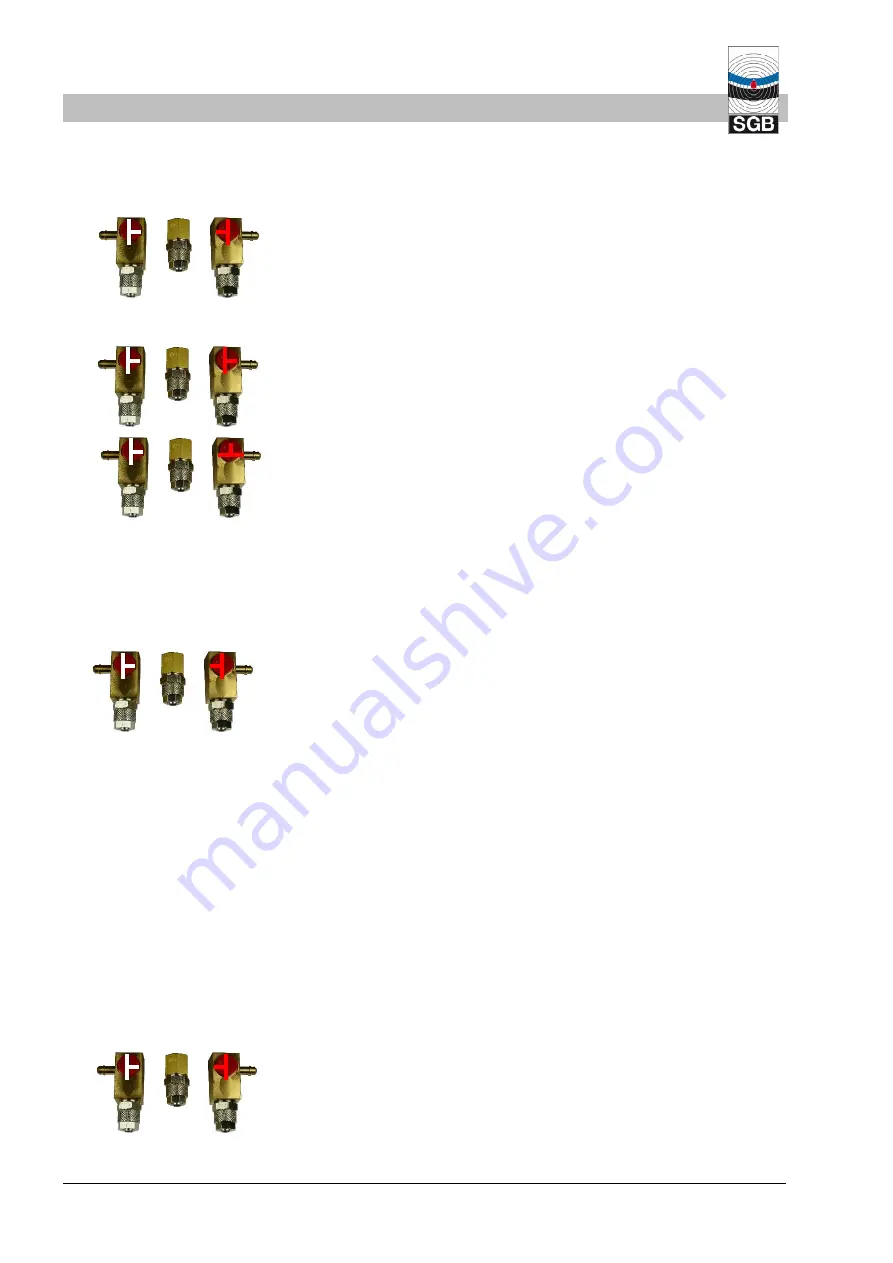
VACUUM LEAK DETECTOR
VLXE .. Ex M and VLXE .. Ex MMV
28/07/2020
- 38 -
(4) The test is considered passed if the vacuum does not drop by
more than 1 mbar during the test period.
Of course, a multiple of the test period can also be measured; in
this case, the permissible vacuum drop is also a multiple.
(5) Once the test is complete, return valves to their original positions
and remove the measuring gauge.
7.3.7 Checking the excess pressure alarm (only for version VLXE .. Ex MMV)
(1) Attach excess pressure testing device to connection on three-
way valve 21 and turn valve 180°.
(2) Then turn three-way valve 21 90°.
(3) Apply pressure using the excess pressure testing device. First
the pumps are switched on, then the alarm is triggered (red LED
on), and if the pressure continues to increase, the excess pres-
sure alarm is triggered (yellow LED flashes).
(4) With the overpressure alarm, the pump halts and the solenoid
valve switches.
(5) Relieve excess pressure by detaching the excess pressure test-
ing device. This alarm goes out and the pump runs; the solenoid
valve opens.
(6) Once the test is complete, return valves to their original positions
and remove the measuring gauge.
7.3.8 Checking the additional pressure switch in conjunction with VLXE .. Ex MMV
(1) Connect the testing device as per Section 7.3.5 and complete
steps (1) to (5).
(2) Close shut-off cock on the interstitial space side.
(3) Connect an external pressure booster to connection 82 and open
the relevant valve.
(4) Pressure build-up until activation of the pressure switch (probe
alarm is triggered and the solenoid valve switches).
(5) Check the corresponding alarm.
(6) Relieve pressure; probe alarm goes out and the solenoid valve
switches.
(7) Close the shut-off cock at 82 and remove the pressure booster.
(8) Open the shut-off cock on the interstitial space side, put three-
way valves 20 and 21 into operating position, and remove testing
device.
21
20
21
20
Functional Check and Maintenance
21
20
21
20
21
20
Summary of Contents for VLXE Ex M Series
Page 49: ...28 07 2020 VACUUM LEAK DETECTOR VLXE Ex M and VLXE Ex MMV 49 12 7 Ex approval Appendix ...
Page 50: ...VACUUM LEAK DETECTOR VLXE Ex M and VLXE Ex MMV 28 07 2020 50 Appendix ...
Page 51: ...28 07 2020 VACUUM LEAK DETECTOR VLXE Ex M and VLXE Ex MMV 51 Appendix ...
Page 52: ...VACUUM LEAK DETECTOR VLXE Ex M and VLXE Ex MMV 28 07 2020 52 Appendix ...
Page 54: ...VACUUM LEAK DETECTOR VLXE Ex M and VLXE Ex MMV 28 07 2020 54 Appendix ...