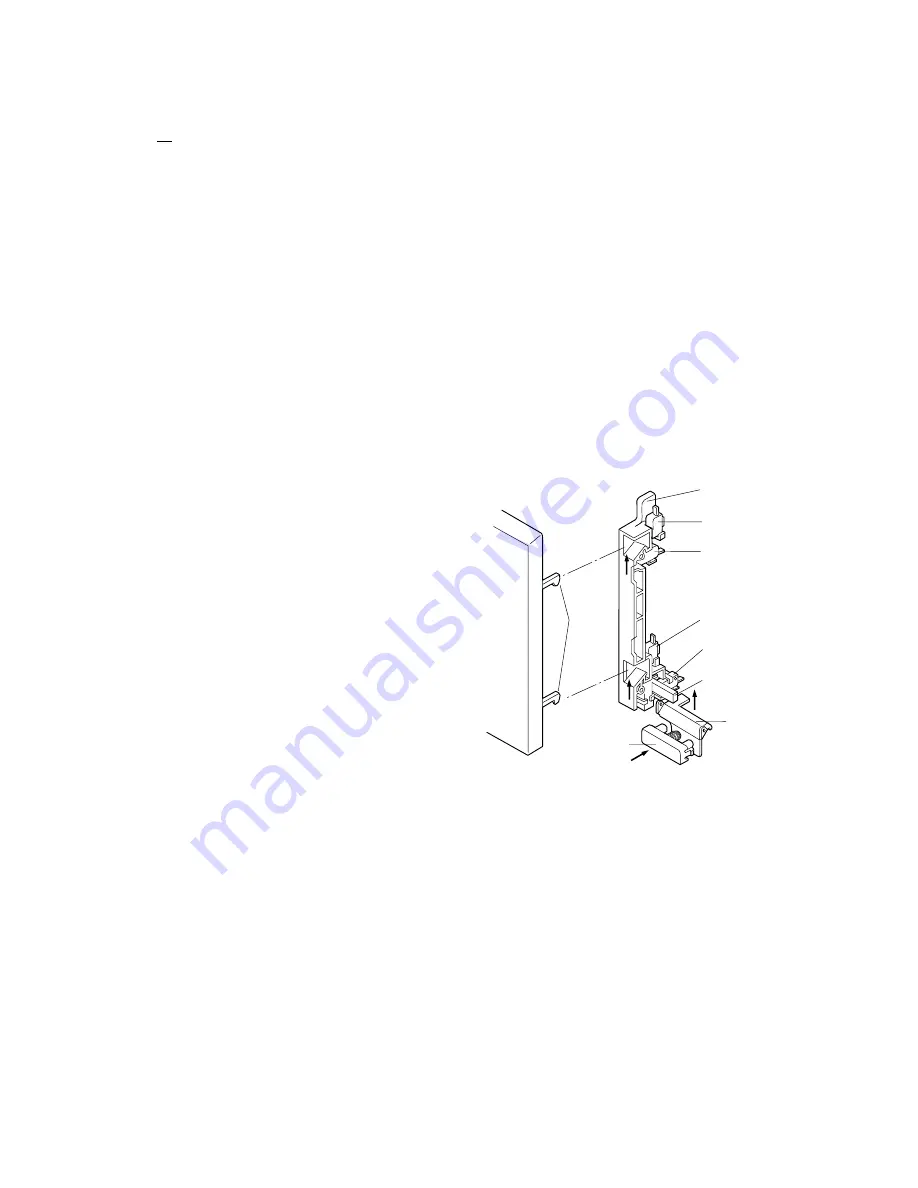
R990K(W)
10 – 5
[16] STOP SWITCH, UPPER LATCH SWITCH, LOWER LATCH SWITCH AND MONITOR
SWITCH REMOVAL
1. REMOVAL
1. CARRY OUT 3D CHECKS.
2. Remove control panel assembly, refer to “Control Panel Removal”.
3. Discharge high voltage capacitor.
4. Disconnect wire leads from each of the switches.
5. Remove two (2) screws holding latch hook to oven flange.
6. Remove latch hook assembly from oven flange.
7. Push downward on the one (1) stopper tabs holding each of the
switches place.
