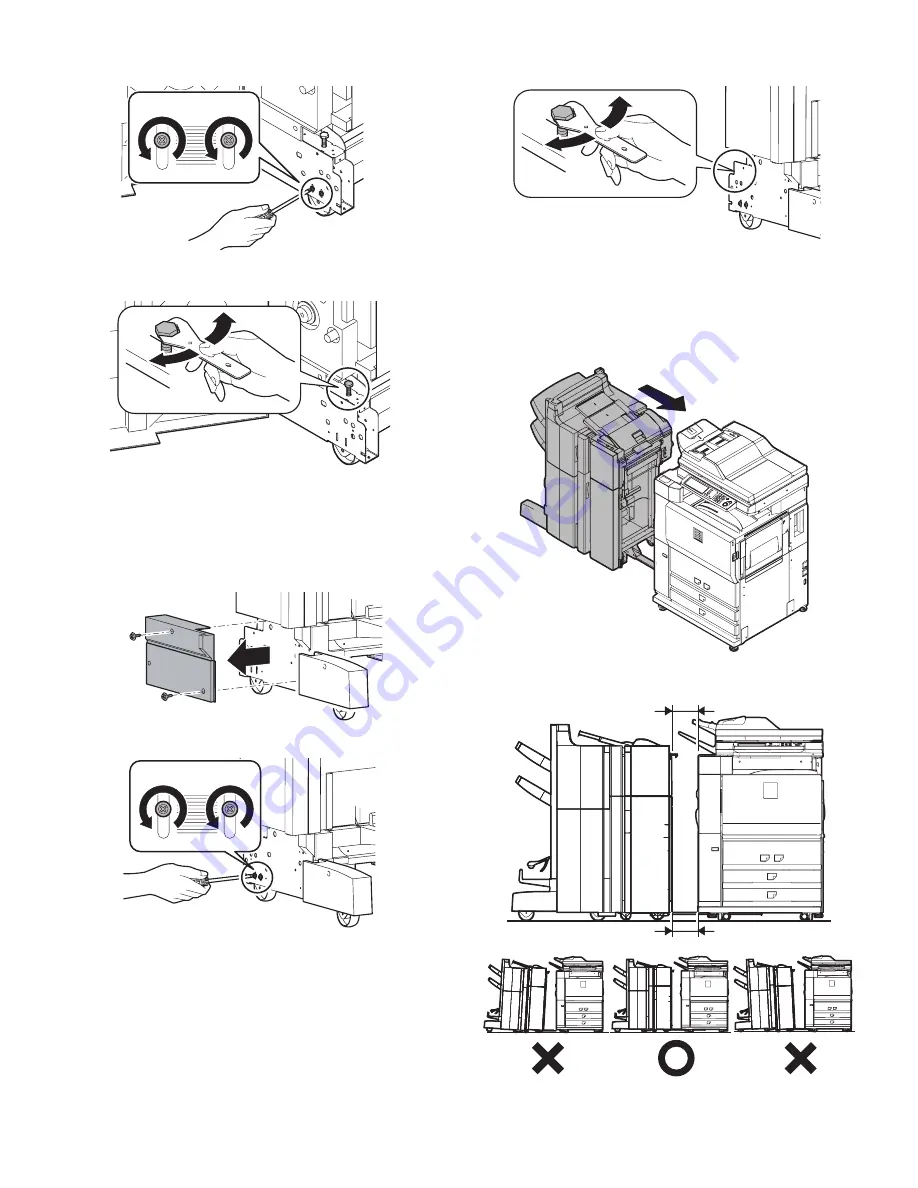
AR-M550/M620/M700 INSTALLATION MANUAL (AR-CF2) 3 - 8
3) Loosen the fixing screws (2 pcs.) of the adjustment section of the
base.
4) Use the spanner removed in step 1) to adjust the height adjustment
bolt so that the upper cabinet is of the same height.
5) Tighten the adjustment section fixing screws (2 pcs.).
6) Close the finisher front door lower, and close the inserter front door.
B. Adjust the rear side height.
1) Remove two screws which are fixing the base cover attached to the
finisher rear side base section, and remove the base cover.
2) Loosen the adjustment section fixing screws (2 pcs.).
3) Use the spanner and adjust the height adjustment bolt so that the
height of the rear side cabinet top surface is of the same height.
4) Tighten the adjustment section fixing screws (2 pcs.).
5) Install the base cover.
(13) Check the clearance between the main unit and the
inserter
1) Push the inserter into the main unit.
2) Check the upper and the lower clearances between the main unit
and the inserter cabinet.