8. Switches are free.At this time latch lever will be free, do not lose it.
2. REINSTALL
1. Re-install latch lever and each switch in its place, refer to Figure C-
1.
2. Re-connect the wire leads to each switches and fuse holder.
Refer to the pictorial diagram.
3. Secure the latch hook (with two (2) mounting screws) to the oven
flange.
4. Make sure that monitor switch is operating properly.
Refer to chapter “Test Procedure” and Adjustment procedure.
[17] STOP SWITCH, UPPER LATCH SWITCH, LOWER LATCH SWITCH AND MONITOR
SWITCH ADJUSTMENT
1. Adjustment
If those switches do not operate properly due to a misadjustment, the
following adjustment should be made.
1. Loosen the two (2) screws holding the latch hook to the flange on
the oven front face.
2. With the door closed, adjust the latch hook by moving it back and
forth and then adjust the latch hook by moving it back and forth. In
and out play of the door allowed by the latch hook should be less
than 0.5 mm. The vertical position of the latch hook should be
adjusted so that the lower latch switch and stop switch are acti-
vated with the door closed. The horizontal position of the latch hook
should be adjusted so that the plunger of the monitor switch and
upper latch switch are pressed with the door closed.
3. Secure the screws with washers firmly.
4. Now, make sure all switches operations. If each switch has not
been activated with the door closed, loose the screws holding the
latch hook to the oven cavity front flange and adjust the latch hook
position.
2. After adjustment, check the following.
1. The in and out play of the door remains less than 0.5mm at latched
position.
2. The stop switch and lower latch switch interrupt the circuit before
the door can be opened.
3. The upper latch switch contacts open when the door is opened.
4. The monitor switch contacts close when the door is opened.
5. Re-install the outer case and check for microwave leakage around
the door with an approved microwave survey meter. (Refer to
Microwave Measurement Procedure.)
Figure C-1. Latch Switch Adjustments
[18] DOOR REPLACEMENT AND ADJUSTMENT
1. REPLACEMENT
1. 1.Disconnect oven from power supply and remove outer case.
2. Discharge high voltage capacitor.
3. Remove turntable tray and roller stay from oven cavity.
4. Remove three (3) screws holding lower oven hinge.
5. Remove lower oven hinge from oven cavity bottom flange.
6. Remove door assembly from upper oven hinge on the oven.
7. Door assembly is now free.
NOTE: When individual parts are replaced, refer to “Door Disassem-
bly”.
8. On re-installing door, insert the upper oven hinge into the door
hinge pin. Then while holding door in place.
9. Make sure door is parallel with oven face lines (left and upper side
lines) and the door latch heads pass through the latch holes cor-
rectly.
10.Insert the lower oven hinge into oven cavity bottom flange and then
engage the door hinge pin. Then secure the lower oven hinge firmly
with three (3) mounting screws.
NOTE: After any service to the door;
1) Make sure that the upper and lower latch switches, the
monitor switch and the stop switch are operating properly.
(Refer to chapter “Test Procedures”.)
2) An approved microwave survey meter should be used to
assure compliance with proper microwave radiation emis-
sion limitation standards.
2. DOOR ADJUSTMENT
The door is adjusted by keeping the screws of each hinge loose. The
lower oven hinge can be loosened.
After adjustment, make sure of the following:
LATCH HOOK
LATCH
HEADS
STOP SWITCH
MONITOR SWITCH
LOWER LATCH SWITCH
SWITCH LEVER
OPEN LEVER
DOOR OPEN
BUTTON
UPPER LATCH SWITCH
Summary of Contents for Carousel R-990K
Page 38: ...R990K W 12 6 MEMO ...